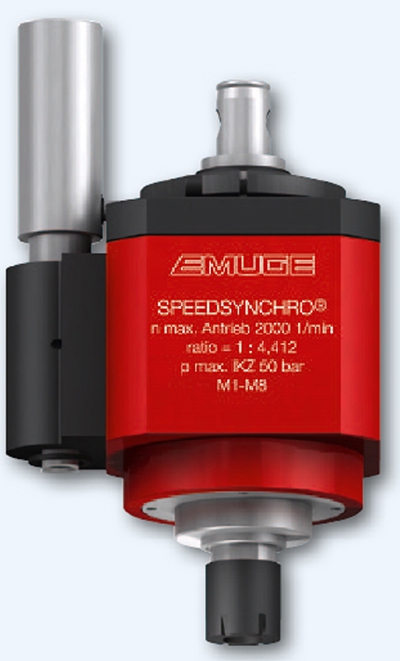
Emuge Corp. has introduced the SPEEDSYNCHRO tool holder, which features an integrated transmission of 1:4.412 for optimizing thread production on CNC machines with synchronous spindles. The integrated transmission is combined with Softsynchro minimum-length compensation to efficiently work with high cutting speeds and a relatively low synchronous machine tool speed, compensating for synchronization errors during the threading process. The results are reportedly significant time and money savings, particularly in high-production tapping operations.
The new tool holder offers easy programming and up to 40 percent time savings due to significantly shortened thread production cycles resulting from the combined fast acceleration and cutting speeds facilitated by the integrated transmission. The time savings substantially increases the number of tapped holes achieved in a given operation and is especially effective in high production tapping. Tool life and thread surface quality are both optimized.
Exact thread depths can be achieved with SPEEDSYNCHRO as it does not reverse the direction of rotation. Emuge SPEEDSYNCHRO Tool Holder supports a maximum spindle speed of 2,000 RPM and a maximum tapping speed of 8,824 RPM. Cutting range is from M1 — M8 and an ER16 tool holder size is offered. Internal coolant capability is provided.
Contact Details
Related Glossary Terms
- computer numerical control ( CNC)
computer numerical control ( CNC)
Microprocessor-based controller dedicated to a machine tool that permits the creation or modification of parts. Programmed numerical control activates the machine’s servos and spindle drives and controls the various machining operations. See DNC, direct numerical control; NC, numerical control.
- coolant
coolant
Fluid that reduces temperature buildup at the tool/workpiece interface during machining. Normally takes the form of a liquid such as soluble or chemical mixtures (semisynthetic, synthetic) but can be pressurized air or other gas. Because of water’s ability to absorb great quantities of heat, it is widely used as a coolant and vehicle for various cutting compounds, with the water-to-compound ratio varying with the machining task. See cutting fluid; semisynthetic cutting fluid; soluble-oil cutting fluid; synthetic cutting fluid.
- tapping
tapping
Machining operation in which a tap, with teeth on its periphery, cuts internal threads in a predrilled hole having a smaller diameter than the tap diameter. Threads are formed by a combined rotary and axial-relative motion between tap and workpiece. See tap.
- threading
threading
Process of both external (e.g., thread milling) and internal (e.g., tapping, thread milling) cutting, turning and rolling of threads into particular material. Standardized specifications are available to determine the desired results of the threading process. Numerous thread-series designations are written for specific applications. Threading often is performed on a lathe. Specifications such as thread height are critical in determining the strength of the threads. The material used is taken into consideration in determining the expected results of any particular application for that threaded piece. In external threading, a calculated depth is required as well as a particular angle to the cut. To perform internal threading, the exact diameter to bore the hole is critical before threading. The threads are distinguished from one another by the amount of tolerance and/or allowance that is specified. See turning.