Contact Details
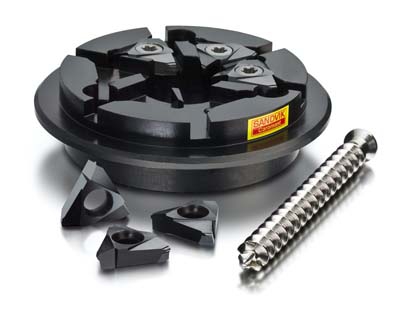
Sandvik Coromant has announced the introduction of its CoroMill 325 thread whirling inserts and holders. These tools address the growing demand for techniques that produce threads fast and at high tolerances, arising from the special thread forms used for medical bone screws, implants and other micro components. Thread whirling is a fast and accurate way to thread long, slender components in difficult-to-machine materials.
By combining the speed of thread whirling with the rigidity of a sliding head machine, complete threads are produced accurately in a single pass, without the need for special supports. CoroMill 325 thread whirling inserts and holders can produce a wide range of high precision screws and implants from rough stock at high speeds and fit a large number of sliding head machine types.
For many manufacturers, this can eliminate the need for a dedicated thread whirling machine. Thread whirling provides a number of advantages over traditional single-point threading, including increased productivity, faster set up times, no extra costs for finishing treatment, superior chip control and increased tool life over conventional tools.
Related Glossary Terms
- threading
threading
Process of both external (e.g., thread milling) and internal (e.g., tapping, thread milling) cutting, turning and rolling of threads into particular material. Standardized specifications are available to determine the desired results of the threading process. Numerous thread-series designations are written for specific applications. Threading often is performed on a lathe. Specifications such as thread height are critical in determining the strength of the threads. The material used is taken into consideration in determining the expected results of any particular application for that threaded piece. In external threading, a calculated depth is required as well as a particular angle to the cut. To perform internal threading, the exact diameter to bore the hole is critical before threading. The threads are distinguished from one another by the amount of tolerance and/or allowance that is specified. See turning.