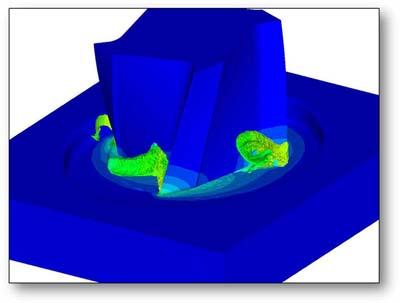
Machining modeling software developer Third Wave Systems' AdvantEdge FEM 5.8 is a material physics-based software solution for optimizing metal cutting, providing detailed information about chip formation, temperatures, stresses, and forces for machining processes. The technology provides users with data not available from trial-and-error tests, making it an invaluable tool for cutting tool design and analysis.
Capitalizing on performance improvements made in 2010 and early 2011, AdvantEdge FEM version 5.8 includes several new modeling capabilities that have been under development for years. These capabilities, coupled with ongoing performance speedups and computational enhancements, provide cutting tool manufacturers and process engineers with a more comprehensive resource for realizing optimal tool performance and getting new products to market faster.
Among AdvantEdge FEM 5.8's new and enhanced capabilities are:
Orbital drilling modeling in 3D, the newest machining process modeled by the software. AdvantEdge FEM 3D is also capable of modeling milling, turning, drilling, boring, tapping, and grooving.
Coolant pressure modeling in 2D, enabling users to predict the influence various coolant strategies will have on chip formation.
3D user-defined yield surface material modeling capabilities, enabling users to easily define their own materials, including Johnson-Cook material models.
Frictional and contact model algorithm enhancements, providing improved accuracy in 3D results.
Contact Details
Related Glossary Terms
- boring
boring
Enlarging a hole that already has been drilled or cored. Generally, it is an operation of truing the previously drilled hole with a single-point, lathe-type tool. Boring is essentially internal turning, in that usually a single-point cutting tool forms the internal shape. Some tools are available with two cutting edges to balance cutting forces.
- coolant
coolant
Fluid that reduces temperature buildup at the tool/workpiece interface during machining. Normally takes the form of a liquid such as soluble or chemical mixtures (semisynthetic, synthetic) but can be pressurized air or other gas. Because of water’s ability to absorb great quantities of heat, it is widely used as a coolant and vehicle for various cutting compounds, with the water-to-compound ratio varying with the machining task. See cutting fluid; semisynthetic cutting fluid; soluble-oil cutting fluid; synthetic cutting fluid.
- gang cutting ( milling)
gang cutting ( milling)
Machining with several cutters mounted on a single arbor, generally for simultaneous cutting.
- grooving
grooving
Machining grooves and shallow channels. Example: grooving ball-bearing raceways. Typically performed by tools that are capable of light cuts at high feed rates. Imparts high-quality finish.
- milling
milling
Machining operation in which metal or other material is removed by applying power to a rotating cutter. In vertical milling, the cutting tool is mounted vertically on the spindle. In horizontal milling, the cutting tool is mounted horizontally, either directly on the spindle or on an arbor. Horizontal milling is further broken down into conventional milling, where the cutter rotates opposite the direction of feed, or “up” into the workpiece; and climb milling, where the cutter rotates in the direction of feed, or “down” into the workpiece. Milling operations include plane or surface milling, endmilling, facemilling, angle milling, form milling and profiling.
- tapping
tapping
Machining operation in which a tap, with teeth on its periphery, cuts internal threads in a predrilled hole having a smaller diameter than the tap diameter. Threads are formed by a combined rotary and axial-relative motion between tap and workpiece. See tap.
- turning
turning
Workpiece is held in a chuck, mounted on a face plate or secured between centers and rotated while a cutting tool, normally a single-point tool, is fed into it along its periphery or across its end or face. Takes the form of straight turning (cutting along the periphery of the workpiece); taper turning (creating a taper); step turning (turning different-size diameters on the same work); chamfering (beveling an edge or shoulder); facing (cutting on an end); turning threads (usually external but can be internal); roughing (high-volume metal removal); and finishing (final light cuts). Performed on lathes, turning centers, chucking machines, automatic screw machines and similar machines.