Growing up in the ’70s I got to experience the digital revolution in its early stages. My generation got to see the first digital watches, play the first video games and watch numerous home computers hit the market.
Industry, although slowly, adapted to the changes. We have seen the proliferation of computer numerically controlled machines (aka CNCs), coordinate measuring machines (aka CMMs) take over inspection duties, and computers migrate from the engineering lab to the shop floor. Only a few short years ago it became widely accepted that we are in the fourth industrial revolution, which is driven by digitization and data analytics. Industry is accelerating the integration of digital technology into all areas of manufacturing beyond the ubiquitous CNCs and CMMs.
In the race to digitize we have seen cutting tool manufacturers get into the game with the introduction of digital boring tools. There are several manufacturers now offering digital boring heads that range in complexity. The simplest of these tools offer a digital readout that simplifies fine adjustments. The more complex tools offer wireless connections that tell the user what size the tool cutting is, calculates size adjustments and suggests cutting parameters.
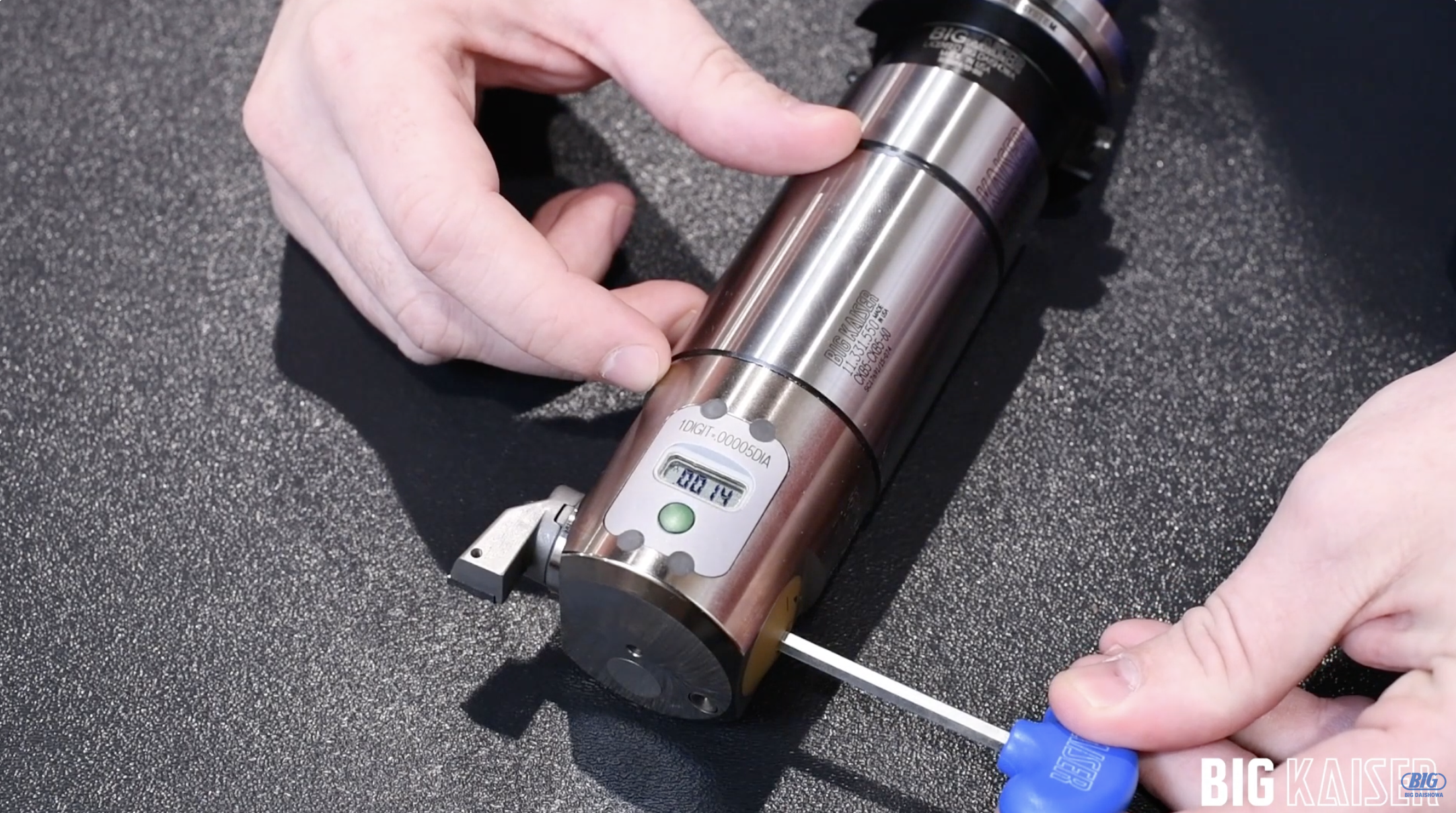
Digital boring tools offer one significant advantage to the user — they are very easy to read, which makes adjustment very precise. Making fine adjustments on an old-style boring head can be difficult as that requires the user to read a vernier scale. While effective, vernier scales can be difficult to read for inexperienced users as they are not very intuitive. In other cases, they can be difficult to see when mounted in the spindle of a large machine. These difficulties present significant opportunities for error and, ultimately, scrap. So making adjustments with old-style boring heads is inherently tedious and slow.
