Contact Details
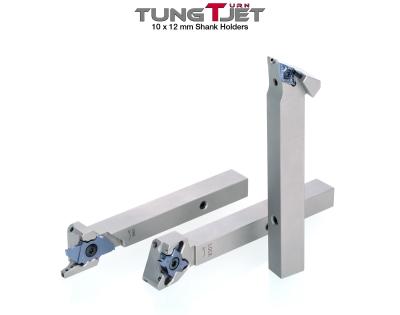
Tungaloy is expanding its TungTurn-Jet series of turning toolholders by adding 10x12 mm shank designed specifically for the use on Swiss-type lathes enabling high-pressure coolant supply through the toolholder directly from the machine without an external coolant hose connection.
TungTurn-Jet toolholders deliver coolant strategically to the optimum position close to the cutting point of the insert. This significantly improves chip control when machining exotic materials that are prone to smearing by effectively breaking the chips into pieces and guiding them away from the cut, which was difficult using a traditional external coolant nozzle method. Additionally, TungTurn-Jet features a second coolant outlet from the insert clearance side which not only improves chip control but also helps minimize flank wear for increased insert life and productivity.
The new 10x12 mm shank toolholders are able to channel coolant directly from the machine tool into the tool holder and out through the nozzle. This technology can eliminate the need for an external coolant hose connection, which often causes unwanted chip accumulations in the tooling area that can easily stall production. The new toolholders provide internal coolant supply but can still be used with an external coolant hose.
The new toolholders can be used on any Swiss-type lathes that have 10x10mm positions on the turning tool post. This addition, along with existing 12x12 mm and 20x20 mm shanks, now offer a complete range of TungTurn-Jet high pressure coolant-through solutions for Swiss-type lathe operations. The new toolholders are available for front-turning, grooving, parting, and thread-turning operations.
At a Glance
- Able to supply coolant through the toolholder directly from the machine tool without an external hose connection
- High-pressure jet of coolant effectively fragments chips into pieces for easy removal, allowing shops to experience high level of productivity
- By strategically directing the coolant jets to the optimum position close to the cutting point, the control of chips and insert wear is significantly improved
- 7 toolholders to be added
Related Glossary Terms
- clearance
clearance
Space provided behind a tool’s land or relief to prevent rubbing and subsequent premature deterioration of the tool. See land; relief.
- coolant
coolant
Fluid that reduces temperature buildup at the tool/workpiece interface during machining. Normally takes the form of a liquid such as soluble or chemical mixtures (semisynthetic, synthetic) but can be pressurized air or other gas. Because of water’s ability to absorb great quantities of heat, it is widely used as a coolant and vehicle for various cutting compounds, with the water-to-compound ratio varying with the machining task. See cutting fluid; semisynthetic cutting fluid; soluble-oil cutting fluid; synthetic cutting fluid.
- flank wear
flank wear
Reduction in clearance on the tool’s flank caused by contact with the workpiece. Ultimately causes tool failure.
- grooving
grooving
Machining grooves and shallow channels. Example: grooving ball-bearing raceways. Typically performed by tools that are capable of light cuts at high feed rates. Imparts high-quality finish.
- lathe
lathe
Turning machine capable of sawing, milling, grinding, gear-cutting, drilling, reaming, boring, threading, facing, chamfering, grooving, knurling, spinning, parting, necking, taper-cutting, and cam- and eccentric-cutting, as well as step- and straight-turning. Comes in a variety of forms, ranging from manual to semiautomatic to fully automatic, with major types being engine lathes, turning and contouring lathes, turret lathes and numerical-control lathes. The engine lathe consists of a headstock and spindle, tailstock, bed, carriage (complete with apron) and cross slides. Features include gear- (speed) and feed-selector levers, toolpost, compound rest, lead screw and reversing lead screw, threading dial and rapid-traverse lever. Special lathe types include through-the-spindle, camshaft and crankshaft, brake drum and rotor, spinning and gun-barrel machines. Toolroom and bench lathes are used for precision work; the former for tool-and-die work and similar tasks, the latter for small workpieces (instruments, watches), normally without a power feed. Models are typically designated according to their “swing,” or the largest-diameter workpiece that can be rotated; bed length, or the distance between centers; and horsepower generated. See turning machine.
- parting
parting
When used in lathe or screw-machine operations, this process separates a completed part from chuck-held or collet-fed stock by means of a very narrow, flat-end cutting, or parting, tool.
- shank
shank
Main body of a tool; the portion of a drill or similar end-held tool that fits into a collet, chuck or similar mounting device.
- toolholder
toolholder
Secures a cutting tool during a machining operation. Basic types include block, cartridge, chuck, collet, fixed, modular, quick-change and rotating.
- turning
turning
Workpiece is held in a chuck, mounted on a face plate or secured between centers and rotated while a cutting tool, normally a single-point tool, is fed into it along its periphery or across its end or face. Takes the form of straight turning (cutting along the periphery of the workpiece); taper turning (creating a taper); step turning (turning different-size diameters on the same work); chamfering (beveling an edge or shoulder); facing (cutting on an end); turning threads (usually external but can be internal); roughing (high-volume metal removal); and finishing (final light cuts). Performed on lathes, turning centers, chucking machines, automatic screw machines and similar machines.