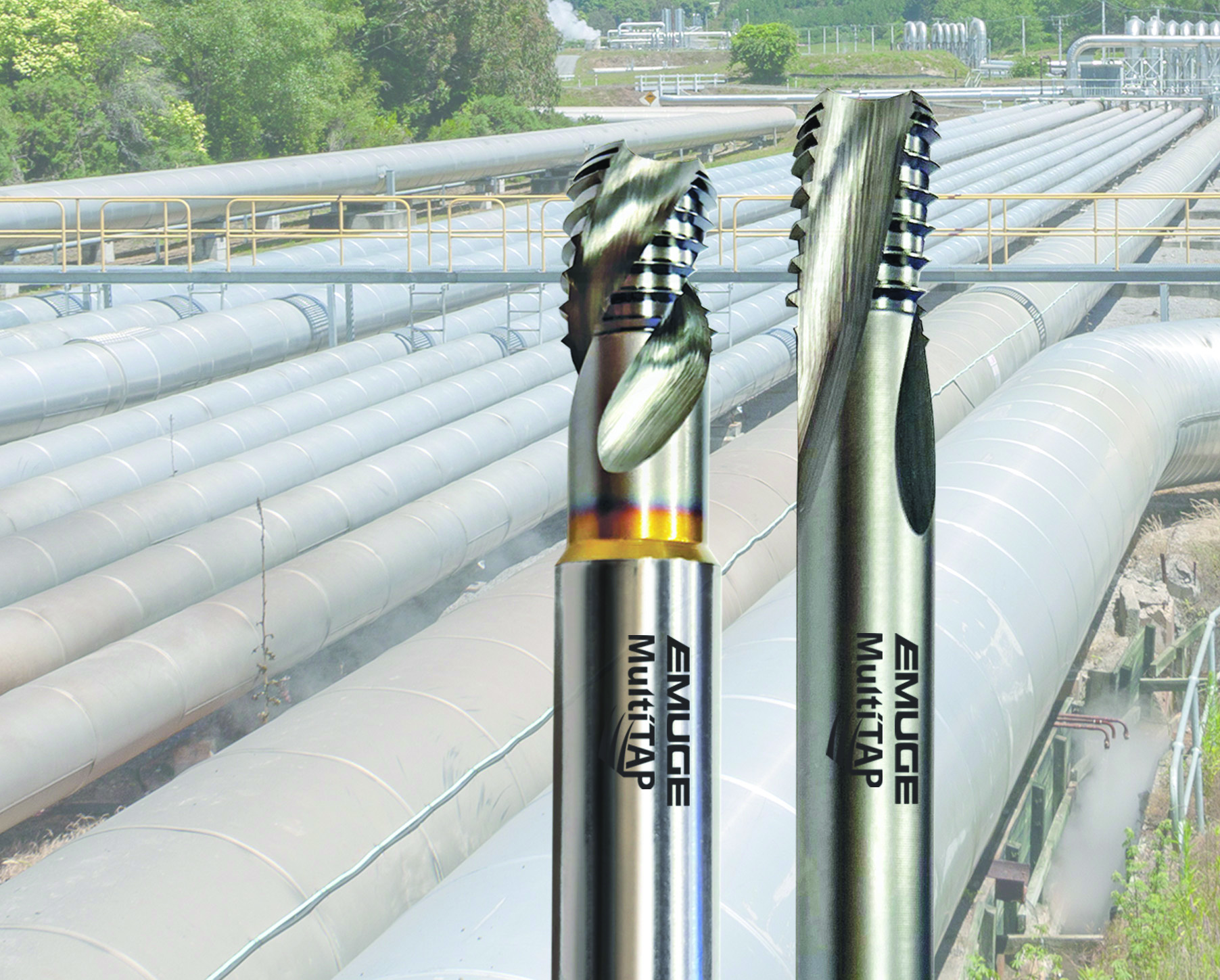
Emuge-Franken USA, a manufacturer of high-performance taps, thread mills, drills, end mills, clamping devices and other rotary tools, has introduced new MultiTAP NPT/NPTF Pipe Taps with a universal threading geometry for both job shops and production tapping. The taps feature a specially engineered shortened projection length when compared to traditional ANSI standard taper taps, decreasing cycle time
and increasing tool life, while meeting all industry-standard requirements for gaging. The new taps are stocked in the U.S.
“We are pleased to offer energy manufacturers a versatile pipe tapping solution designed to meet and exceed even the most difficult applications for the oil, gas, and petrochemical manufacturing sectors,” said Dylan Bowles, product director, EMUGE-FRANKEN USA.
The new taps are also well-suited for food and dairy equipment, high-pressure pipe delivery systems, valves, and fire suppression systems. The MultiTAP line of NPT/ NPFT Pipe Taps offers an interrupted skip tooth thread profile that helps to reduce cutting forces and chip clogging. The new taps feature a premium HSSE base tool substrate and a proprietary TICN-PVD coating to extend tool life. The pipe taps are designed with a C-style semi-bottoming chamfer length of 2-3 teeth, as well as an enhanced flute helix angle to meet the needs of NPT (Right Hand 35° helix) and NPTF (Right Hand 15° helix) thread profiles.
For more information on the new MultiTAP NPT/NPTF Pipe Taps, click here.
Contact Details
Related Glossary Terms
- helix angle
helix angle
Angle that the tool’s leading edge makes with the plane of its centerline.
- tapping
tapping
Machining operation in which a tap, with teeth on its periphery, cuts internal threads in a predrilled hole having a smaller diameter than the tap diameter. Threads are formed by a combined rotary and axial-relative motion between tap and workpiece. See tap.
- threading
threading
Process of both external (e.g., thread milling) and internal (e.g., tapping, thread milling) cutting, turning and rolling of threads into particular material. Standardized specifications are available to determine the desired results of the threading process. Numerous thread-series designations are written for specific applications. Threading often is performed on a lathe. Specifications such as thread height are critical in determining the strength of the threads. The material used is taken into consideration in determining the expected results of any particular application for that threaded piece. In external threading, a calculated depth is required as well as a particular angle to the cut. To perform internal threading, the exact diameter to bore the hole is critical before threading. The threads are distinguished from one another by the amount of tolerance and/or allowance that is specified. See turning.