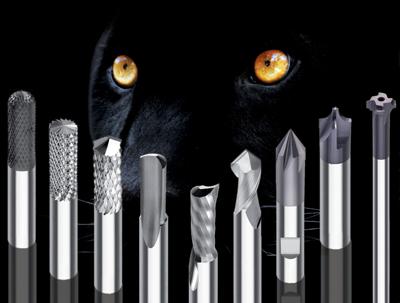
Cutting plastics and composite materials is a special discipline. Only with application-optimized tools can acceptable service lives and qualities be achieved in a cost-effective manner. To attain success, cutters are therefore particularly reliant on their tool and system suppliers. With a new range of high-performance SC special end mills, tool manufacturer Inovatools helps producers to tackle the special cutting problems presented by hybrid materials and to solve them reliably.
Composites such as carbon- and glass-fiber-reinforced plastic (CFRP, GFRP) and combined steel, titanium and aluminum, such as GLARE, are now used extensively in such areas as the automotive and aerospace industries. After all, these lightweight construction materials are available wherever low weight, low component volume and high mechanical performance are required.
These sandwich materials present very particular challenges for cutters. The main problem lies in the material mix, with the materials used having diverse properties and parameters. Accordingly, the list of cutting problems is long. For example, different layer thicknesses of each sandwich structure, the sometimes very high abrasiveness of the hard carbon fibers, the danger of delamination, chipping and fiber bursting, occasionally very high heat sensitivity and inadequate chip evacuation make life difficult for the tools.
Norbert Geyer, head of Coating at Inovatools: "There is often enormous potential for optimization in machining strategies for composite materials. With our next-generation tools, we are helping to realize this potential. For example, our tools for edge machining, trimming, groove milling and contouring etc. are optimally designed for the various milling applications. That begins right from the selection of the right carbide metal and continues through the special geometry with application-focused cutting, chip and clearance angles through to the thin, hard-wearing diamond coating. It must be noted that, depending on the cutting task, diamond-coated tools are not necessarily better than those without coatings."
One example is the new Inovatools SC routers. These end mills, with or without drill bits, are designed such that, due to a special pitch angle, for example, the cutting forces are directed to the center of the workpiece, preventing such issues as delamination. SC end mills from the SoftLine series (single-tooth; single-tooth full-radius) have finely lapped chip grooves. This prevents adhesion and allows the chips to flow optimally away from the contact zone.
For composite machining, Inovatools continues to offer engraving blanks, gravers (60°, 90°, 100°), multimills, forward and backward deburring tools, 90° copying and fiber end mills and quarter-circle end mills of various dimensions and designs.
All Inovatools end mills can be delivered wherever they are required, with the option of a high-performance diamond coating as well. They have an extremely smooth and fine crystalline surface topography and adhere very well to the carbide metal substrate. They also make the tool resistant to chemical effects while also minimizing friction and preventing resin from adhering to the end mill. One key advantage of the coating is that it does not affect the microgeometry of the tool, which means that cutting edges remain sharp. Norbert Geyer: "Thanks to the special combination of geometry and chip design, the new Inovatools end mills work free of vibration and rattling and exhibit very high cutting capacity with extremely long service lives."
Contact Details
Related Glossary Terms
- clearance
clearance
Space provided behind a tool’s land or relief to prevent rubbing and subsequent premature deterioration of the tool. See land; relief.
- composites
composites
Materials composed of different elements, with one element normally embedded in another, held together by a compatible binder.
- gang cutting ( milling)
gang cutting ( milling)
Machining with several cutters mounted on a single arbor, generally for simultaneous cutting.
- milling
milling
Machining operation in which metal or other material is removed by applying power to a rotating cutter. In vertical milling, the cutting tool is mounted vertically on the spindle. In horizontal milling, the cutting tool is mounted horizontally, either directly on the spindle or on an arbor. Horizontal milling is further broken down into conventional milling, where the cutter rotates opposite the direction of feed, or “up” into the workpiece; and climb milling, where the cutter rotates in the direction of feed, or “down” into the workpiece. Milling operations include plane or surface milling, endmilling, facemilling, angle milling, form milling and profiling.
- milling machine ( mill)
milling machine ( mill)
Runs endmills and arbor-mounted milling cutters. Features include a head with a spindle that drives the cutters; a column, knee and table that provide motion in the three Cartesian axes; and a base that supports the components and houses the cutting-fluid pump and reservoir. The work is mounted on the table and fed into the rotating cutter or endmill to accomplish the milling steps; vertical milling machines also feed endmills into the work by means of a spindle-mounted quill. Models range from small manual machines to big bed-type and duplex mills. All take one of three basic forms: vertical, horizontal or convertible horizontal/vertical. Vertical machines may be knee-type (the table is mounted on a knee that can be elevated) or bed-type (the table is securely supported and only moves horizontally). In general, horizontal machines are bigger and more powerful, while vertical machines are lighter but more versatile and easier to set up and operate.
- pitch
pitch
1. On a saw blade, the number of teeth per inch. 2. In threading, the number of threads per inch.