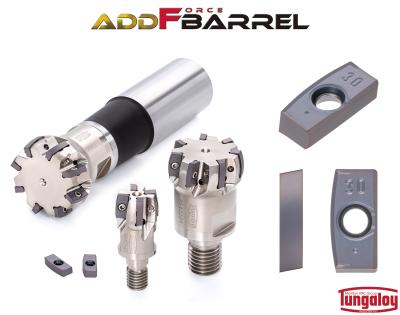
Tungaloy has unveiled AddForceBarrel indexable profile milling cutters with barrel-shaped cutting edges that are designed for efficient semi-finish machining of 3D surfaces.
Following the success of TungMeister barrel shape milling head series, which were developed for efficient finish profiling of 3D surfaces such as of complex dies and turbomachinery components in 5-axis milling operations, Tungaloy furthered the same design principle to engineer AddForceBarrel for an indexable insert solution.
AddForceBarrel uses inserts whose cutting edges have a large-radius arc of either 20 mm (.787″) or 30 mm (1.181″), designed for semi-finish profiling of 3D surfaces. Just like the TungMeister’s barrel milling heads, AddForceBarrel provides much greater engagement area between the cutting edge and workpiece when compared with conventional ballnose end mills. Greater engagement area enables larger stepovers, which improves metal removal rates for reduced number of cutter passes and cycle times.
Double-sided with two total cutting edges and ground-to-precision, AddForceBarrel inserts come in extremely small body of size 10 with cutting edges comprised of a large-radius arc, which are developed with high powder-sintering and grinding technologies unique to Tungaloy. These small-size inserts enable high tooth density, allowing a 20 mm-diameter cutter to carry four inserts. On the other hand, their cutting edge is long enough so that the 20 mm-radius insert can be set to an optimal tilt angle at up to 21.5 degrees relative to the plane being machined and the 30 mm-radius insert at up to 16 degrees.
Furthermore, the inserts are designed to provide wide contacts with the seat when screw-clamped on the cutter, ensuring strong insert retention and part precision.
The inserts are offered in AH9130, a latest PVD-coated grade that provides long and predictable tool life in carbon steel, stainless steel, as well as hardened steel.
Contact Details
Related Glossary Terms
- gang cutting ( milling)
gang cutting ( milling)
Machining with several cutters mounted on a single arbor, generally for simultaneous cutting.
- grinding
grinding
Machining operation in which material is removed from the workpiece by a powered abrasive wheel, stone, belt, paste, sheet, compound, slurry, etc. Takes various forms: surface grinding (creates flat and/or squared surfaces); cylindrical grinding (for external cylindrical and tapered shapes, fillets, undercuts, etc.); centerless grinding; chamfering; thread and form grinding; tool and cutter grinding; offhand grinding; lapping and polishing (grinding with extremely fine grits to create ultrasmooth surfaces); honing; and disc grinding.
- indexable insert
indexable insert
Replaceable tool that clamps into a tool body, drill, mill or other cutter body designed to accommodate inserts. Most inserts are made of cemented carbide. Often they are coated with a hard material. Other insert materials are ceramic, cermet, polycrystalline cubic boron nitride and polycrystalline diamond. The insert is used until dull, then indexed, or turned, to expose a fresh cutting edge. When the entire insert is dull, it is usually discarded. Some inserts can be resharpened.
- milling
milling
Machining operation in which metal or other material is removed by applying power to a rotating cutter. In vertical milling, the cutting tool is mounted vertically on the spindle. In horizontal milling, the cutting tool is mounted horizontally, either directly on the spindle or on an arbor. Horizontal milling is further broken down into conventional milling, where the cutter rotates opposite the direction of feed, or “up” into the workpiece; and climb milling, where the cutter rotates in the direction of feed, or “down” into the workpiece. Milling operations include plane or surface milling, endmilling, facemilling, angle milling, form milling and profiling.
- profiling
profiling
Machining vertical edges of workpieces having irregular contours; normally performed with an endmill in a vertical spindle on a milling machine or with a profiler, following a pattern. See mill, milling machine.