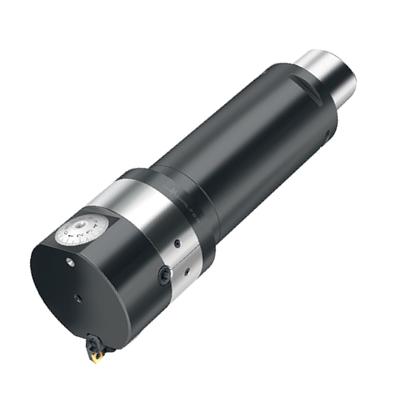
Walter has introduced a reduced weight version of its Walter PrecisionMEDIUM B4031.C with the Walter Capto modular toolholding interface. This single-edged precision boring tool is now available weighing 30-50 percent less than the previous version. While maintaining the same dimensions along with the same properties and performance levels, the new LWS (Light Weight Solution) version weighs just 3.2 kg as opposed to 7.2 kg. Walter is adding the LWS design into its product range with diameters from 90-110mm and 110 to 153mm.
For the user, this offers several advantages, beginning with easier handling for personnel in the assembly and setting area. Also, these light weight tools are particularly beneficial if a machine's tool magazine can accommodate limited weight. The design protects the machine and spindle as there is less weight during acceleration and deceleration.
Likewise, the moment of force is reduced for the same projection lengths, making it easier to change the tool. Due to its special construction, the tool is also more effective at reducing vibration, according to the company. The B4031.C's light weight Walter Capto interface, with its high clamping force and even force distribution, is completely backlash-free.
In addition, it significantly enhances the new tool's versatility. That's because many of today's machine tools include a Capto interface as standard because Capto is a universal interface, suitable for turning, drilling, counterboring and precision boring, as well as for milling, in both rotating and static modes. With this unique interface system, all machining operations can be performed on lathes, machining centers and turn/mill centers.
Contact Details
Related Glossary Terms
- boring
boring
Enlarging a hole that already has been drilled or cored. Generally, it is an operation of truing the previously drilled hole with a single-point, lathe-type tool. Boring is essentially internal turning, in that usually a single-point cutting tool forms the internal shape. Some tools are available with two cutting edges to balance cutting forces.
- centers
centers
Cone-shaped pins that support a workpiece by one or two ends during machining. The centers fit into holes drilled in the workpiece ends. Centers that turn with the workpiece are called “live” centers; those that do not are called “dead” centers.
- counterboring
counterboring
Enlarging one end of a drilled hole. The enlarged hole, which is concentric with the original hole, is flat on the bottom. Counterboring is used primarily to set bolt heads and nuts below the workpiece surface.
- gang cutting ( milling)
gang cutting ( milling)
Machining with several cutters mounted on a single arbor, generally for simultaneous cutting.
- milling
milling
Machining operation in which metal or other material is removed by applying power to a rotating cutter. In vertical milling, the cutting tool is mounted vertically on the spindle. In horizontal milling, the cutting tool is mounted horizontally, either directly on the spindle or on an arbor. Horizontal milling is further broken down into conventional milling, where the cutter rotates opposite the direction of feed, or “up” into the workpiece; and climb milling, where the cutter rotates in the direction of feed, or “down” into the workpiece. Milling operations include plane or surface milling, endmilling, facemilling, angle milling, form milling and profiling.
- turning
turning
Workpiece is held in a chuck, mounted on a face plate or secured between centers and rotated while a cutting tool, normally a single-point tool, is fed into it along its periphery or across its end or face. Takes the form of straight turning (cutting along the periphery of the workpiece); taper turning (creating a taper); step turning (turning different-size diameters on the same work); chamfering (beveling an edge or shoulder); facing (cutting on an end); turning threads (usually external but can be internal); roughing (high-volume metal removal); and finishing (final light cuts). Performed on lathes, turning centers, chucking machines, automatic screw machines and similar machines.