Contact Details
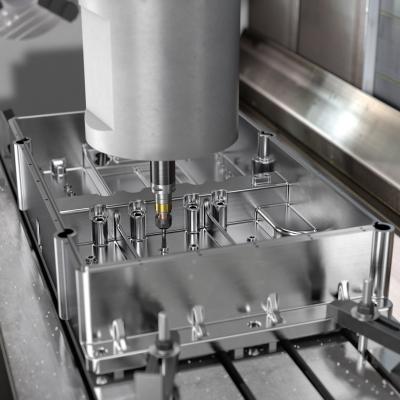
Global metal cutting specialist Sandvik Coromant recently introduced a new generation of CoroTap® 100 and CoroTap® 400 for short-chipping and chip-free tapping of aluminum. The taps offer high process security and predictable tool life.
Threading is often the last operation in a component, and the last thing manufacturers want is for the tap to break. That is why process security and predictable tool life are of the utmost importance when it comes to tapping. The next-generation CoroTap 100 and CoroTap 400, with optimized performance in aluminum, can meet very strict process security demands and offer a high level of reliability and consistent tool life.
The CoroTap 100 straight flute tap features refined edge rounding that helps to remove burrs and improve surface finish. The combination of core thickness, rake/relief angles and land width ensure optimal flute geometry with excellent chip evacuation. The back chamfer helps to improve the threading capacity when threading deep holes.
The CoroTap 400 forming tap has an optimized lobe shape developed for aluminum machining and a low friction-coefficient surface treatment for a smooth and polished thread surface finish. With a reduced thread length, the tap is less in contact with the material, reducing power consumption and torque. Finally, staggered coolant holes offer excellent coolant flow into the thread-forming zone and a safe forming process.
In a production process, tapping can be a bottleneck, and increased productivity is often a demand. For example, a typical aluminum cylinder block can have up to 12 different threads in its structure, and tapping is the most time-consuming process. With the new straight flute tap and forming tap, manufacturers can increase productivity and reduce cost per part. “Both geometries are combined with the latest surface treatments, substrates and coatings, which offer the possibility to use higher cutting data with significantly improved tool life, leading to a reduction in your cost per part,” says Robert Smith, Offer Manager for Hole Making and Composites at Sandvik Coromant.
Both taps can be used for blind and through holes in many different components, such as cylinder blocks, cylinder heads, electric motor housings, transmission housings and battery racks. Robert continues: “These products are beneficial for anyone who machines aluminum, including automotive, e-mobility and general engineering.”
Related Glossary Terms
- composites
composites
Materials composed of different elements, with one element normally embedded in another, held together by a compatible binder.
- coolant
coolant
Fluid that reduces temperature buildup at the tool/workpiece interface during machining. Normally takes the form of a liquid such as soluble or chemical mixtures (semisynthetic, synthetic) but can be pressurized air or other gas. Because of water’s ability to absorb great quantities of heat, it is widely used as a coolant and vehicle for various cutting compounds, with the water-to-compound ratio varying with the machining task. See cutting fluid; semisynthetic cutting fluid; soluble-oil cutting fluid; synthetic cutting fluid.
- land
land
Part of the tool body that remains after the flutes are cut.
- tap
tap
Cylindrical tool that cuts internal threads and has flutes to remove chips and carry tapping fluid to the point of cut. Normally used on a drill press or tapping machine but also may be operated manually. See tapping.
- tapping
tapping
Machining operation in which a tap, with teeth on its periphery, cuts internal threads in a predrilled hole having a smaller diameter than the tap diameter. Threads are formed by a combined rotary and axial-relative motion between tap and workpiece. See tap.
- threading
threading
Process of both external (e.g., thread milling) and internal (e.g., tapping, thread milling) cutting, turning and rolling of threads into particular material. Standardized specifications are available to determine the desired results of the threading process. Numerous thread-series designations are written for specific applications. Threading often is performed on a lathe. Specifications such as thread height are critical in determining the strength of the threads. The material used is taken into consideration in determining the expected results of any particular application for that threaded piece. In external threading, a calculated depth is required as well as a particular angle to the cut. To perform internal threading, the exact diameter to bore the hole is critical before threading. The threads are distinguished from one another by the amount of tolerance and/or allowance that is specified. See turning.