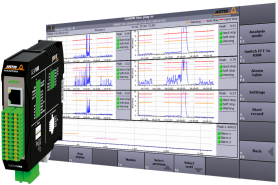
Marposs, a world leader in measurement, inspection and test technologies, has announced its new Artis GEMVM system, which monitors vibration, gravity and temperature values to detect machining anomalies, such as damage to spindle bearings or wear of the drive axles. This makes it a highly effective solution for predictive maintenance and simple process monitoring, as well as for the detection of collisions and crashes. When a sudden change occurs, the system initiates an alarm in less than 1ms, helping to reduce or avoid the downtime and costs of unplanned maintenance or total failure of machine components.
Predictive maintenance, which provides real-time information from the machine tool, is a more advanced option than preventive maintenance based on previous cases and an estimate of equipment life expectancy. Thus, predictive maintenance contributes to the overall service life of the equipment by preventing early or late replacements. Additionally, it identifies any need for changes in the machine parameters to avoid unwanted events.
The GEMVM system measures acceleration in up to three axes (depending upon sensor type) with a measuring frequency of up to 5.6kHz and a sampling rate of 25kHz. It has eight definable and selectable operating modes with five freely activatable static alarms. Any events that violate the predefined hard stop limits are logged in the event memory with relevant information for later analysis.
The system comes with the Artis VisuScope diagnostic tool, which is ideal for assuring the quality of new machines and those in operation. Process analyses based upon determined GEMVM data allow historical comparison of machine states, evaluation of damages, and the control after repairs.
The GEMVM can function in a stand-alone mode, running on Windows® (WIN 7/10) machine control panels or Siemens Linux systems (TCU). Or, the software can be installed on 7 or 10” industrial PCs from Marposs or any Windows PC (WIN 7/10). Additionally, the GEMVM can also be integrated into a Genior modular monitoring system for process monitoring purposes, delivering the vibration velocity and acceleration to a processing unit for further evaluation.