Located in Riverside, California, Blacoh Fluid Control Inc. manufactures pulsation dampeners, inlet stabilizers, back pressure valves and other products designed to move flow and reduce pulsation and shock in fluid systems. Because the products are tailored to individual needs, part runs are typically short and workpiece materials vary widely.
“We thread materials from 10/32" to 2.5" (7.94 mm to 63.5 mm) in diameter,” said Engineering Manager David McComb. “Materials range from metals, including stainless, Hastelloy, alloy 20 (a high-nickel-content material) and others, to PVC, CPVC, PTFE and the very expensive PVDF plastics.”
A key product line for the company is calibration columns, which have an end cap that is 177.8 mm (7") in diameter and require 12 threads per inch.
“The column houses a transparent tube and accompanying label imprinted with precise gradations to monitor the correct amount of fluoride, sodium hypochlorite or other chemical used in water or wastewater treatment,” McComb said.
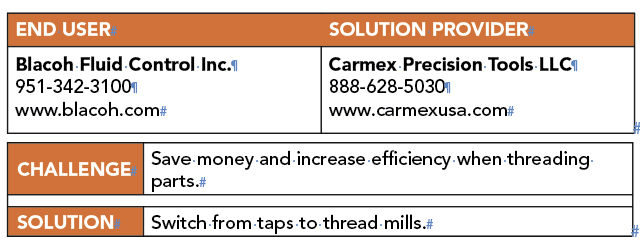
In selecting a tool supplier, he sought a manufacturer with a wide selection of off-the-shelf threading tools in a variety of sizes and configurations, which brought him to Hartford, Wisconsin-based Carmex Precision Tools LLC.
“I reasoned that a logistical approach involving the optimum selection of off-the-shelf threading tools encompassing all the sizes we need would result in the greatest economic benefit in terms of tool cost, as well as simplifying the supply chain and avoiding the high cost of special tooling,” McComb said. “It has also aided us in identifying the best tools for the job.”
“Thread milling and turning have always been Carmex’s greatest area of specialization,” said Leonard Ahumada, applications engineer at Carmex Precision Tools. “And as a result, we offer an extensive choice of tools extending from our Tiny Tool and Swiss tool lines, which are solid-carbide tools for working in small diameters, as well as larger indexable thread mills and specialty inserts for turning that are designed according to part print specifications. We worked with David to assist him in developing a matrix of 24 standardized tools in the machining center that accomplish all his machining needs, as well as the Blacoh thread milling requirements. An optimum selection of material-specific threading inserts and toolholders was also defined for use in the turning centers, where part runs are typically larger.”
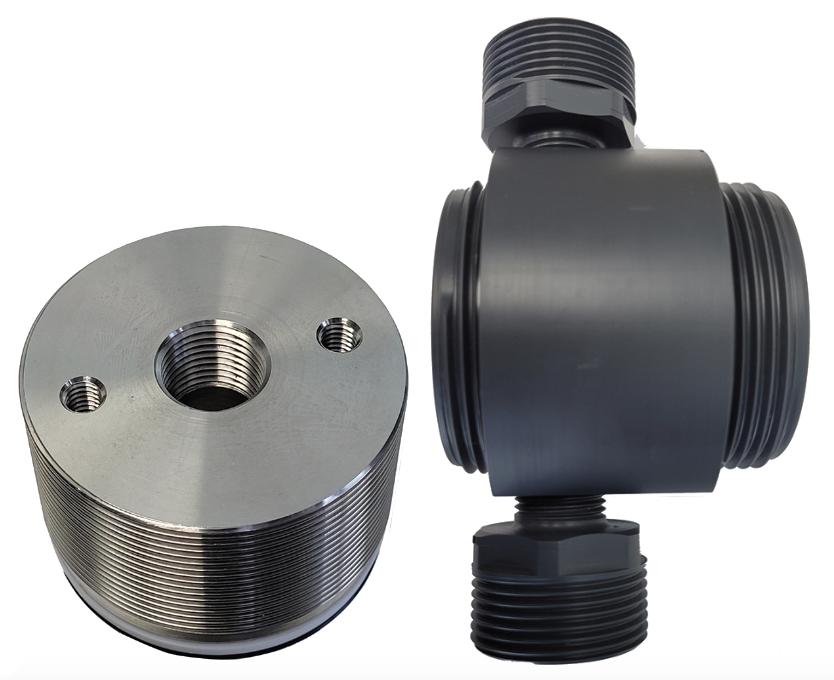
“By partnering with Carmex,” McComb said, “we’ve been able to achieve significant economies using standard tooling. We formerly used taps in our threading applications but ultimately found them to be expensive and less effective than thread milling. Tap breakage results in scrap parts, and a dull tap will score the material. This was a real problem for us as some of our materials, such as Hastelloy, have a hardness of 45 Rockwell.
