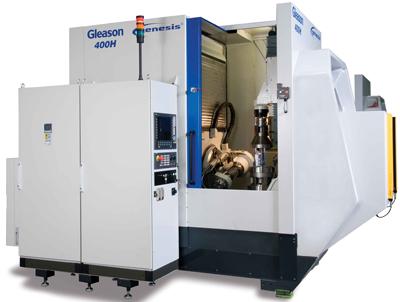
The new Genesis 400H gear hobbing machine for workpieces up to 400mm in diameter and module 8mm supplements Gleason's successful line of Genesis hobbing machines in the medium-sized workpiece range. The 400H is designed for the manufacture of gears in truck, agriculture and construction applications as well as universal job shop tasks of similar size and module range.
The machine combines proven features with latest technologies to raise productivity to new levels. The 400H features high-speed drives to utilize the most advanced cutting tools available on the market, including high speed steel and carbide hobs including Gleason's new G90 hobs. Designed for dry or wet hobbing, its clean work area ensures that dry chips or cutting residue are effectively removed from the work area.
The machine can be configured individually to respond to customers' application requirements with automatic loading and conveyor options. In addition to regular hobbing processes, the 400H employs process options for form milling/gashing, cutting of multiple/cluster gears, skive hobbing and more. Optionally the 400H can be equipped with a smart solution for integrated chamfering and deburring.
The machine is fitted with either dry or wet chip evacuation systems and the respective dust or mist filter options. The whole work area has been designed with optimum ergonomics in mind and is easily accessible including a simple tool change mechanism unique for a machine of such size. The integrated power clamping system allows for the adaption of a wide range of workholding systems including the new Gleason Quik-Flex Plus workholding for workpiece changes in less than 30 seconds.
The 400H is supported by the Gleason Global Service network with strategically located spare parts centers and over 250 service professionals in all major markets worldwide. Gleason provides application support, cutting tools and workholding all from a single source.
Contact Details
Related Glossary Terms
- centers
centers
Cone-shaped pins that support a workpiece by one or two ends during machining. The centers fit into holes drilled in the workpiece ends. Centers that turn with the workpiece are called “live” centers; those that do not are called “dead” centers.
- chamfering
chamfering
Machining a bevel on a workpiece or tool; improves a tool’s entrance into the cut.