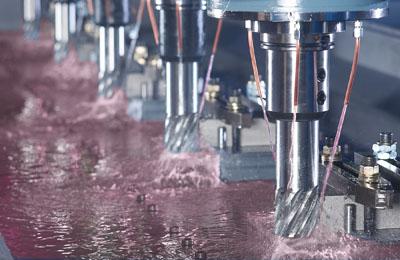
CIMCOOL Fluid Technology announced the release of a new lubricant technology for machining and grinding of hard metals. These CIMTECH synthetic fluids feature synergistic lubricant blends that provide huge increases in productivity without the use of chlorine or other high levels of extreme pressure additives. CIMCOOL delivers significant cost reductions from the higher production rates these fluids can provide, according to the company.
More production and lower cost per part coupled with environmentally responsible fluids gives significant advantages to customers concerned with being competitive. With unique hybrid blends, including patented Milacron lubricants, only CIMCOOL can provide customers with these innovative fluids. Customers with heavy duty performance requirements looking to eliminate chlorine from their operations now have options never before available.
"We have developed something that is completely new and unique to the industry," said Tina Hunter, Automotive Product Manager. "These fluids work best when really pushed to the limit. The tougher the operation, the better results we see. The performance of these fluids is significantly better. They have outperformed some popular heavy duty, sulfo-chlorinated oils by up to 300 percent. This is a huge jump in technology."
And this is enormously significant in the automotive (and other) communities. There has been (and continues) to be a constant shifting of material preferences, especially as the materials themselves change in metallurgical makeup (steel is now lighter and more flexible, thus making a comeback, again). Then there is the penetration of the non-steels (aluminum, magnesium, titanium and other exotics) into automotive components, driving manufacturing managers and operators to rethink their milling, turning, drilling and grinding processes and the fluids they use.
CIMCOOL's new Hybrid Fluid Technology products include:
CIMTECH 627 — A synthetic fluid used in heavy-duty machining and grinding of exotic alloys, this water-based fluid performs best at high speeds and feeds where conventional fluids fail. With better lubricity than sulfo-chlorinated soluble oils, this new synthetic offers up to 65 percent savings compared to conventional competitive fluids.
CIMTECH 609-E — This water-based fluid exhibits reduced chatter, decreased wheel loading, excellent finish and more machine uptime in hard metal valve grinding and can provide more productivity compared to competitive soluble oils. Customer-documented results show a 52 percent lower cost per part.
CIMTECH 610 — A unique blend of patented Milacron Synthetic Lubricants (MSL) makes this perfect for titanium and other hard metals. Significantly lower cutting forces provide tool savings up to 200 percent making this one of the best fluids for ferrous metals CIMCOOL has ever developed. This fluid performs best at high speeds and feeds where conventional fluids fail and does not contain chlorine, sulfur or phosphorus. It can also be used on aluminum alloys as well.
CIMTECH 612NF — This water-based synthetic is reportedly the best CIMCOOL has ever developed for machining high-silicon aluminum alloys, with excellent machining and tapping capabilities. Dramatically lower cutting forces improve tool life and finish even in operations with extreme speeds and feeds. This fluid can be used on some ferrous grinding and machining applications. It does not contain chlorine, sulfur or phosphorus.
Contact Details
Related Glossary Terms
- alloys
alloys
Substances having metallic properties and being composed of two or more chemical elements of which at least one is a metal.
- aluminum alloys
aluminum alloys
Aluminum containing specified quantities of alloying elements added to obtain the necessary mechanical and physical properties. Aluminum alloys are divided into two categories: wrought compositions and casting compositions. Some compositions may contain up to 10 alloying elements, but only one or two are the main alloying elements, such as copper, manganese, silicon, magnesium, zinc or tin.
- chatter
chatter
Condition of vibration involving the machine, workpiece and cutting tool. Once this condition arises, it is often self-sustaining until the problem is corrected. Chatter can be identified when lines or grooves appear at regular intervals in the workpiece. These lines or grooves are caused by the teeth of the cutter as they vibrate in and out of the workpiece and their spacing depends on the frequency of vibration.
- extreme pressure additives ( EP)
extreme pressure additives ( EP)
Cutting-fluid additives (chlorine, sulfur or phosphorus compounds) that chemically react with the workpiece material to minimize chipwelding. Good for high-speed machining. See cutting fluid.
- gang cutting ( milling)
gang cutting ( milling)
Machining with several cutters mounted on a single arbor, generally for simultaneous cutting.
- grinding
grinding
Machining operation in which material is removed from the workpiece by a powered abrasive wheel, stone, belt, paste, sheet, compound, slurry, etc. Takes various forms: surface grinding (creates flat and/or squared surfaces); cylindrical grinding (for external cylindrical and tapered shapes, fillets, undercuts, etc.); centerless grinding; chamfering; thread and form grinding; tool and cutter grinding; offhand grinding; lapping and polishing (grinding with extremely fine grits to create ultrasmooth surfaces); honing; and disc grinding.
- lubricity
lubricity
Measure of the relative efficiency with which a cutting fluid or lubricant reduces friction between surfaces.
- milling
milling
Machining operation in which metal or other material is removed by applying power to a rotating cutter. In vertical milling, the cutting tool is mounted vertically on the spindle. In horizontal milling, the cutting tool is mounted horizontally, either directly on the spindle or on an arbor. Horizontal milling is further broken down into conventional milling, where the cutter rotates opposite the direction of feed, or “up” into the workpiece; and climb milling, where the cutter rotates in the direction of feed, or “down” into the workpiece. Milling operations include plane or surface milling, endmilling, facemilling, angle milling, form milling and profiling.
- tapping
tapping
Machining operation in which a tap, with teeth on its periphery, cuts internal threads in a predrilled hole having a smaller diameter than the tap diameter. Threads are formed by a combined rotary and axial-relative motion between tap and workpiece. See tap.
- turning
turning
Workpiece is held in a chuck, mounted on a face plate or secured between centers and rotated while a cutting tool, normally a single-point tool, is fed into it along its periphery or across its end or face. Takes the form of straight turning (cutting along the periphery of the workpiece); taper turning (creating a taper); step turning (turning different-size diameters on the same work); chamfering (beveling an edge or shoulder); facing (cutting on an end); turning threads (usually external but can be internal); roughing (high-volume metal removal); and finishing (final light cuts). Performed on lathes, turning centers, chucking machines, automatic screw machines and similar machines.