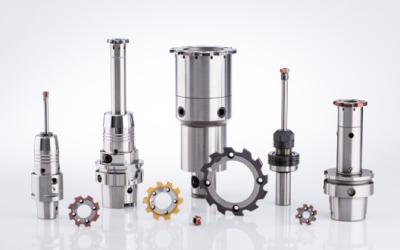
Tight bore tolerances, high surface quality and almost perfect cylindricity. Boring with reaming tools is often the last machining step in the production of precise components. In addition to the features mentioned, other properties play an important role in the production of close tolerance bores. Reaming tools are usually used for this purpose. In addition to the well-known HSS reamers, special high-performance reaming systems are increasingly proving their worth in modern production. With the DR reaming system, Paul Horn GmbH offers its own product portfolio for the economical finishing of bores.
As with other tool systems, high-performance reaming systems are also subject to demanding requirements. In addition to high process reliability, long tool life and low tool costs, modern reaming tools must fulfil further criteria. These include, among other things, the modularity of the tools. While machining with an HSS reamer is partially limited in this respect, modern reaming systems can be improved by replaceable heads with carbide inserts, modular tool lengths and various adjustment options. These include, for example, µ-accurate adjustment of concentricity and runout. Precise concentricity of the reaming inserts is the path to success. In practice, this should be within 5 µm.
Chip control
In addition to the precise grinding of the carbide insert, the appropriate tool geometry for the machining operation also plays an important role in economical reaming. Therefore, two insert orientations or side rake angles are used for reliable chip removal. Straight-insert reaming cutters are suitable for machining blind holes. Chip flow is in the opposite direction to the machining direction. Left-hand helical inserts are designed for reaming through holes only. In this case, the direction of chip flow and machining is the same.
Controlling chip breaking is an important aspect of successful boring. In deep bores, with low coolant pressure or dry machining, helical or ribbon swarf can occur. As with drilling with twist drills, the chips can be broken by briefly lifting the reamer. It is important to program as few interruptions as possible, but as many as necessary, as retractions can reduce the service life of the cutting edges. The lifting of the tool is hardly noticeable in the appearance of the machined surface.
System DR small in use
For reaming bores, a company in the vehicle manufacturing industry relies on the DR small reaming system from Horn. Before the changeover, the bores were milled or drilled and then reamed with an HSS reamer. A spokesperson for the user said, "The performance, machining cycle time and precision no longer satisfied us. New developments in our products with even finer mechanical and electrical components made it necessary to rethink the reaming process. The internal coolant supply was an important issue in this application. We machine many aluminium components. When reaming deep holes in aluminium, efficient cooling makes the difference between success and failure." The holes are reamed at a cutting feed rate of vf = 6 m/min. The machining time has been reduced by two thirds. The performance of the system has impressed the user: "We have saved a lot of time by switching to the new system. Furthermore, the tool performance as well as the quality of the reamed bores are both much better."
Reaming large diameters
With the newly developed DR-Large reaming system, Horn has extended its expertise in boring. The tool offers easy handling and high precision thanks to the proven technology of the DR tool family. The large number of cutting edges enables high cutting values and consequent time and cost savings in machining. The user achieves great flexibility thanks to the modular design and the solid carbide inserts of the tool system. There is no need for tool adjustment when changing the cutter head. The versatile and powerful interchangeable reamer system covers bore diameters from 140 mm to 200.2 mm. Horn offers servicing for simple and fast reconditioning of worn heads.
Basically, reaming is a very economical machining process. Compared to turning or milling bores to tight tolerances, reaming is many times faster and can significantly reduce unit costs. Horn has developed a high level of know-how for economical boring and has a powerful tool system in its range with the modular, high-performance DR reaming system. It covers bore diameters from 7.6 mm to 200.2 mm. All variants are equipped with internal coolant supply directly to each cutting edge. The insert interface offers high changeover accuracy to within a few µm and enables quick and uncomplicated insert exchange.
Contact Details
Related Glossary Terms
- boring
boring
Enlarging a hole that already has been drilled or cored. Generally, it is an operation of truing the previously drilled hole with a single-point, lathe-type tool. Boring is essentially internal turning, in that usually a single-point cutting tool forms the internal shape. Some tools are available with two cutting edges to balance cutting forces.
