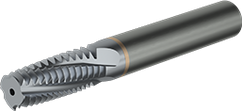
The Vargus Mach TM is a high-performance thread milling tool engineered to enhance machining productivity and efficiency. Designed with advanced features, it is ideal for demanding applications requiring precise threading and superior surface finish.
Key Advantages:
-
High Feed Rate: Allows for more material removal per flute.
-
Reduced Machining Time: Significantly shortens cycle times.
-
Extended Tool Life: Enhanced durability for prolonged use.
-
Excellent Surface Finish: Ensures superior finish quality.
Features:
-
Improved Cutting Edge & Reinforced Geometry: For handling high loads.
-
Coolant Thru Design: Enhances chip flow and surface finish.
-
Large Core Diameter: Increases stability.
-
Additional Flutes: Enables higher feed rates.
-
Advanced Surface Treatment: Strengthens cutting edges and improves finish.
-
Optimal Flute Length: Provides higher rigidity and efficient chip evacuation.
For more details, visit the Vargus Mach TM page.
Contact Details
Related Glossary Terms
- coolant
coolant
Fluid that reduces temperature buildup at the tool/workpiece interface during machining. Normally takes the form of a liquid such as soluble or chemical mixtures (semisynthetic, synthetic) but can be pressurized air or other gas. Because of water’s ability to absorb great quantities of heat, it is widely used as a coolant and vehicle for various cutting compounds, with the water-to-compound ratio varying with the machining task. See cutting fluid; semisynthetic cutting fluid; soluble-oil cutting fluid; synthetic cutting fluid.
- feed
feed
Rate of change of position of the tool as a whole, relative to the workpiece while cutting.
- gang cutting ( milling)
gang cutting ( milling)
Machining with several cutters mounted on a single arbor, generally for simultaneous cutting.
- milling
milling
Machining operation in which metal or other material is removed by applying power to a rotating cutter. In vertical milling, the cutting tool is mounted vertically on the spindle. In horizontal milling, the cutting tool is mounted horizontally, either directly on the spindle or on an arbor. Horizontal milling is further broken down into conventional milling, where the cutter rotates opposite the direction of feed, or “up” into the workpiece; and climb milling, where the cutter rotates in the direction of feed, or “down” into the workpiece. Milling operations include plane or surface milling, endmilling, facemilling, angle milling, form milling and profiling.
- threading
threading
Process of both external (e.g., thread milling) and internal (e.g., tapping, thread milling) cutting, turning and rolling of threads into particular material. Standardized specifications are available to determine the desired results of the threading process. Numerous thread-series designations are written for specific applications. Threading often is performed on a lathe. Specifications such as thread height are critical in determining the strength of the threads. The material used is taken into consideration in determining the expected results of any particular application for that threaded piece. In external threading, a calculated depth is required as well as a particular angle to the cut. To perform internal threading, the exact diameter to bore the hole is critical before threading. The threads are distinguished from one another by the amount of tolerance and/or allowance that is specified. See turning.