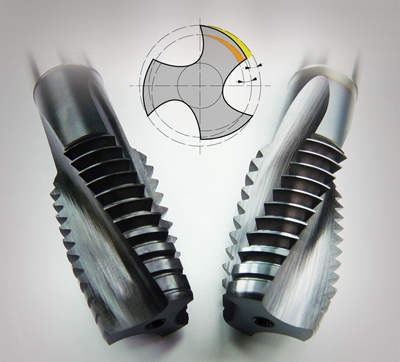
Emuge Corp. is introducing a comprehensive line of high-performance tools for threading demanding alloyed titanium materials. Ranging from taps with unique new geometry designs to solid-carbide thread mills, the new program provides solutions for the most demanding titanium challenges such as in aerospace, defense and medical machining applications. A full line of tap sizes from no. 0 to 1" are available in UNC, UNF and from 3 x 0.5 to 24 x 3.0 in Metric, 222 tools in total.
The new Emuge Titanium Program features C-Ti and D-Ti taps with new High Relief Geometry (HRG) technology, which increases space between the friction surfaces for enhanced lubrication and reduced torque load in both forward and reverse direction. HRG counteracts the high compressive forces produced by the extreme elastic memory of Titanium. An optimized flute angle and profile create tough, long chips that evacuate axially in one direction. Taps are manufactured with premium HSS-E steel for exceptional heat and wear resistance, and a modified bottoming chamfer provides reduced torque and increased tool life.
With Advanced left-hand helical flute form and chamfer geometry, C-Ti taps optimize chip evacuation in the forward direction and add strength to the cutting teeth for enhanced tool life and process security. The new D-Ti taps are available in STI thread sizes for jet engine components. Both C-Ti and D-Ti taps are available in a special NT2 coating with nitriding that provides increased edge hardness and a steam layer over the nitriding that promotes lubricity to prevent cold welding. Taps are also available with a TiCN multi-layer PVD coating for increased edge hardness and surface lubricity.
Mark Hatch, Emuge Corp. Product Director commented, "Emuge's new HRG technology is ideal for threading tough, long chipping titaniums. The optimized geometry provides extraordinary tool life, superior thread finish, and excellent guiding properties for true-to-gauge fit and significantly reduced chipped teeth or tap breakage."
The new Titanium Program also offers a variety of thread mills. THREADS-ALL Z-GF style thread mills require only eight stock standard tool sizes to produce 100+ commonly produced screw thread designations. They provide easy machining of difficult materials, one tool for through and blind holes and total control over pitch diameter limits. SHUR-THREAD GFI-IKZ thread mills with internal coolant offer an exceptional balance of performance and price with specially engineered multiple-spiral flutes to eliminate chatter, a large cutter diameter with high profile correction to ensure true-to-gauge threads and an extended milling portion which allows for 2xD length of cut.
For optimal results, Emuge recommends that tools from the Titanium Program run on a CNC machine with a synchronous spindle utilizing a tap holder with minimal compensation, such as Emuge Softsynchro, which features patented construction separation of the transmission of torque and axial force for the best imaginable tool life and thread surface quality.
Contact Details
Related Glossary Terms
- axial force
axial force
When drilling, a force that is directed axially—along the direction of machining. The magnitude of an axial force rises with the drill’s diameter and the chisel edge’s width. Axial force is also known as thrust. When turning and boring, the term “feed force” is commonly used instead of “axial force.” See cutting force.
- chatter
chatter
Condition of vibration involving the machine, workpiece and cutting tool. Once this condition arises, it is often self-sustaining until the problem is corrected. Chatter can be identified when lines or grooves appear at regular intervals in the workpiece. These lines or grooves are caused by the teeth of the cutter as they vibrate in and out of the workpiece and their spacing depends on the frequency of vibration.
