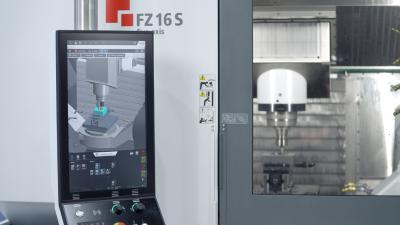
Intelligent software algorithms are essential for real-time collision avoidance, but they are only half the story. The other half is a well-designed user interface that enables operators to drive the software effectively. In their latest cooperation ModuleWorks, technology providers for digital manufacturing solutions, and the CHIRON Group, CNC machine tool manufacturers, put operator experience at the center of a new GUI for the ModuleWorks Collision Avoidance System (CAS).
The ModuleWorks CAS uses real-time machining data and look-ahead technology to detect immanent collisions and stop the machining process before an actual collision occurs. The CHIRON Group uses CAS as part of their ProtectLine digital system to protect their high-end machining centers from potentially expensive damage and downtime.
In addition to sophisticated algorithms, effective collision avoidance requires careful setup by the operator to ensure the system accurately represents the entire machining process, including the fixtures, workpiece and tools. The user interface therefore plays a pivotal role in the acceptance and effectiveness of the system:
“We asked ourselves: ‘What do operators need from a GUI in order to use the CAS effectively?’” says Jasper Sanders, Product Manager at ModuleWorks. “The obvious answer was to ask the operators, so we created a project team with the CHIRON Group and their machine operators. This proved a great approach. In less than 12 months we were able to launch a new GUI that raises usability and operator acceptance.”
“Collision avoidance is indispensable for safe and cost-effective manufacturing. Through the cooperation we have a system that truly supports machine operators and encourages them to use the full benefits of the collision avoidance technology on our machining centers”, says Pascal Schröder, Development Coordination Digitalization at the CHIRON Group.
Contact Details
Contact Details
Related Glossary Terms
- centers
centers
Cone-shaped pins that support a workpiece by one or two ends during machining. The centers fit into holes drilled in the workpiece ends. Centers that turn with the workpiece are called “live” centers; those that do not are called “dead” centers.
- computer numerical control ( CNC)
computer numerical control ( CNC)
Microprocessor-based controller dedicated to a machine tool that permits the creation or modification of parts. Programmed numerical control activates the machine’s servos and spindle drives and controls the various machining operations. See DNC, direct numerical control; NC, numerical control.
- look-ahead
look-ahead
CNC feature that evaluates many data blocks ahead of the cutting tool’s location to adjust the machining parameters to prevent gouges. This occurs when the feed rate is too high to stop the cutting tool within the required distance, resulting in an overshoot of the tool’s projected path. Ideally, look-ahead should be dynamic, varying the distance and number of program blocks based on the part profile and the desired feed rate.