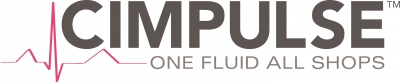
Milacron Fluid Technologies brand CIMCOOL announced a new product release to its CIMPULSE metalworking fluid line. CIMPULSE products are designed to cover a broad-range of applications with trouble-free performance allowing customers to use one product across a range of operations.
CIMPULSE 49MP is an oil-containing, multi-purpose fluid for both machining and grinding. It offers high performance without the use of traditional extreme pressure lubricants and is recommended for turning, drilling, milling, reaming, boring, tapping, and grinding of most metals. It is excellent in hard water situations and leaves a light, manageable residue and customer feedback regarding the fluids cleanliness has been very positive. More importantly, it is easy to use and minimizes the number of products CIMCOOL customers have to inventory.
Bruce Koehler, CIMCOOL senior product and technical services manager, said, “CIMPULSE 49MP evolved from listening to our customers’ requirements who want more. Our initial CIMPULSE family of products has been the fastest growing launch of products in CIMCOOL’s history.”
CIMPULSE 49MP fits perfectly between CIMPULSE 45MP and CIMPULSE 51MP by offering:
- Broad range applications even on tough jobs.
- Improved cleanliness of operation with excellent operator acceptance.
- Low foaming characteristics.
- Excellent sump life.
- Reduced concentrate consumption and carry-off.
- DCHA free chemistry.
Koehler added, “This is a great product for job shops or large manufacturers wanting to minimize the number of products they have to stock. Our own Milacron manufacturing locations use our CIMPULSE fluids, and CIMPULSE 49MP was validated on our own metalworking processes.”
CIMCOOL expects customers will be able to significantly lower inventory and reduce costs by switching to a CIMPULSE metalworking solution.
Contact Details
Related Glossary Terms
- boring
boring
Enlarging a hole that already has been drilled or cored. Generally, it is an operation of truing the previously drilled hole with a single-point, lathe-type tool. Boring is essentially internal turning, in that usually a single-point cutting tool forms the internal shape. Some tools are available with two cutting edges to balance cutting forces.
- gang cutting ( milling)
gang cutting ( milling)
Machining with several cutters mounted on a single arbor, generally for simultaneous cutting.
- grinding
grinding
Machining operation in which material is removed from the workpiece by a powered abrasive wheel, stone, belt, paste, sheet, compound, slurry, etc. Takes various forms: surface grinding (creates flat and/or squared surfaces); cylindrical grinding (for external cylindrical and tapered shapes, fillets, undercuts, etc.); centerless grinding; chamfering; thread and form grinding; tool and cutter grinding; offhand grinding; lapping and polishing (grinding with extremely fine grits to create ultrasmooth surfaces); honing; and disc grinding.
- metalworking
metalworking
Any manufacturing process in which metal is processed or machined such that the workpiece is given a new shape. Broadly defined, the term includes processes such as design and layout, heat-treating, material handling and inspection.
- milling
milling
Machining operation in which metal or other material is removed by applying power to a rotating cutter. In vertical milling, the cutting tool is mounted vertically on the spindle. In horizontal milling, the cutting tool is mounted horizontally, either directly on the spindle or on an arbor. Horizontal milling is further broken down into conventional milling, where the cutter rotates opposite the direction of feed, or “up” into the workpiece; and climb milling, where the cutter rotates in the direction of feed, or “down” into the workpiece. Milling operations include plane or surface milling, endmilling, facemilling, angle milling, form milling and profiling.
- tapping
tapping
Machining operation in which a tap, with teeth on its periphery, cuts internal threads in a predrilled hole having a smaller diameter than the tap diameter. Threads are formed by a combined rotary and axial-relative motion between tap and workpiece. See tap.
- turning
turning
Workpiece is held in a chuck, mounted on a face plate or secured between centers and rotated while a cutting tool, normally a single-point tool, is fed into it along its periphery or across its end or face. Takes the form of straight turning (cutting along the periphery of the workpiece); taper turning (creating a taper); step turning (turning different-size diameters on the same work); chamfering (beveling an edge or shoulder); facing (cutting on an end); turning threads (usually external but can be internal); roughing (high-volume metal removal); and finishing (final light cuts). Performed on lathes, turning centers, chucking machines, automatic screw machines and similar machines.