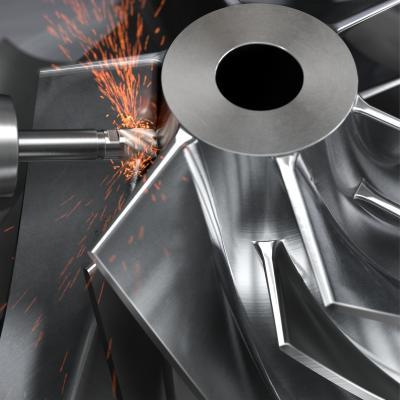
Cutting tool and tooling systems specialist Sandvik Coromant is extending its series of ceramic exchangeable milling heads with the introduction of a new ceramic grade for optimized performance in nickel-based alloys. The latest, brazed-ceramic CoroMill® 316 offers a more productive method for roughing in ISO S materials than standard carbide milling cutters.
With aerospace components manufactured from nickel-based alloys becoming increasingly prevalent, the demand for optimized cutting tools is growing. With this in mind, Sandvik Coromant has developed two innovative solutions ideal for shoulder and face milling of nickel alloy aero-engine parts.
“The ceramic substrate of the latest CoroMill 316 allows for a different cutting process than traditional solid carbide tools,” explains Tiziana Pro, Global Offer Manager, Solid End Mills, at Sandvik Coromant. “Our unique S1KU grade is purpose-designed for the superior machining of nickel alloys and is supported by a negative geometry that offers a tough cutting edge.
“In fact, the six-flute geometry delivers highly productive side milling operations, while the four-flute geometry boosts face milling. The CoroMill 316 is a perfect tool for difficult-to-reach applications or if you are looking for extra flexibility, thanks to the exchangeable head system.”
Ceramic tools retain their hardness at the high temperatures associated with milling heat-resistant super alloys (HRSAs). As a result, 20 to 30 times the speed can be achieved compared to solid carbide tools, delivering considerable potential for increased productivity. With the new, bigger head diameter available from D16-25 mm, it will be possible to reach these high cutting speeds with conventional machining centers (n = 10000-18000 rpm).
Beyond shoulder and face milling, the new end mills can also be used for pocket milling, helical interpolation, ramping and slot milling. The CoroMill 316 is part of the Sandvik Coromant Optimized Solutions offering in the company’s solid round tools range.
Contact Details
Related Glossary Terms
- alloys
alloys
Substances having metallic properties and being composed of two or more chemical elements of which at least one is a metal.
- centers
centers
Cone-shaped pins that support a workpiece by one or two ends during machining. The centers fit into holes drilled in the workpiece ends. Centers that turn with the workpiece are called “live” centers; those that do not are called “dead” centers.
- gang cutting ( milling)
gang cutting ( milling)
Machining with several cutters mounted on a single arbor, generally for simultaneous cutting.
- hardness
hardness
Hardness is a measure of the resistance of a material to surface indentation or abrasion. There is no absolute scale for hardness. In order to express hardness quantitatively, each type of test has its own scale, which defines hardness. Indentation hardness obtained through static methods is measured by Brinell, Rockwell, Vickers and Knoop tests. Hardness without indentation is measured by a dynamic method, known as the Scleroscope test.
- interpolation
interpolation
Process of generating a sufficient number of positioning commands for the servomotors driving the machine tool so the path of the tool closely approximates the ideal path. See CNC, computer numerical control; NC, numerical control.
- milling
milling
Machining operation in which metal or other material is removed by applying power to a rotating cutter. In vertical milling, the cutting tool is mounted vertically on the spindle. In horizontal milling, the cutting tool is mounted horizontally, either directly on the spindle or on an arbor. Horizontal milling is further broken down into conventional milling, where the cutter rotates opposite the direction of feed, or “up” into the workpiece; and climb milling, where the cutter rotates in the direction of feed, or “down” into the workpiece. Milling operations include plane or surface milling, endmilling, facemilling, angle milling, form milling and profiling.