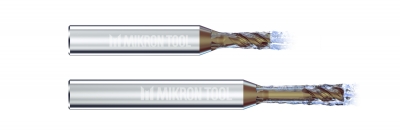
The Swiss tool manufacturer Mikron Tool has expanded its milling cutter program and launches a version of the already well-known plunge-mill CrazyMill Cool P&S, which is now suitable for even deeper machining operations.
Like its already successful "short" predecessor, it is characterized by the ability to plunge (drill) vertically into the material, mill slots or pockets into solid material in smallest spaces and concluding the milling with a finishing operation. While the milling depth in the short version (2.5 x d) was based on the machining of keyways (as found, for example, on the drive shafts of engines), the aim is now to be able to mill the deepest possible slots and pockets with a single tool and to reach more distant machining areas within a workpiece.
The new version of the solid carbide plunge mill is based on the same technology as the short version, transferred directly to the new one. Now it is possible to plunge perpendicularly into the material and reach the maximum milling depth of 5 x d in a few steps. Despite its length, the milling cutter is extremely stable and at the same time impresses with its cutting speeds, chip removal rates as well as a long tool life and surface quality, all this from a milling diameter of one millimeter (.039”).
The cutting-edge geometry enables process stable and vibration-free "drilling" (vertical plunging) even at a depth of 5 x d. This not only prevents the cutting edges from breaking out, one of the central difficulties when "drilling" with a milling cutter, but also ensures excellent surface quality and longer tool life.
Even more than with the short version, good chip removal plays an important role at this depth. There is a higher risk that chips remain in the milling zone, are broken up several times and thus damage both the milling cutter and the milled surface. The special cutting-edge geometry with extended chip area provides a remedy, on the one hand, ensuring perfect lateral chip removal during plunging and the stability of the milling cutter even during deep milling. On the other hand, the integrated coolant ducts in the shank with the massive coolant flow, ensure an efficient chip evacuation even from tight or angled spaces of deep pockets or slots.
Mr. Gotti, Head of the Technology & Customer Project Center at Mikron Tool confirms: "We work with this tool at high speeds and feeds and an axial infeed (ap) of 0.5 x d, achieving an extremely high chip removal rate. For the user, this means up to 5 times shorter machining processes and a significantly longer tool life compared to other milling cutters on the market".
CrazyMill Cool P&S is available in diameters from 1 to 8 mm and for a maximum milling depth of up to 5 x d.
Contact Details
Related Glossary Terms
- coolant
coolant
Fluid that reduces temperature buildup at the tool/workpiece interface during machining. Normally takes the form of a liquid such as soluble or chemical mixtures (semisynthetic, synthetic) but can be pressurized air or other gas. Because of water’s ability to absorb great quantities of heat, it is widely used as a coolant and vehicle for various cutting compounds, with the water-to-compound ratio varying with the machining task. See cutting fluid; semisynthetic cutting fluid; soluble-oil cutting fluid; synthetic cutting fluid.
- gang cutting ( milling)
gang cutting ( milling)
Machining with several cutters mounted on a single arbor, generally for simultaneous cutting.
- milling
milling
Machining operation in which metal or other material is removed by applying power to a rotating cutter. In vertical milling, the cutting tool is mounted vertically on the spindle. In horizontal milling, the cutting tool is mounted horizontally, either directly on the spindle or on an arbor. Horizontal milling is further broken down into conventional milling, where the cutter rotates opposite the direction of feed, or “up” into the workpiece; and climb milling, where the cutter rotates in the direction of feed, or “down” into the workpiece. Milling operations include plane or surface milling, endmilling, facemilling, angle milling, form milling and profiling.
- milling cutter
milling cutter
Loosely, any milling tool. Horizontal cutters take the form of plain milling cutters, plain spiral-tooth cutters, helical cutters, side-milling cutters, staggered-tooth side-milling cutters, facemilling cutters, angular cutters, double-angle cutters, convex and concave form-milling cutters, straddle-sprocket cutters, spur-gear cutters, corner-rounding cutters and slitting saws. Vertical cutters use shank-mounted cutting tools, including endmills, T-slot cutters, Woodruff keyseat cutters and dovetail cutters; these may also be used on horizontal mills. See milling.
- milling machine ( mill)
milling machine ( mill)
Runs endmills and arbor-mounted milling cutters. Features include a head with a spindle that drives the cutters; a column, knee and table that provide motion in the three Cartesian axes; and a base that supports the components and houses the cutting-fluid pump and reservoir. The work is mounted on the table and fed into the rotating cutter or endmill to accomplish the milling steps; vertical milling machines also feed endmills into the work by means of a spindle-mounted quill. Models range from small manual machines to big bed-type and duplex mills. All take one of three basic forms: vertical, horizontal or convertible horizontal/vertical. Vertical machines may be knee-type (the table is mounted on a knee that can be elevated) or bed-type (the table is securely supported and only moves horizontally). In general, horizontal machines are bigger and more powerful, while vertical machines are lighter but more versatile and easier to set up and operate.
- shank
shank
Main body of a tool; the portion of a drill or similar end-held tool that fits into a collet, chuck or similar mounting device.