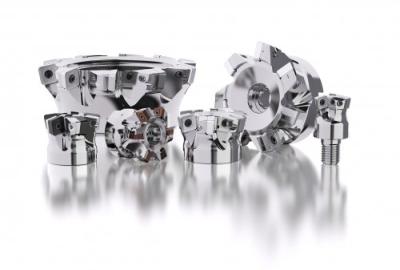
Milling challenging materials like tough steels, stainless steels, superalloys and titanium cause built-up or notched edges and broken inserts that increase tooling costs and cause unexpected downtime. To overcome these challenging ISO P, M and S materials, the new next-generation Seco High Feed SP milling system features a combination of dedicated cutting geometries and insert grades, as well as optimized lead angles, that combine to boost material removal rates, maximize chip evacuation and extend tool life.
Reduce tooling inventories
Packed with versatility, one High Feed SP tool handles a complete range of high feed milling operations and materials. The tool optimizes such operations as copy milling, ramping, pocketing, face milling and plunging to further reduce tooling inventories. Users optimize milling performance while eliminating the need to switch among numerous tools to implement various machining strategies and part materials.
“Premature tool wear increases job costs and leads to unexpected machine downtime that lengthens production time,” said Benoît Patriarca, Global Product Manager High Feed Milling at Seco Tools. “The combination of dedicated cutting geometries and grades with optimized leading angles of the High Feed SP system allow for faster machining to shorten job turnaround times, while also providing a superior price-to-performance ratio.”
Avoid downtime and scrapped parts
Designed for ease of use, the robust High Feed SP milling tools provide simple foolproof insert indexing that prevents operator mistakes, unexpected machine downtime and scrapped parts. Plus, users can quickly access product information through the Seco data matrix code scanning.
Seco offers a comprehensive range of High Feed SP tool sizes. The range includes:
- SP10: two geometries, 10 grades, dia 32 to 63mm + inch equivalents
- SP14: two geometries, 10 grades, dia 50 to 100mm + inch equivalents
- SP18: two geometries, 10 grades, dia 63 to 160mm + inch equivalents
Contact Details
Related Glossary Terms
- feed
feed
Rate of change of position of the tool as a whole, relative to the workpiece while cutting.
- gang cutting ( milling)
gang cutting ( milling)
Machining with several cutters mounted on a single arbor, generally for simultaneous cutting.
- milling
milling
Machining operation in which metal or other material is removed by applying power to a rotating cutter. In vertical milling, the cutting tool is mounted vertically on the spindle. In horizontal milling, the cutting tool is mounted horizontally, either directly on the spindle or on an arbor. Horizontal milling is further broken down into conventional milling, where the cutter rotates opposite the direction of feed, or “up” into the workpiece; and climb milling, where the cutter rotates in the direction of feed, or “down” into the workpiece. Milling operations include plane or surface milling, endmilling, facemilling, angle milling, form milling and profiling.
- stainless steels
stainless steels
Stainless steels possess high strength, heat resistance, excellent workability and erosion resistance. Four general classes have been developed to cover a range of mechanical and physical properties for particular applications. The four classes are: the austenitic types of the chromium-nickel-manganese 200 series and the chromium-nickel 300 series; the martensitic types of the chromium, hardenable 400 series; the chromium, nonhardenable 400-series ferritic types; and the precipitation-hardening type of chromium-nickel alloys with additional elements that are hardenable by solution treating and aging.
- superalloys
superalloys
Tough, difficult-to-machine alloys; includes Hastelloy, Inconel and Monel. Many are nickel-base metals.