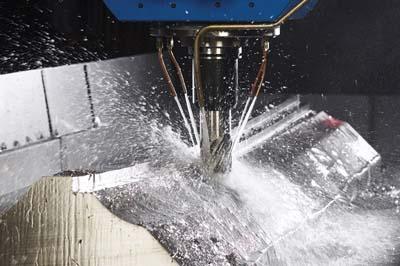
MAG's new CYCLO COOL 900 and 5000 series synthetic coolants are additive free, low foaming and specially formulated for machining titanium, Inconel, beryllium copper, hardened steels, stainless steels and other superalloys. Developed for the aerospace industry, the new coolants are an ideal replacement for semi-synthetics and soluble oils, delivering significant cost savings with lower initial cost, longer tool life, increased stock removal rates, reduced housekeeping, long sump life, and freedom from biocides/fungicides/pH adjusters. These new coolants use unique synthetic formulations to provide boundary lubricant properties, while penetrating the heat barrier in the cutting zone, even at lower pressures (300 to 400 psi), to absorb heat from the tool and part, and minimize chemical reactions between tools and workpieces. Both coolants are clear in use, permitting excellent visibility in the cutting zone.
Low-foaming CYCLO COOL 900 series coolants are intended for use in high-pressure, through-tool delivery systems at up to 2000 psi, as well as flood coolant for chip flushing. The lubrication package in the CYCLO COOL 900 series varies to cover a range of applications from lighter duty high speed (10,000 to 15,000 rpm) milling to heavy duty drilling and tapping. Three formulations are available to match the severity of the application, utilizing concentrations in the 5-7 percent range. 900 series coolants reject 99 percent of tramp oil, allowing easy removal and reducing mist levels.
CYCLO COOL 5000 is an anionic synthetic cutting fluid developed for severe to extreme metalworking applications at delivery pressures of 300 to 400 psi or intermittent high pressure. It utilizes a hybrid blend of patented lubricants that allows it to exceed the performance of high-oil containing semi-synthetics, chlorinated soluble oils and other heavy-duty synthetics. CYCLO COOL 5000 is proven to deliver increased tool life with higher cutting feeds, increased feed rates and depth of cut. Its unique EP package provides heat-activated boundary lubrication, while eliminating chlorine, sulphur and phosphorus. CYCLO COOL 5000 provides excellent corrosion control and is non-staining.
CYCLO COOL fluids are available through MAG Global Services.
Contact Details
Related Glossary Terms
- coolant
coolant
Fluid that reduces temperature buildup at the tool/workpiece interface during machining. Normally takes the form of a liquid such as soluble or chemical mixtures (semisynthetic, synthetic) but can be pressurized air or other gas. Because of water’s ability to absorb great quantities of heat, it is widely used as a coolant and vehicle for various cutting compounds, with the water-to-compound ratio varying with the machining task. See cutting fluid; semisynthetic cutting fluid; soluble-oil cutting fluid; synthetic cutting fluid.
- cutting fluid
cutting fluid
Liquid used to improve workpiece machinability, enhance tool life, flush out chips and machining debris, and cool the workpiece and tool. Three basic types are: straight oils; soluble oils, which emulsify in water; and synthetic fluids, which are water-based chemical solutions having no oil. See coolant; semisynthetic cutting fluid; soluble-oil cutting fluid; synthetic cutting fluid.
- depth of cut
depth of cut
Distance between the bottom of the cut and the uncut surface of the workpiece, measured in a direction at right angles to the machined surface of the workpiece.
- extreme pressure additives ( EP)
extreme pressure additives ( EP)
Cutting-fluid additives (chlorine, sulfur or phosphorus compounds) that chemically react with the workpiece material to minimize chipwelding. Good for high-speed machining. See cutting fluid.
- feed
feed
Rate of change of position of the tool as a whole, relative to the workpiece while cutting.
- gang cutting ( milling)
gang cutting ( milling)
Machining with several cutters mounted on a single arbor, generally for simultaneous cutting.
- metalworking
metalworking
Any manufacturing process in which metal is processed or machined such that the workpiece is given a new shape. Broadly defined, the term includes processes such as design and layout, heat-treating, material handling and inspection.
- milling
milling
Machining operation in which metal or other material is removed by applying power to a rotating cutter. In vertical milling, the cutting tool is mounted vertically on the spindle. In horizontal milling, the cutting tool is mounted horizontally, either directly on the spindle or on an arbor. Horizontal milling is further broken down into conventional milling, where the cutter rotates opposite the direction of feed, or “up” into the workpiece; and climb milling, where the cutter rotates in the direction of feed, or “down” into the workpiece. Milling operations include plane or surface milling, endmilling, facemilling, angle milling, form milling and profiling.
- stainless steels
stainless steels
Stainless steels possess high strength, heat resistance, excellent workability and erosion resistance. Four general classes have been developed to cover a range of mechanical and physical properties for particular applications. The four classes are: the austenitic types of the chromium-nickel-manganese 200 series and the chromium-nickel 300 series; the martensitic types of the chromium, hardenable 400 series; the chromium, nonhardenable 400-series ferritic types; and the precipitation-hardening type of chromium-nickel alloys with additional elements that are hardenable by solution treating and aging.
- superalloys
superalloys
Tough, difficult-to-machine alloys; includes Hastelloy, Inconel and Monel. Many are nickel-base metals.
- synthetic cutting fluid
synthetic cutting fluid
Water-based chemical solution that contains no oil. Normally contains additives that improve lubricity and prevent corrosion and rancidity. See semisynthetic cutting fluid.
- tapping
tapping
Machining operation in which a tap, with teeth on its periphery, cuts internal threads in a predrilled hole having a smaller diameter than the tap diameter. Threads are formed by a combined rotary and axial-relative motion between tap and workpiece. See tap.
- tramp oil
tramp oil
Oil that is present in a metalworking fluid mix that is not from the product concentrate. The usual sources are machine tool lubrication system leaks.