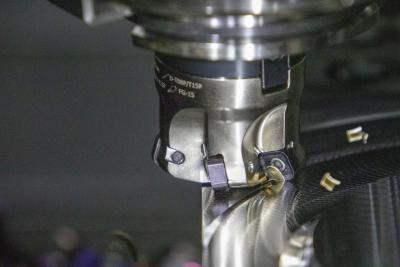
The Dormer Pramet milling assortment for die and mold has grown with several introductions, including the double-sided Pramet SNGX11 insert for high-feed milling with up to 0.07" DOC. A strong main cutting edge ensures a high level of durability and process security, especially when machining corners inside a pocket. With eight cutting edges, the square-shaped SNGX11 also represents an extremely economical solution.
Suitable for copy milling, helical interpolation, ramping, progressive plunging and facemilling, the SNGX11 is available in two geometries. M is for machining steel, but also hardened steel and cast iron. MM provides a smoother cut and is more suitable for stainless steel, soft steel and superalloys.
The range is supplemented by the new SSN11 cutter, available in diameters from 1.26" to 4.92" with intermediate sizes for die and mold applications. All cutters feature a special through-coolant design to further improve process security and a high overhang to support deep milling up to 10xD.
Meanwhile, there are also new additions to the Pramet ADMX07 milling program with a new F geometry for finishing and semifinishing applications. This sits alongside the existing M, FA and HF geometries and targets light machining of stainless steel and low carbon steels.
Suited to vibration sensitive machining, the chipbreaker features a highly positive geometry with narrow peripheral land. This reduces chatter and enables a smooth cutting action without burrs on the machined wall.
It also supports lower cutting forces, which not only reduces energy consumption but also prevents workhardening, meaning increased durability and longer tool life.
Contact Details
Related Glossary Terms
- carbon steels
carbon steels
Known as unalloyed steels and plain carbon steels. Contains, in addition to iron and carbon, manganese, phosphorus and sulfur. Characterized as low carbon, medium carbon, high carbon and free machining.
- chatter
chatter
Condition of vibration involving the machine, workpiece and cutting tool. Once this condition arises, it is often self-sustaining until the problem is corrected. Chatter can be identified when lines or grooves appear at regular intervals in the workpiece. These lines or grooves are caused by the teeth of the cutter as they vibrate in and out of the workpiece and their spacing depends on the frequency of vibration.
- chipbreaker
chipbreaker
Groove or other tool geometry that breaks chips into small fragments as they come off the workpiece. Designed to prevent chips from becoming so long that they are difficult to control, catch in turning parts and cause safety problems.
- facemilling
facemilling
Form of milling that produces a flat surface generally at right angles to the rotating axis of a cutter having teeth or inserts both on its periphery and on its end face.
- gang cutting ( milling)
gang cutting ( milling)
Machining with several cutters mounted on a single arbor, generally for simultaneous cutting.
- interpolation
interpolation
Process of generating a sufficient number of positioning commands for the servomotors driving the machine tool so the path of the tool closely approximates the ideal path. See CNC, computer numerical control; NC, numerical control.
- land
land
Part of the tool body that remains after the flutes are cut.
- milling
milling
Machining operation in which metal or other material is removed by applying power to a rotating cutter. In vertical milling, the cutting tool is mounted vertically on the spindle. In horizontal milling, the cutting tool is mounted horizontally, either directly on the spindle or on an arbor. Horizontal milling is further broken down into conventional milling, where the cutter rotates opposite the direction of feed, or “up” into the workpiece; and climb milling, where the cutter rotates in the direction of feed, or “down” into the workpiece. Milling operations include plane or surface milling, endmilling, facemilling, angle milling, form milling and profiling.
- superalloys
superalloys
Tough, difficult-to-machine alloys; includes Hastelloy, Inconel and Monel. Many are nickel-base metals.
- workhardening
workhardening
Tendency of all metals to become harder when they are machined or subjected to other stresses and strains. This trait is particularly pronounced in soft, low-carbon steel or alloys containing nickel and manganese—nonmagnetic stainless steel, high-manganese steel and the superalloys Inconel and Monel.