- computer numerical control ( CNC)
computer numerical control ( CNC)
Microprocessor-based controller dedicated to a machine tool that permits the creation or modification of parts. Programmed numerical control activates the machine’s servos and spindle drives and controls the various machining operations. See DNC, direct numerical control; NC, numerical control.
- coolant
coolant
Fluid that reduces temperature buildup at the tool/workpiece interface during machining. Normally takes the form of a liquid such as soluble or chemical mixtures (semisynthetic, synthetic) but can be pressurized air or other gas. Because of water’s ability to absorb great quantities of heat, it is widely used as a coolant and vehicle for various cutting compounds, with the water-to-compound ratio varying with the machining task. See cutting fluid; semisynthetic cutting fluid; soluble-oil cutting fluid; synthetic cutting fluid.
- flutes
flutes
Grooves and spaces in the body of a tool that permit chip removal from, and cutting-fluid application to, the point of cut.
- gang cutting ( milling)
gang cutting ( milling)
Machining with several cutters mounted on a single arbor, generally for simultaneous cutting.
- hardness
hardness
Hardness is a measure of the resistance of a material to surface indentation or abrasion. There is no absolute scale for hardness. In order to express hardness quantitatively, each type of test has its own scale, which defines hardness. Indentation hardness obtained through static methods is measured by Brinell, Rockwell, Vickers and Knoop tests. Hardness without indentation is measured by a dynamic method, known as the Scleroscope test.
- lubricity
lubricity
Measure of the relative efficiency with which a cutting fluid or lubricant reduces friction between surfaces.
- milling
milling
Machining operation in which metal or other material is removed by applying power to a rotating cutter. In vertical milling, the cutting tool is mounted vertically on the spindle. In horizontal milling, the cutting tool is mounted horizontally, either directly on the spindle or on an arbor. Horizontal milling is further broken down into conventional milling, where the cutter rotates opposite the direction of feed, or “up” into the workpiece; and climb milling, where the cutter rotates in the direction of feed, or “down” into the workpiece. Milling operations include plane or surface milling, endmilling, facemilling, angle milling, form milling and profiling.
- nitriding
nitriding
Introducing nitrogen into the surface layer of a solid ferrous alloy. This is done to increase hardness, wear resistance and fatigue strength.
- physical vapor deposition ( PVD)
physical vapor deposition ( PVD)
Tool-coating process performed at low temperature (500° C), compared to chemical vapor deposition (1,000° C). Employs electric field to generate necessary heat for depositing coating on a tool’s surface. See CVD, chemical vapor deposition.
- pitch
pitch
1. On a saw blade, the number of teeth per inch. 2. In threading, the number of threads per inch.
- relief
relief
Space provided behind the cutting edges to prevent rubbing. Sometimes called primary relief. Secondary relief provides additional space behind primary relief. Relief on end teeth is axial relief; relief on side teeth is peripheral relief.
- tap
tap
Cylindrical tool that cuts internal threads and has flutes to remove chips and carry tapping fluid to the point of cut. Normally used on a drill press or tapping machine but also may be operated manually. See tapping.
- threading
threading
Process of both external (e.g., thread milling) and internal (e.g., tapping, thread milling) cutting, turning and rolling of threads into particular material. Standardized specifications are available to determine the desired results of the threading process. Numerous thread-series designations are written for specific applications. Threading often is performed on a lathe. Specifications such as thread height are critical in determining the strength of the threads. The material used is taken into consideration in determining the expected results of any particular application for that threaded piece. In external threading, a calculated depth is required as well as a particular angle to the cut. To perform internal threading, the exact diameter to bore the hole is critical before threading. The threads are distinguished from one another by the amount of tolerance and/or allowance that is specified. See turning.
- titanium carbonitride ( TiCN)
titanium carbonitride ( TiCN)
Often used as a tool coating. See coated tools.
- wear resistance
wear resistance
Ability of the tool to withstand stresses that cause it to wear during cutting; an attribute linked to alloy composition, base material, thermal conditions, type of tooling and operation and other variables.