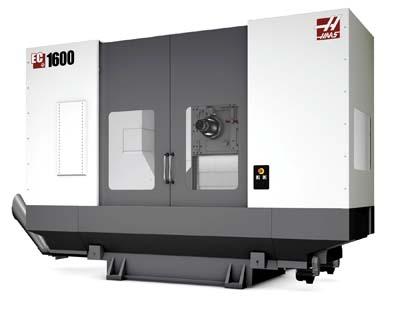
As the aerospace, automotive, and mold-and-die industries trend toward monolithic components and large structures, there is a growing need for large-travel machining centers. To accommodate large-volume machining, Haas Automation Inc. has expanded the capacity of its EC-1600 horizontal machining center with an additional 10" of Y-axis travel. The latest generation Haas EC-1600 HMC features a generous 64"x50"x32" work cube--10 more inches of Y-axis travel than before--as well as a 64"x32" T-slot table and a 6,000-rpm, geared-head, 50-taper spindle. The fully enclosed machine includes multiple chip augers to evacuate chips, and a flood coolant system with 95-gal. capacity. The EC-1600's cast-iron construction increases rigidity and damps vibration, and the standard T-slot table supports parts weighing up to 10,000 lb. The 50-taper geared-head spindle is powered by a 30-hp vector drive system, providing 450 ft.-lbs. of torque for heavy cutting. A 30+1 side-mount tool changer is standard, as well as a color LCD remote jog handle, rigid tapping, 1MB of program memory, a 15" color LCD monitor, and a USB port. For machining all four sides of a workpiece in a single setup, an optional 5-degree indexing table is available. The indexer uses a face-gear coupler design that provides superior accuracy and extreme rigidity for off-center milling and drilling/tapping operations. With a 30" platter diameter and 10,000-lb. weight capacity, the indexer easily positions very large parts to nearly any angle for machining. A full 4th-axis platter is also available for high-speed contouring and fully interpolated motion. For high-speed machining operations, an optional 10,000-rpm 50-taper spindle (30 hp, geared-head) is available for the EC-1600. Other high-productivity options include high-speed machining software with full look-ahead, high-pressure through-spindle coolant systems, a programmable coolant nozzle, linear scales, Haas Intuitive Probing System (tool and work offset) and Ethernet connectivity.
Contact Details
Related Glossary Terms
- centers
centers
Cone-shaped pins that support a workpiece by one or two ends during machining. The centers fit into holes drilled in the workpiece ends. Centers that turn with the workpiece are called “live” centers; those that do not are called “dead” centers.
- coolant
coolant
Fluid that reduces temperature buildup at the tool/workpiece interface during machining. Normally takes the form of a liquid such as soluble or chemical mixtures (semisynthetic, synthetic) but can be pressurized air or other gas. Because of water’s ability to absorb great quantities of heat, it is widely used as a coolant and vehicle for various cutting compounds, with the water-to-compound ratio varying with the machining task. See cutting fluid; semisynthetic cutting fluid; soluble-oil cutting fluid; synthetic cutting fluid.
- gang cutting ( milling)
gang cutting ( milling)
Machining with several cutters mounted on a single arbor, generally for simultaneous cutting.
- look-ahead
look-ahead
CNC feature that evaluates many data blocks ahead of the cutting tool’s location to adjust the machining parameters to prevent gouges. This occurs when the feed rate is too high to stop the cutting tool within the required distance, resulting in an overshoot of the tool’s projected path. Ideally, look-ahead should be dynamic, varying the distance and number of program blocks based on the part profile and the desired feed rate.
- machining center
machining center
CNC machine tool capable of drilling, reaming, tapping, milling and boring. Normally comes with an automatic toolchanger. See automatic toolchanger.
- milling
milling
Machining operation in which metal or other material is removed by applying power to a rotating cutter. In vertical milling, the cutting tool is mounted vertically on the spindle. In horizontal milling, the cutting tool is mounted horizontally, either directly on the spindle or on an arbor. Horizontal milling is further broken down into conventional milling, where the cutter rotates opposite the direction of feed, or “up” into the workpiece; and climb milling, where the cutter rotates in the direction of feed, or “down” into the workpiece. Milling operations include plane or surface milling, endmilling, facemilling, angle milling, form milling and profiling.
- tapping
tapping
Machining operation in which a tap, with teeth on its periphery, cuts internal threads in a predrilled hole having a smaller diameter than the tap diameter. Threads are formed by a combined rotary and axial-relative motion between tap and workpiece. See tap.