Contact Details
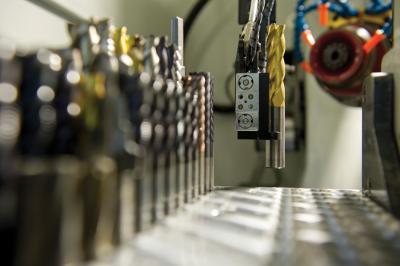
ANCA’s EDGe-Spark erosion power generator controls the energy level of the eroding spark for optimal surface finish, material removal and cycle time. It also enables a double-ended HSK wheel spindle for eroding PCD and grinding carbide and HSS.
According to ANCA, the ability to manufacture a variety of tools (up to 220 mm or 8.66” in diameter and up to 20 kg or 44 lbs. in weight) makes the EDGe ideal for users looking to reduce the risk associated with moving into the growing PCD-side of the tool grinding business and is suitable for a variety of tools and applications.
Another advantage of the EDGe is that it performing erosion and grinding operations on the one machine, which reduces machine setup time. It also enables improved tool accuracy due to a single setup and fewer machines required.
Duncan Thompson, EDGe product manager, ANCA, said “The proprietary EDGe-Spark generator monitors and controls the energy level of every spark for the resistivity of the substrate, be it tungsten carbide, diamond or cobalt binder. It automatically detects the substrate and adaptively adjusts the gap distance for optimum surface finish, material removal and cycle time. What’s more, it provides exceptional operator feedback in real time. We take the precision and high accuracy demands of our customers very seriously."
Testing of tools eroded on the EDGe machine resulted with better figures for cutting force, exit burrs on CFRP and drill life than ground tools achieving a surface finish on tools finer than 0.2 microns Ra.
The most recent comparative tests of the EDGe against competitive products prove its performance is equal in terms of material-removal rates and cutting-edge quality and surface finish yet at a more economical price point.
ANCA, well known for its ToolRoom design software, also says that the EDGe has a fast, easy-to-use interface for inputting tool geometry. The ANCA software includes integrated 3D graphics, is used to adjust power generator settings, and is designed to create programs for a wide range of tool types. ANCA’s tool design software provides the flexibility and user-friendliness for a wide range of tool types and applications for both "erosion" and "grinding." In addition, ANCA can include its LaserPlus in-process tool measuring system to support accurate manufacture of PCD cutting tools.
The process to manufacture a PCD tool is relatively unchanged: wire EDM the PCD segment to size and shape, pocket grind the tool body so the PCD segment can be located on the tool, and braze the PCD segment to the tool body. The final stages of the PCD tool production can traditionally involve multiple machines to complete the tool to the finished requirement. The ANCA EDGe is ideal for the final stages of PCD tool production, resulting in an eroded finish with a surface roughness less than 0.2µm Ra. Depending upon the surface roughness requirements and whether an eroded or ground surface is required, the EDGe machine can eliminate some of the grinding operations.
ANCA partnered with Precorp, a leading U.S. manufacturer of PCD cutting tools and a key supplier to companies such as Boeing, to develop the technology. This partnership means the EDGe is suitable for grinding PCD tools that are essential for machining composite materials often used in aerospace applications.
Related Glossary Terms
- cutting force
cutting force
Engagement of a tool’s cutting edge with a workpiece generates a cutting force. Such a cutting force combines tangential, feed and radial forces, which can be measured by a dynamometer. Of the three cutting force components, tangential force is the greatest. Tangential force generates torque and accounts for more than 95 percent of the machining power. See dynamometer.
- electrical-discharge machining ( EDM)
electrical-discharge machining ( EDM)
Process that vaporizes conductive materials by controlled application of pulsed electrical current that flows between a workpiece and electrode (tool) in a dielectric fluid. Permits machining shapes to tight accuracies without the internal stresses conventional machining often generates. Useful in diemaking.
- grinding
grinding
Machining operation in which material is removed from the workpiece by a powered abrasive wheel, stone, belt, paste, sheet, compound, slurry, etc. Takes various forms: surface grinding (creates flat and/or squared surfaces); cylindrical grinding (for external cylindrical and tapered shapes, fillets, undercuts, etc.); centerless grinding; chamfering; thread and form grinding; tool and cutter grinding; offhand grinding; lapping and polishing (grinding with extremely fine grits to create ultrasmooth surfaces); honing; and disc grinding.
- high-speed steels ( HSS)
high-speed steels ( HSS)
Available in two major types: tungsten high-speed steels (designated by letter T having tungsten as the principal alloying element) and molybdenum high-speed steels (designated by letter M having molybdenum as the principal alloying element). The type T high-speed steels containing cobalt have higher wear resistance and greater red (hot) hardness, withstanding cutting temperature up to 1,100º F (590º C). The type T steels are used to fabricate metalcutting tools (milling cutters, drills, reamers and taps), woodworking tools, various types of punches and dies, ball and roller bearings. The type M steels are used for cutting tools and various types of dies.
- polycrystalline diamond ( PCD)
polycrystalline diamond ( PCD)
Cutting tool material consisting of natural or synthetic diamond crystals bonded together under high pressure at elevated temperatures. PCD is available as a tip brazed to a carbide insert carrier. Used for machining nonferrous alloys and nonmetallic materials at high cutting speeds.
- tungsten carbide ( WC)
tungsten carbide ( WC)
Intermetallic compound consisting of equal parts, by atomic weight, of tungsten and carbon. Sometimes tungsten carbide is used in reference to the cemented tungsten carbide material with cobalt added and/or with titanium carbide or tantalum carbide added. Thus, the tungsten carbide may be used to refer to pure tungsten carbide as well as co-bonded tungsten carbide, which may or may not contain added titanium carbide and/or tantalum carbide.
- wire EDM
wire EDM
Process similar to ram electrical-discharge machining except a small-diameter copper or brass wire is used as a traveling electrode. Usually used in conjunction with a CNC and only works when a part is to be cut completely through. A common analogy is wire electrical-discharge machining is like an ultraprecise, electrical, contour-sawing operation.