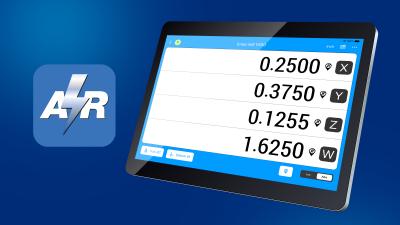
ACU-RITE announced that its new iOS app, droPWR, is now available in the Apple App Store. The app allows users to turn an ordinary iPad into a versatile digital readout console.
This advancement leverages ACU-RITE’s long-standing expertise and offerings in the DRO space—while taking flexibility and ease-of-use even further. Key benefits of the droPWR include:
- Provides intuitive user experience and touchscreen conventions
- Allows users to dynamically switch between milling, turning and grinding machines/applications to save time and money
- Allows multiple configurations on one tablet, with parameters set to each user
- On-boarding configuration easily walks the user through application setup
- Uses Bluetooth technology for wireless connectivity to encoders via an interface box
Two key user advantages of the droPWR app are split-screen functionality and dynamic zoom. The split-screen capability allows users to multitask—having more than one application displayed at a time (the readout application on one side and part print on the other, for example).
The dynamic zoom feature when enabled allows the user to visually see the position value of the current moving axis to greatly improve legibility—especially from a distance.
“ACU-RITE DROs allow manufacturers and educators to take their manual machines to the next level in terms of precision, productivity and overall potential,” says ACU-RITE Business Unit Manager, John Parker.
“The droPWR takes this to the next level, thanks to its versatility and multi-machine capabilities. It’s a perfect fit for classrooms and manufacturing environments of all kinds.”
Contact Details
Related Glossary Terms
- gang cutting ( milling)
gang cutting ( milling)
Machining with several cutters mounted on a single arbor, generally for simultaneous cutting.
- grinding
grinding
Machining operation in which material is removed from the workpiece by a powered abrasive wheel, stone, belt, paste, sheet, compound, slurry, etc. Takes various forms: surface grinding (creates flat and/or squared surfaces); cylindrical grinding (for external cylindrical and tapered shapes, fillets, undercuts, etc.); centerless grinding; chamfering; thread and form grinding; tool and cutter grinding; offhand grinding; lapping and polishing (grinding with extremely fine grits to create ultrasmooth surfaces); honing; and disc grinding.
- milling
milling
Machining operation in which metal or other material is removed by applying power to a rotating cutter. In vertical milling, the cutting tool is mounted vertically on the spindle. In horizontal milling, the cutting tool is mounted horizontally, either directly on the spindle or on an arbor. Horizontal milling is further broken down into conventional milling, where the cutter rotates opposite the direction of feed, or “up” into the workpiece; and climb milling, where the cutter rotates in the direction of feed, or “down” into the workpiece. Milling operations include plane or surface milling, endmilling, facemilling, angle milling, form milling and profiling.
- turning
turning
Workpiece is held in a chuck, mounted on a face plate or secured between centers and rotated while a cutting tool, normally a single-point tool, is fed into it along its periphery or across its end or face. Takes the form of straight turning (cutting along the periphery of the workpiece); taper turning (creating a taper); step turning (turning different-size diameters on the same work); chamfering (beveling an edge or shoulder); facing (cutting on an end); turning threads (usually external but can be internal); roughing (high-volume metal removal); and finishing (final light cuts). Performed on lathes, turning centers, chucking machines, automatic screw machines and similar machines.