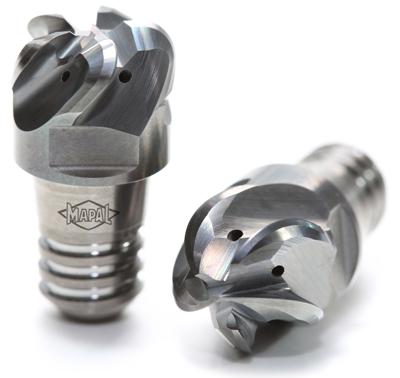
For the production of homokinetic joints of hardened steel, numerous automotive manufacturers and suppliers rely on ballnose milling cutters from the MAPAL CPMill program. For years, these have been successfully used for premachining (soft milling) and finishing (hard milling with PCBN tools). They are subject to continuous improvement. A new, comprehensive development of the milling cutter for premachining now allows users to enjoy a significant increase in efficiency.
The new, highly spiraled geometry ensures optimal chip removal, according to the company. Instead of four cutting edges, the new solid-carbide ballnose milling cutter has five. Furthermore, in addition to the base substrate, the coating has been improved. For easy changing of the milling heads, they are equipped with the CFS interface. Through the precise tuning of the taper and face, a high concentricity of ≤5μm, excellent rigidity and consistently high quality are achieved.
Examples in practice show that with the new CPMill ballnose milling cutter, machining time per component can be significantly reduced. While 75,000 parts were previously machined in one week, for example, there is around 12 percent more produced (namely, 85,000 components) with the five-edged cutter using the same machine capacity and without any additional investment in equipment, because the tool can cut at higher machining parameters. In addition, the milling cutter has a 25 percent higher service life than the previous model.
Contact Details
Related Glossary Terms
- gang cutting ( milling)
gang cutting ( milling)
Machining with several cutters mounted on a single arbor, generally for simultaneous cutting.
- milling
milling
Machining operation in which metal or other material is removed by applying power to a rotating cutter. In vertical milling, the cutting tool is mounted vertically on the spindle. In horizontal milling, the cutting tool is mounted horizontally, either directly on the spindle or on an arbor. Horizontal milling is further broken down into conventional milling, where the cutter rotates opposite the direction of feed, or “up” into the workpiece; and climb milling, where the cutter rotates in the direction of feed, or “down” into the workpiece. Milling operations include plane or surface milling, endmilling, facemilling, angle milling, form milling and profiling.
- milling cutter
milling cutter
Loosely, any milling tool. Horizontal cutters take the form of plain milling cutters, plain spiral-tooth cutters, helical cutters, side-milling cutters, staggered-tooth side-milling cutters, facemilling cutters, angular cutters, double-angle cutters, convex and concave form-milling cutters, straddle-sprocket cutters, spur-gear cutters, corner-rounding cutters and slitting saws. Vertical cutters use shank-mounted cutting tools, including endmills, T-slot cutters, Woodruff keyseat cutters and dovetail cutters; these may also be used on horizontal mills. See milling.
- polycrystalline cubic boron nitride ( PCBN)
polycrystalline cubic boron nitride ( PCBN)
Cutting tool material consisting of polycrystalline cubic boron nitride with a metallic or ceramic binder. PCBN is available either as a tip brazed to a carbide insert carrier or as a solid insert. Primarily used for cutting hardened ferrous alloys.