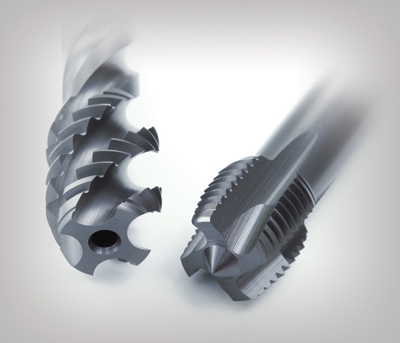
Emuge Corp. announced they are introducing a new tap program, Z-Taps, an extensive line of taps featuring design and engineering that make them ideal for stainless steels, high strength alloys, tool steels and cast steels less than or equal to 30 HRC.
Emuge Z-Taps are designed with an advanced chamfer geometry and rake/flute form. GLT-1, a newly developed multi-layered coating, produces a consistent, controllable chip formation that is released smoothly for fast and efficient chip removal. GLT-1 is uniquely structured with advanced heat resistance characteristics, along with an outer anti-friction layer. These elements synergistically combine to produce exceptional wear resistance and sliding properties that result in improved tool life, reduced torque, optimized chip evacuation and superior thread finish.
Mark Hatch, Emuge Corp. Product Director said, "The Emuge Z-Tap is engineered for the economical and efficient tapping of stainless steels and other alloy, tool and cast steels."
Emuge Z-Taps feature an increased number of flutes and a shortened thread section to reduce friction, and a lower cutting torque to reduce the occurrence of tap breakage and enable higher cutting speeds. The Z-Taps line is available in through-hole and blind-hole designs for thread lengths up to 3xD. Blind-hole taps offer two chamfer designs — a full bottoming (1.5-2 threads) and a modified bottoming (2-3 threads).
A DIN length is available for improved chip clearance in hard-to-reach tapping applications. For optimal results, Z-Taps are recommended on CNC machines with synchronous spindles utilizing emulsion coolant lubrication and synchronous tap holders such as the Emuge Softsynchro Holder. A full line of sizes from no. 4 to ¾" are available in UNC, UNF and Metric Fine and Coarse, 160 sku's in total.
Contact Details
Related Glossary Terms
- alloys
alloys
Substances having metallic properties and being composed of two or more chemical elements of which at least one is a metal.
- blind-hole
blind-hole
Hole or cavity cut in a solid shape that does not connect with other holes or exit through the workpiece.
- chip clearance
chip clearance
In milling, the groove or space provided in the cutter body that allows chips to be formed by the inserts.
- clearance
clearance
Space provided behind a tool’s land or relief to prevent rubbing and subsequent premature deterioration of the tool. See land; relief.
- computer numerical control ( CNC)
computer numerical control ( CNC)
Microprocessor-based controller dedicated to a machine tool that permits the creation or modification of parts. Programmed numerical control activates the machine’s servos and spindle drives and controls the various machining operations. See DNC, direct numerical control; NC, numerical control.
- coolant
coolant
Fluid that reduces temperature buildup at the tool/workpiece interface during machining. Normally takes the form of a liquid such as soluble or chemical mixtures (semisynthetic, synthetic) but can be pressurized air or other gas. Because of water’s ability to absorb great quantities of heat, it is widely used as a coolant and vehicle for various cutting compounds, with the water-to-compound ratio varying with the machining task. See cutting fluid; semisynthetic cutting fluid; soluble-oil cutting fluid; synthetic cutting fluid.
- emulsion
emulsion
Suspension of one liquid in another, such as oil in water.
- flutes
flutes
Grooves and spaces in the body of a tool that permit chip removal from, and cutting-fluid application to, the point of cut.
- stainless steels
stainless steels
Stainless steels possess high strength, heat resistance, excellent workability and erosion resistance. Four general classes have been developed to cover a range of mechanical and physical properties for particular applications. The four classes are: the austenitic types of the chromium-nickel-manganese 200 series and the chromium-nickel 300 series; the martensitic types of the chromium, hardenable 400 series; the chromium, nonhardenable 400-series ferritic types; and the precipitation-hardening type of chromium-nickel alloys with additional elements that are hardenable by solution treating and aging.
- tap
tap
Cylindrical tool that cuts internal threads and has flutes to remove chips and carry tapping fluid to the point of cut. Normally used on a drill press or tapping machine but also may be operated manually. See tapping.
- tapping
tapping
Machining operation in which a tap, with teeth on its periphery, cuts internal threads in a predrilled hole having a smaller diameter than the tap diameter. Threads are formed by a combined rotary and axial-relative motion between tap and workpiece. See tap.
- through-hole
through-hole
Hole or cavity cut in a solid shape that connects with other holes or extends all the way through the workpiece.
- tool steels
tool steels
Group of alloy steels which, after proper heat treatment, provide the combination of properties required for cutting tool and die applications. The American Iron and Steel Institute divides tool steels into six major categories: water hardening, shock resisting, cold work, hot work, special purpose and high speed.
- wear resistance
wear resistance
Ability of the tool to withstand stresses that cause it to wear during cutting; an attribute linked to alloy composition, base material, thermal conditions, type of tooling and operation and other variables.