Contact Details
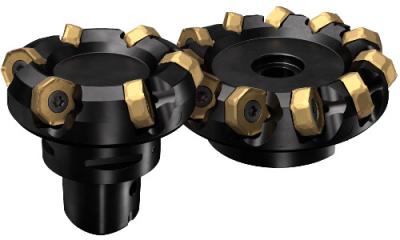
Sandvik Coromant has unveiled a new, high-feed version of the CoroMill 745 facemilling cutter, featuring a 25° entering angle for additional productivity gains when milling steel and cast iron workpieces. The new, high-feed version facilitates even higher metal-removal rates in applications with depths of cut up to 2.8 mm (0.110 inch). The new cutter is set to benefit sectors such as die and mold, pump and valve, oil and gas, automotive, power generation, and general engineering.
Despite the elevated MRR and productivity, there is no compromise to surface finish when using the new, high-feed CoroMill 745. A light cutting action from the innovative insert positioning provides excellent chip formation, a smooth, soft sound, and low power consumption, the company reports.
“An important benefit of the new cutter is low cost per edge from its double-sided, 14-edge insert design,” says Matts Westin, product manager, Sandvik Coromant. “In fact, purchasing departments will be pleased to learn that tool inventory costs are reduced because the CoroMill 745 with a 25° entering angle uses the same inserts as its counterpart cutter with a 42° entering angle.”
The high-feed CoroMill 745 is aimed at roughing to semifinishing facemilling operations on machining centers and multitask machines. With its multiple-edge concept, the tool is particularly suitable for large batch production, flexible transfer lines, and when maximum tool utilization is important. Advantages will be provided when milling components made from ISO P or ISO K materials, such as valves, engine blocks, hubs, main frames, pump components, and molds, in fact, any type of general engineering component.
The presence of a short (0.6 mm, 0.024 inch) parallel land ensures a fine surface finish. The large screw ensures easy handling, while the insert position and the heptagonal insert shape make clamping exceptionally secure for reliable facemilling operations. Internal coolant is available for all cutters that range from 63 to 160 mm (2.5 to 6.0 inch).
Providing an example of the potential gains on the offer, a customer trial application showed impressive benefits when face milling a machine bed component made from cast CMC ST52 (165 HB) on an ISO 50 gantry mill. A 125 mm (5 inch) CoroMill 745 with a 25° entering angle reduced cycle time per component by 40 percent in comparison with a competitor tool.
The high-feed CoroMill 745 with a 25° entering angle complements CoroMill 745 with a 42° entering angle.
Related Glossary Terms
- centers
centers
Cone-shaped pins that support a workpiece by one or two ends during machining. The centers fit into holes drilled in the workpiece ends. Centers that turn with the workpiece are called “live” centers; those that do not are called “dead” centers.
- coolant
coolant
Fluid that reduces temperature buildup at the tool/workpiece interface during machining. Normally takes the form of a liquid such as soluble or chemical mixtures (semisynthetic, synthetic) but can be pressurized air or other gas. Because of water’s ability to absorb great quantities of heat, it is widely used as a coolant and vehicle for various cutting compounds, with the water-to-compound ratio varying with the machining task. See cutting fluid; semisynthetic cutting fluid; soluble-oil cutting fluid; synthetic cutting fluid.
- facemilling
facemilling
Form of milling that produces a flat surface generally at right angles to the rotating axis of a cutter having teeth or inserts both on its periphery and on its end face.
- gang cutting ( milling)
gang cutting ( milling)
Machining with several cutters mounted on a single arbor, generally for simultaneous cutting.
- land
land
Part of the tool body that remains after the flutes are cut.
- milling
milling
Machining operation in which metal or other material is removed by applying power to a rotating cutter. In vertical milling, the cutting tool is mounted vertically on the spindle. In horizontal milling, the cutting tool is mounted horizontally, either directly on the spindle or on an arbor. Horizontal milling is further broken down into conventional milling, where the cutter rotates opposite the direction of feed, or “up” into the workpiece; and climb milling, where the cutter rotates in the direction of feed, or “down” into the workpiece. Milling operations include plane or surface milling, endmilling, facemilling, angle milling, form milling and profiling.
- milling machine ( mill)
milling machine ( mill)
Runs endmills and arbor-mounted milling cutters. Features include a head with a spindle that drives the cutters; a column, knee and table that provide motion in the three Cartesian axes; and a base that supports the components and houses the cutting-fluid pump and reservoir. The work is mounted on the table and fed into the rotating cutter or endmill to accomplish the milling steps; vertical milling machines also feed endmills into the work by means of a spindle-mounted quill. Models range from small manual machines to big bed-type and duplex mills. All take one of three basic forms: vertical, horizontal or convertible horizontal/vertical. Vertical machines may be knee-type (the table is mounted on a knee that can be elevated) or bed-type (the table is securely supported and only moves horizontally). In general, horizontal machines are bigger and more powerful, while vertical machines are lighter but more versatile and easier to set up and operate.
- parallel
parallel
Strip or block of precision-ground stock used to elevate a workpiece, while keeping it parallel to the worktable, to prevent cutter/table contact.