Contact Details
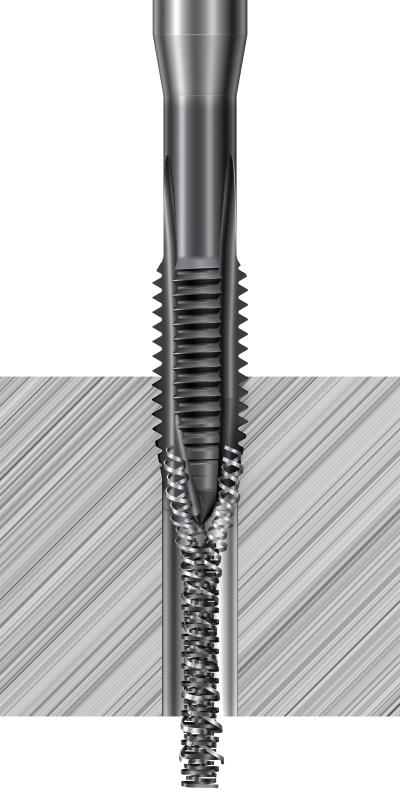
Global leader in metal cutting, Sandvik Coromant, is upgrading its range of tools for steel tapping operations with two updates to its solid round tools range. The next generation CoroTap® T200 spiral point tap and T300 spiral flute tap for ISO P deliver improved process security, longer tool life and a reduced cost per component.
Part of Sandvik Coromant’s solid round tools offering, the CoroTap range delivers material-specific solutions for threading a variety of metals. In particular, the CoroTap T200 and T300 are optimized for ISO P1 and P2 steel workpiece materials, making them suitable for machining components in the automotive and general engineering industries. This includes crank shafts, steering knuckles, and general engineering components such as housings and flanges. Both tools are suitable for mass production.
The CoroTap T200 has a spiral point, while the T300 is a spiral flute tap. While the spiral point of the T200 is suited for machining through holes, where chips are pushed forwards, the T300 is catered to blind holes, where there is no exit hole and chips must be pulled backwards. As part of the upgrade, both tools have a new surface treatment, as well as improved edge rounding for better finishing inside the machined hole. An improved flute form also offers better overall performance.
As a result of these upgrades, manufacturers will benefit from improved process security with increased resistance to edge chipping, leading to fewer tool breakages and an improved quality of the machined thread. In addition, cutting speeds are higher than previous versions of the tool and there is an overall reduction in the cost per part.
Another major difference compared to previous versions of the CoroTap range is the improved CoroTap T200 and T300 can benefit from Sandvik Coromant’s Tailor Made web assortment. Serving the industry with tailored manufacturing tools, the Tailor Made service gives customers the freedom to specify their own dimensions, without paying for a specialist tool. The taps can be adjusted to meet the demands of multiple industries and are adaptable to specific requirements.
“Performance case data demonstrates significant improvement for the tools,” explains Lisa Belfrage, Global Product Manager at Sandvik Coromant. “In fact, a comparison of the new and existing T200 tap demonstrates a 121% increase in tool life, with the potential to machine over double the number of threaded holes using a single tool. Productivity is also increased with the upgraded T200 — with cutting speeds increasing from 18 metres per minute (m/min) to 24 m/min with machining P2 steel.
“The new generation of the T300 has seen a significant increase in tool life compared to the previous version,” added Belfrage. “What’s more, when compared to a competing tool on the market, Sandvik Coromant’s upgraded CoroTap T300 demonstrates a 57% increase in tool life and higher cutting speeds.
“With demonstrated process improvements, and the ability to offer tool customisation with the Tailor Made service, the new generations of the CoroTap tools will make thread cutting faster and more efficient for our customers”.
Related Glossary Terms
- tap
tap
Cylindrical tool that cuts internal threads and has flutes to remove chips and carry tapping fluid to the point of cut. Normally used on a drill press or tapping machine but also may be operated manually. See tapping.
- tapping
tapping
Machining operation in which a tap, with teeth on its periphery, cuts internal threads in a predrilled hole having a smaller diameter than the tap diameter. Threads are formed by a combined rotary and axial-relative motion between tap and workpiece. See tap.
- threading
threading
Process of both external (e.g., thread milling) and internal (e.g., tapping, thread milling) cutting, turning and rolling of threads into particular material. Standardized specifications are available to determine the desired results of the threading process. Numerous thread-series designations are written for specific applications. Threading often is performed on a lathe. Specifications such as thread height are critical in determining the strength of the threads. The material used is taken into consideration in determining the expected results of any particular application for that threaded piece. In external threading, a calculated depth is required as well as a particular angle to the cut. To perform internal threading, the exact diameter to bore the hole is critical before threading. The threads are distinguished from one another by the amount of tolerance and/or allowance that is specified. See turning.
- web
web
On a rotating tool, the portion of the tool body that joins the lands. Web is thicker at the shank end, relative to the point end, providing maximum torsional strength.