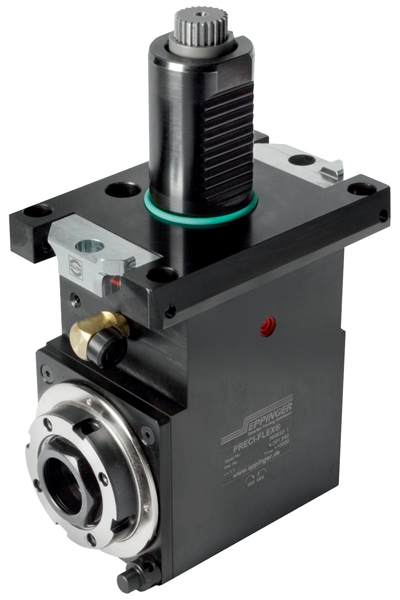
The EPPINGER Trifix tool positioning system from EXSYS Tool Inc. facilitates quick and accurate exchanges of both static and driven tooling for DMG/Gildemeister multi-tasking machines.
Based on the VDI interface, the system can reduce tool setup times by up to 80 percent compared to prior methods while delivering positioning accuracy within 10µm between tool stations and single-position repeatability of less than 5µm at a tool length of 3.9" (100mm).
According to EXSYS Tool, when searching for ways to increase productivity, it's important to evaluate even the smallest steps of a production process. Minor adjustments, such as the incorporation of an improved VDI interface, can greatly reduce setup time, and the Trifix is a great example as it provides a faster, more accurate tool holder exchange.
After the user initially aligns the Trifix unit in the lathe turret, further adjustment for subsequent tool changes becomes unnecessary. As a result, manufacturers can preset their tools off the machine, further reducing their setup time.
Tooling can be mounted with four additional hold down screws to maximize rigidity in heavy-chipload operations such as milling, and employing the Trifix system does not prevent a facility from using other tooling it already has.
Contact Details
Related Glossary Terms
- gang cutting ( milling)
gang cutting ( milling)
Machining with several cutters mounted on a single arbor, generally for simultaneous cutting.
- lathe
lathe
Turning machine capable of sawing, milling, grinding, gear-cutting, drilling, reaming, boring, threading, facing, chamfering, grooving, knurling, spinning, parting, necking, taper-cutting, and cam- and eccentric-cutting, as well as step- and straight-turning. Comes in a variety of forms, ranging from manual to semiautomatic to fully automatic, with major types being engine lathes, turning and contouring lathes, turret lathes and numerical-control lathes. The engine lathe consists of a headstock and spindle, tailstock, bed, carriage (complete with apron) and cross slides. Features include gear- (speed) and feed-selector levers, toolpost, compound rest, lead screw and reversing lead screw, threading dial and rapid-traverse lever. Special lathe types include through-the-spindle, camshaft and crankshaft, brake drum and rotor, spinning and gun-barrel machines. Toolroom and bench lathes are used for precision work; the former for tool-and-die work and similar tasks, the latter for small workpieces (instruments, watches), normally without a power feed. Models are typically designated according to their “swing,” or the largest-diameter workpiece that can be rotated; bed length, or the distance between centers; and horsepower generated. See turning machine.
- milling
milling
Machining operation in which metal or other material is removed by applying power to a rotating cutter. In vertical milling, the cutting tool is mounted vertically on the spindle. In horizontal milling, the cutting tool is mounted horizontally, either directly on the spindle or on an arbor. Horizontal milling is further broken down into conventional milling, where the cutter rotates opposite the direction of feed, or “up” into the workpiece; and climb milling, where the cutter rotates in the direction of feed, or “down” into the workpiece. Milling operations include plane or surface milling, endmilling, facemilling, angle milling, form milling and profiling.