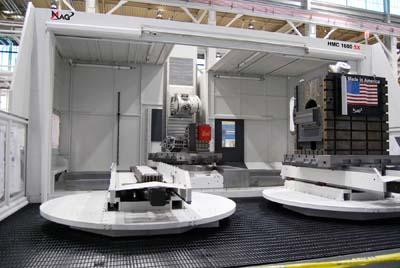
MAG's modular HMC 1250/1600 Series is engineered for high-precision, high-productivity machining of large aerospace, power generation, pump, valve, and off-road equipment parts. It now includes eight spindle options to suit special-purpose or general machining requirements. The new 6000 and 8000 rpm/46-kW (61.6-hp) tilt-spindles – with +90/-120 degree A-axis travel – joins an all-around 10,000 rpm/ 46-kW (62-hp) spindle, high-speed 24,000 rpm spindle, high-torque 2600 Nm/80-kW (1918 ft lb) spindle and two live spindles (110 or 130mm diameter). The high-torque spindle is especially suited for hard-metal cutting, while the live spindles extend W-axis reach by up to 800mm (31.5 in), enabling deep cavity milling to high precision with shorter, more rigid tools. Standard on the live spindle, MAG's exclusive Z-axis thermal compensation software dynamically offsets spindle growth to maintain tight tolerances.
Designed for application flexibility, the HMC 1250/1600 offers maximum 3000mm (118 in) work-zone swing, and 15,000 kg (33,000 lb) pallet load capacity. Major machine components, including the X-bed, Z-bed and column, are cast ductile iron, with pallets up to 1600 x 2000mm, headstock and rotary table housings of gray cast iron. Modular design provides a range of machine travels, 60- to 300-tool magazines and two control choices.
The new 5-axis HMC offers 56 to 100 kW (75 to 133 hp) spindle power, 35 kN (7870 lb) Z-axis thrust, and super-rigid, full-contouring hydrostatic rotary table. The 360,000-position contouring table provides a rigid work platform, while a rugged worm gear drive with clamp securely holds axis position. Rotary table positioning accuracy is 10 arc seconds, repeatable to 5 arc seconds. Positioning accuracy of the tilt-spindle is 4 arc seconds, repeatable to 2 arc seconds.
Meeting industry needs for tighter part tolerances and greater machining accuracies, the HMC Series comes standard with linear scale feedback in X, Y and Z axes, providing 8µm (0.0003 in) positioning accuracy and 5µm (0.0002 in) repeatability. Heavy-duty hardened and ground roller guide ways enable a rapid traverse rate of up to 40 m/min (1575 ipm) with high acc/dec rates, double the load capacity and nearly 10 times the wear life of ball-type ways. The full work zone enclosure is pre-engineered to provide a clean machining environment and includes a doorway for operator access with walkway/platform inside.
Contact Details
Related Glossary Terms
- gang cutting ( milling)
gang cutting ( milling)
Machining with several cutters mounted on a single arbor, generally for simultaneous cutting.
- milling
milling
Machining operation in which metal or other material is removed by applying power to a rotating cutter. In vertical milling, the cutting tool is mounted vertically on the spindle. In horizontal milling, the cutting tool is mounted horizontally, either directly on the spindle or on an arbor. Horizontal milling is further broken down into conventional milling, where the cutter rotates opposite the direction of feed, or “up” into the workpiece; and climb milling, where the cutter rotates in the direction of feed, or “down” into the workpiece. Milling operations include plane or surface milling, endmilling, facemilling, angle milling, form milling and profiling.
- modular design ( modular construction)
modular design ( modular construction)
Manufacturing of a product in subassemblies that permits fast and simple replacement of defective assemblies and tailoring of the product for different purposes. See interchangeable parts.
- rapid traverse
rapid traverse
Movement on a CNC mill or lathe that is from point to point at full speed but, usually, without linear interpolation.