- coolant
coolant
Fluid that reduces temperature buildup at the tool/workpiece interface during machining. Normally takes the form of a liquid such as soluble or chemical mixtures (semisynthetic, synthetic) but can be pressurized air or other gas. Because of water’s ability to absorb great quantities of heat, it is widely used as a coolant and vehicle for various cutting compounds, with the water-to-compound ratio varying with the machining task. See cutting fluid; semisynthetic cutting fluid; soluble-oil cutting fluid; synthetic cutting fluid.
- feed
feed
Rate of change of position of the tool as a whole, relative to the workpiece while cutting.
- gang cutting ( milling)
gang cutting ( milling)
Machining with several cutters mounted on a single arbor, generally for simultaneous cutting.
- grinding
grinding
Machining operation in which material is removed from the workpiece by a powered abrasive wheel, stone, belt, paste, sheet, compound, slurry, etc. Takes various forms: surface grinding (creates flat and/or squared surfaces); cylindrical grinding (for external cylindrical and tapered shapes, fillets, undercuts, etc.); centerless grinding; chamfering; thread and form grinding; tool and cutter grinding; offhand grinding; lapping and polishing (grinding with extremely fine grits to create ultrasmooth surfaces); honing; and disc grinding.
- high-speed steels ( HSS)
high-speed steels ( HSS)
Available in two major types: tungsten high-speed steels (designated by letter T having tungsten as the principal alloying element) and molybdenum high-speed steels (designated by letter M having molybdenum as the principal alloying element). The type T high-speed steels containing cobalt have higher wear resistance and greater red (hot) hardness, withstanding cutting temperature up to 1,100º F (590º C). The type T steels are used to fabricate metalcutting tools (milling cutters, drills, reamers and taps), woodworking tools, various types of punches and dies, ball and roller bearings. The type M steels are used for cutting tools and various types of dies.
- milling
milling
Machining operation in which metal or other material is removed by applying power to a rotating cutter. In vertical milling, the cutting tool is mounted vertically on the spindle. In horizontal milling, the cutting tool is mounted horizontally, either directly on the spindle or on an arbor. Horizontal milling is further broken down into conventional milling, where the cutter rotates opposite the direction of feed, or “up” into the workpiece; and climb milling, where the cutter rotates in the direction of feed, or “down” into the workpiece. Milling operations include plane or surface milling, endmilling, facemilling, angle milling, form milling and profiling.
- modular design ( modular construction)
modular design ( modular construction)
Manufacturing of a product in subassemblies that permits fast and simple replacement of defective assemblies and tailoring of the product for different purposes. See interchangeable parts.
- rake
rake
Angle of inclination between the face of the cutting tool and the workpiece. If the face of the tool lies in a plane through the axis of the workpiece, the tool is said to have a neutral, or zero, rake. If the inclination of the tool face makes the cutting edge more acute than when the rake angle is zero, the rake is positive. If the inclination of the tool face makes the cutting edge less acute or more blunt than when the rake angle is zero, the rake is negative.
- reamer
reamer
Rotating cutting tool used to enlarge a drilled hole to size. Normally removes only a small amount of stock. The workpiece supports the multiple-edge cutting tool. Also for contouring an existing hole.
- swarf
swarf
Metal fines and grinding wheel particles generated during grinding.
- tolerance
tolerance
Minimum and maximum amount a workpiece dimension is allowed to vary from a set standard and still be acceptable.
- turning
turning
Workpiece is held in a chuck, mounted on a face plate or secured between centers and rotated while a cutting tool, normally a single-point tool, is fed into it along its periphery or across its end or face. Takes the form of straight turning (cutting along the periphery of the workpiece); taper turning (creating a taper); step turning (turning different-size diameters on the same work); chamfering (beveling an edge or shoulder); facing (cutting on an end); turning threads (usually external but can be internal); roughing (high-volume metal removal); and finishing (final light cuts). Performed on lathes, turning centers, chucking machines, automatic screw machines and similar machines.