If you’re working with tight tolerances, that can mean taking several cuts to achieve the finished size. Because digital heads are easier to read, adjustments are more precise thereby reducing or eliminating the repetition of achieving final size, and reducing the risk associated with multiple passes. This also helps improve cycle times.
Many of the digital heads offer wireless connectivity allowing the user to read size from a mobile device, which means machinists can make adjustments with fewer ergonomic challenges. Having the ability to see and review settings outside the machine is a huge ergonomic improvement. No one likes climbing on a coolant covered machine table to read a boring head while trying to hold a few tenths on a gazillion-dollar part.
Digital boring heads improve the user experience and help reduce the risks of boring an oversized hole, but they are expensive. You cannot get into digital boring without spending a few thousand dollars. A basic set up with a boring head and a tool holder for the spindle can be purchased in a kit starting around $2,000 on the low side. If you need extensions, boring bars, inserts and other tooling items, the cost goes up. A single head gives the user infinite adjustability but only in a limited range so a large variation in diameters can necessitate multiple size boring heads. Likewise, multiple diameters in the same boring range can necessitate multiple bars of the same size. The cost of outfitting a shop with these tools can escalate quickly making financial justification difficult.
Digital heads are desirable because they speed up the repetition and precision of the boring process. Consider how this process plays out. The machinist bores a hole, measures the diameter, adjusts the boring head and then repeats. Two-thousand-dollar boring heads are probably going to be run on CNC machines. It is also likely the hole tolerances are very tight so, frequent measurement and adjustment routines are occurring. The result is frequent mid-program stops and starts. Each time the machinist restarts that program there is a chance that a tool length is not read, or the program is started out of sequence, which risks crashing the boring head into something. Unlike conventional boring heads that can be repaired in the shop, these new digital heads will need to be sent back to the manufacturer. And there is a chance they cannot be fixed.
Ease of use, precision and speed are the primary benefits touted by the manufacturers. All are accurate. However, these tools are somewhat a novelty, and the benefits may not outweigh the costs.
Should you invest in a digital boring head? It depends.
I had the opportunity to bore some holes in our shop this week. Of course, I was thinking about this article, which made me very aware of the old-fashioned boring head I was using. You know, the black and sliver version that lives around the old knee mill in every shop. A digital would have been very handy. However, a digital boring head would have been far more accurate than the old mill I was using. So, using a digital head on machines that are less accurate negates any benefit and makes financial justification difficult.
Digital boring heads are not the right tool for high volume hole sizing. There are tools on the market that are just as accurate that perform better in high volume machining applications. For smaller volumes with some variation in hole sizes inside a small range, a digital boring head might be a good option.
Digital boring is a practical choice in very low volume machining of expensive parts with a large variation in close tolerance hole diameters. They offer an excellent way to mitigate risky boring operations. They may also be a good choice for a shop that routinely does fine boring and is looking to replace older or damaged analog heads with something more efficient.
Used in the right environment for the right application, digital boring tools can be beneficial but the cost is still prohibitive. Like everything else, they will eventually become more affordable, and I suspect they will also become as common as digital calipers and micrometers.
Contact Details
Related Glossary Terms
- boring
boring
Enlarging a hole that already has been drilled or cored. Generally, it is an operation of truing the previously drilled hole with a single-point, lathe-type tool. Boring is essentially internal turning, in that usually a single-point cutting tool forms the internal shape. Some tools are available with two cutting edges to balance cutting forces.
- boring head
boring head
Single- or multiple-point precision tool used to bring an existing hole within dimensional tolerance. The head attaches to a standard toolholder and a mechanism permits fine adjustments to be made to the head within a diameter range.
- computer numerical control ( CNC)
computer numerical control ( CNC)
Microprocessor-based controller dedicated to a machine tool that permits the creation or modification of parts. Programmed numerical control activates the machine’s servos and spindle drives and controls the various machining operations. See DNC, direct numerical control; NC, numerical control.
- coolant
coolant
Fluid that reduces temperature buildup at the tool/workpiece interface during machining. Normally takes the form of a liquid such as soluble or chemical mixtures (semisynthetic, synthetic) but can be pressurized air or other gas. Because of water’s ability to absorb great quantities of heat, it is widely used as a coolant and vehicle for various cutting compounds, with the water-to-compound ratio varying with the machining task. See cutting fluid; semisynthetic cutting fluid; soluble-oil cutting fluid; synthetic cutting fluid.
- milling machine ( mill)
milling machine ( mill)
Runs endmills and arbor-mounted milling cutters. Features include a head with a spindle that drives the cutters; a column, knee and table that provide motion in the three Cartesian axes; and a base that supports the components and houses the cutting-fluid pump and reservoir. The work is mounted on the table and fed into the rotating cutter or endmill to accomplish the milling steps; vertical milling machines also feed endmills into the work by means of a spindle-mounted quill. Models range from small manual machines to big bed-type and duplex mills. All take one of three basic forms: vertical, horizontal or convertible horizontal/vertical. Vertical machines may be knee-type (the table is mounted on a knee that can be elevated) or bed-type (the table is securely supported and only moves horizontally). In general, horizontal machines are bigger and more powerful, while vertical machines are lighter but more versatile and easier to set up and operate.
- tolerance
tolerance
Minimum and maximum amount a workpiece dimension is allowed to vary from a set standard and still be acceptable.