“The tools we currently use are extremely precise, and we have been able to attain better diameter control and eliminate problems with shallow hole threading. Because we use indexable inserts, we can replace the inserts without needing to touch off the tools again.
“Our single-supplier relationship also delivers greater efficiencies, and Leonard and his team continually monitor our usage and needs.”
“David’s approach has been exceptionally valuable to Blacoh by taking a wide view that includes not only the tooling but the supply chain,” Ahumada said. “He has been able to optimize the threading process while deriving significant economic benefits.”
Contact Details
Related Glossary Terms
- calibration
calibration
Checking measuring instruments and devices against a master set to ensure that, over time, they have remained dimensionally stable and nominally accurate.
- centers
centers
Cone-shaped pins that support a workpiece by one or two ends during machining. The centers fit into holes drilled in the workpiece ends. Centers that turn with the workpiece are called “live” centers; those that do not are called “dead” centers.
- gang cutting ( milling)
gang cutting ( milling)
Machining with several cutters mounted on a single arbor, generally for simultaneous cutting.
- hardness
hardness
Hardness is a measure of the resistance of a material to surface indentation or abrasion. There is no absolute scale for hardness. In order to express hardness quantitatively, each type of test has its own scale, which defines hardness. Indentation hardness obtained through static methods is measured by Brinell, Rockwell, Vickers and Knoop tests. Hardness without indentation is measured by a dynamic method, known as the Scleroscope test.
- machining center
machining center
CNC machine tool capable of drilling, reaming, tapping, milling and boring. Normally comes with an automatic toolchanger. See automatic toolchanger.
- milling
milling
Machining operation in which metal or other material is removed by applying power to a rotating cutter. In vertical milling, the cutting tool is mounted vertically on the spindle. In horizontal milling, the cutting tool is mounted horizontally, either directly on the spindle or on an arbor. Horizontal milling is further broken down into conventional milling, where the cutter rotates opposite the direction of feed, or “up” into the workpiece; and climb milling, where the cutter rotates in the direction of feed, or “down” into the workpiece. Milling operations include plane or surface milling, endmilling, facemilling, angle milling, form milling and profiling.
- tap
tap
Cylindrical tool that cuts internal threads and has flutes to remove chips and carry tapping fluid to the point of cut. Normally used on a drill press or tapping machine but also may be operated manually. See tapping.
- threading
threading
Process of both external (e.g., thread milling) and internal (e.g., tapping, thread milling) cutting, turning and rolling of threads into particular material. Standardized specifications are available to determine the desired results of the threading process. Numerous thread-series designations are written for specific applications. Threading often is performed on a lathe. Specifications such as thread height are critical in determining the strength of the threads. The material used is taken into consideration in determining the expected results of any particular application for that threaded piece. In external threading, a calculated depth is required as well as a particular angle to the cut. To perform internal threading, the exact diameter to bore the hole is critical before threading. The threads are distinguished from one another by the amount of tolerance and/or allowance that is specified. See turning.
- turning
turning
Workpiece is held in a chuck, mounted on a face plate or secured between centers and rotated while a cutting tool, normally a single-point tool, is fed into it along its periphery or across its end or face. Takes the form of straight turning (cutting along the periphery of the workpiece); taper turning (creating a taper); step turning (turning different-size diameters on the same work); chamfering (beveling an edge or shoulder); facing (cutting on an end); turning threads (usually external but can be internal); roughing (high-volume metal removal); and finishing (final light cuts). Performed on lathes, turning centers, chucking machines, automatic screw machines and similar machines.