Contact Details
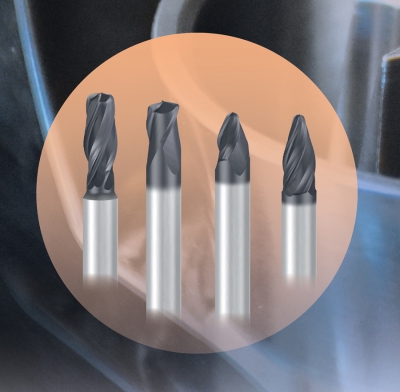
Emuge Corp. has introduced “circle-segment” cutters, a class of endmills designed to reportedly enable substantially more material removal with fewer passes in 5-Axis machining, over 80 percent cycle time reductions and up to 50 percent smoother surface finishes.
These high-performance tools, ideal for machining turbine blades, impellers, blisks and in moldmaking applications, feature unique forms with large radii in the cutting area of the mills, allowing a larger axial depth of cut during prefinishing and finishing operations.
Emuge circle-segment solid-carbide endmills are offered in four geometries: barrel-shaped, oval form, taper form and lens shape. Oval and taper form mills are ideal for curved shapes such as blades or straight-walled pockets, freely engaging more of the cutting edge. Barrel design mills provide highly effective flank milling to the sides of spiral grooves and similar applications, while lens shape mills excel in narrow channels or in lands on molds.
Specific CAM system software, such as HyperMill (Open Mind) or Mastercam Version 2017 is required to support and compute the geometries of Emuge circle-segment end mills to achieve the performance levels the tools were designed for.
“Our all-new circle-segment end mills, only available from Emuge, provide unprecedented levels of machining performance in complex 5-axis applications, allowing precision manufacturers to attain dramatic time and cost savings, while increasing part quality,” said Mr. Bob Hellinger, President of Emuge Corp.
Related Glossary Terms
- computer-aided manufacturing ( CAM)
computer-aided manufacturing ( CAM)
Use of computers to control machining and manufacturing processes.
- depth of cut
depth of cut
Distance between the bottom of the cut and the uncut surface of the workpiece, measured in a direction at right angles to the machined surface of the workpiece.
- gang cutting ( milling)
gang cutting ( milling)
Machining with several cutters mounted on a single arbor, generally for simultaneous cutting.
- milling
milling
Machining operation in which metal or other material is removed by applying power to a rotating cutter. In vertical milling, the cutting tool is mounted vertically on the spindle. In horizontal milling, the cutting tool is mounted horizontally, either directly on the spindle or on an arbor. Horizontal milling is further broken down into conventional milling, where the cutter rotates opposite the direction of feed, or “up” into the workpiece; and climb milling, where the cutter rotates in the direction of feed, or “down” into the workpiece. Milling operations include plane or surface milling, endmilling, facemilling, angle milling, form milling and profiling.