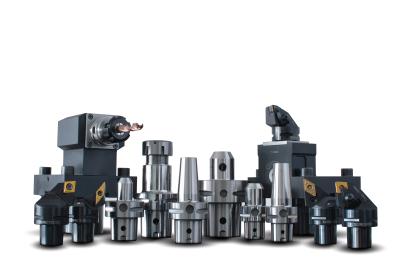
Lyndex-Nikken, manufacturer and provider of high-performance machine tool accessories, offers innovative Polygonal Shank Toolholders for increased stability and versatility in machining. Polygonal Shank Toolholders have a standardized interface as per ISO 26623 enabling extreme stability and a rigid connection between the tool and machine - ideal for all processes both in turning and milling.
As precisely defined per ISO 26623, the Polygon Shank Coupling (PSC) interface features a unique tapered polygon which serves as a main element in torque transmitting, centering, and clamping. With double contact on both face and taper, as well as great cross-sectional strength, this interface is unrivaled in terms of high clamping force and bending stiffness.
The combination of these excellent properties gives the PSC interface a clear advantage over HSK and 7/24 tapers with about 2x better bending and torsional characteristics. This translates into greater process stability, higher productivity, and lower costs.
Used in both standard turning centers and hybrid mill-turn machines, PSC turning toolholders enable a fast tool change solution for reduced downtime and increased productivity without compromising on stability and rigidity. Additionally, direct high pressure coolant nozzles increase tool life with higher feeds and speeds. This enables more time making chips and less time in unwanted stops – resulting in a fast ROI.
Key benefits of using PSC turning tools include:
- Reduced setup and tool change time - maximum utilization of the machine
- Increased stability and versatility - in vertical lathes, multi-tasking machining centers and machining centers with turning possibilities
- Ultimate repeatability - allowing online tool presetting
- Reduced tool inventory and storage space in workshop - due to universal interface for both turning and milling
- Self-centering system provides high precision and repeatability
- Carbide shims to prevent insert seats from damage
- Quick change, monobloc system without additional interfaces
Lyndex-Nikken Polygonal Shank Toolholders are available in 5 sizes, flange diameters 32-40-50-63-80 mm (sizes C3-C4-C5-C6-C8).
Contact Details
Related Glossary Terms
- centering
centering
1. Process of locating the center of a workpiece to be mounted on centers. 2. Process of mounting the workpiece concentric to the machine spindle. See centers.
- centers
centers
Cone-shaped pins that support a workpiece by one or two ends during machining. The centers fit into holes drilled in the workpiece ends. Centers that turn with the workpiece are called “live” centers; those that do not are called “dead” centers.
- coolant
coolant
Fluid that reduces temperature buildup at the tool/workpiece interface during machining. Normally takes the form of a liquid such as soluble or chemical mixtures (semisynthetic, synthetic) but can be pressurized air or other gas. Because of water’s ability to absorb great quantities of heat, it is widely used as a coolant and vehicle for various cutting compounds, with the water-to-compound ratio varying with the machining task. See cutting fluid; semisynthetic cutting fluid; soluble-oil cutting fluid; synthetic cutting fluid.
- gang cutting ( milling)
gang cutting ( milling)
Machining with several cutters mounted on a single arbor, generally for simultaneous cutting.
- milling
milling
Machining operation in which metal or other material is removed by applying power to a rotating cutter. In vertical milling, the cutting tool is mounted vertically on the spindle. In horizontal milling, the cutting tool is mounted horizontally, either directly on the spindle or on an arbor. Horizontal milling is further broken down into conventional milling, where the cutter rotates opposite the direction of feed, or “up” into the workpiece; and climb milling, where the cutter rotates in the direction of feed, or “down” into the workpiece. Milling operations include plane or surface milling, endmilling, facemilling, angle milling, form milling and profiling.
- shank
shank
Main body of a tool; the portion of a drill or similar end-held tool that fits into a collet, chuck or similar mounting device.
- stiffness
stiffness
1. Ability of a material or part to resist elastic deflection. 2. The rate of stress with respect to strain; the greater the stress required to produce a given strain, the stiffer the material is said to be. See dynamic stiffness; static stiffness.
- turning
turning
Workpiece is held in a chuck, mounted on a face plate or secured between centers and rotated while a cutting tool, normally a single-point tool, is fed into it along its periphery or across its end or face. Takes the form of straight turning (cutting along the periphery of the workpiece); taper turning (creating a taper); step turning (turning different-size diameters on the same work); chamfering (beveling an edge or shoulder); facing (cutting on an end); turning threads (usually external but can be internal); roughing (high-volume metal removal); and finishing (final light cuts). Performed on lathes, turning centers, chucking machines, automatic screw machines and similar machines.