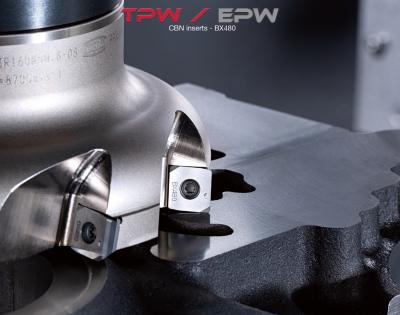
Tungaloy Corporation (President: Satoshi Kinoshita, Headquarters: Iwaki City, Fukushima Prefecture) is pleased to announce the addition of CBN inserts for high-speed cast iron finishing to its "TPW / EPW Type" milling cutter series.
Overview
The "TPW / EPW Type" series features a 4-corner insert design that balances sharpness and edge strength, enabling high-precision, high-efficiency machining. With a 90-degree cutting edge angle (KAPR), these cutters excel not only in square shoulder milling but also in face milling around obstacles and fixtures. The inserts are available in four types, including the versatile "MJ Type," ensuring stable performance across a wide range of materials.
The cutter bodies come in both bore type "TPW Type" and shank type "EPW Type," covering tool diameters from φ32 to φ200mm (from φ1.260” to φ7.874”). Additionally, both of coarse pitch type and close pitch type are available, allowing users to select the optimal tool based on their machining conditions.
The new addition to the "TPW / EPW Type" series includes CBN inserts designed for high-speed cast iron finishing. In addition to the economical 2-corner standard insert, a wiper insert option is also available to achieve excellent surface finish. The insert grade is High-content CBN "BX480," which consists of densely bonded medium-grain CBN. This grade offers high hardness, toughness, and superior thermal conductivity, making it suitable for high-speed machining at cutting speeds (Vc) exceeding 1000m/min.
The expansion of the CBN inserts for high-speed cast iron finishing will enable the "TPW / EPW Type" cutters to significantly contribute to reducing machining time and improving productivity across a wider range of industries through high-efficiency machining.
Contact Details
Related Glossary Terms
- cubic boron nitride ( CBN)
cubic boron nitride ( CBN)
Crystal manufactured from boron nitride under high pressure and temperature. Used to cut hard-to-machine ferrous and nickel-base materials up to 70 HRC. Second hardest material after diamond. See superabrasive tools.
- gang cutting ( milling)
gang cutting ( milling)
Machining with several cutters mounted on a single arbor, generally for simultaneous cutting.
- hardness
hardness
Hardness is a measure of the resistance of a material to surface indentation or abrasion. There is no absolute scale for hardness. In order to express hardness quantitatively, each type of test has its own scale, which defines hardness. Indentation hardness obtained through static methods is measured by Brinell, Rockwell, Vickers and Knoop tests. Hardness without indentation is measured by a dynamic method, known as the Scleroscope test.
- milling
milling
Machining operation in which metal or other material is removed by applying power to a rotating cutter. In vertical milling, the cutting tool is mounted vertically on the spindle. In horizontal milling, the cutting tool is mounted horizontally, either directly on the spindle or on an arbor. Horizontal milling is further broken down into conventional milling, where the cutter rotates opposite the direction of feed, or “up” into the workpiece; and climb milling, where the cutter rotates in the direction of feed, or “down” into the workpiece. Milling operations include plane or surface milling, endmilling, facemilling, angle milling, form milling and profiling.
- milling cutter
milling cutter
Loosely, any milling tool. Horizontal cutters take the form of plain milling cutters, plain spiral-tooth cutters, helical cutters, side-milling cutters, staggered-tooth side-milling cutters, facemilling cutters, angular cutters, double-angle cutters, convex and concave form-milling cutters, straddle-sprocket cutters, spur-gear cutters, corner-rounding cutters and slitting saws. Vertical cutters use shank-mounted cutting tools, including endmills, T-slot cutters, Woodruff keyseat cutters and dovetail cutters; these may also be used on horizontal mills. See milling.
- pitch
pitch
1. On a saw blade, the number of teeth per inch. 2. In threading, the number of threads per inch.
- shank
shank
Main body of a tool; the portion of a drill or similar end-held tool that fits into a collet, chuck or similar mounting device.
- wiper
wiper
Metal-removing edge on the face of a cutter that travels in a plane perpendicular to the axis. It is the edge that sweeps the machined surface. The flat should be as wide as the feed per revolution of the cutter. This allows any given insert to wipe the entire workpiece surface and impart a fine surface finish at a high feed rate.