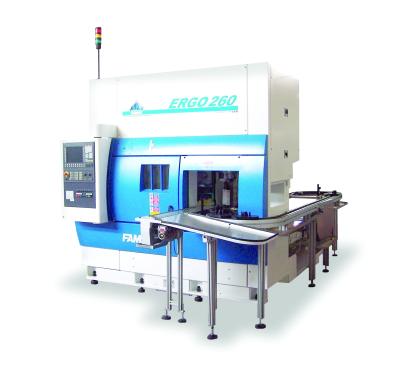
FAMAR S.r.l manufactures 16 different models of vertical lathes specialized in turning, but also in milling, boring, drilling and tapping. Thanks to electro spindles added to the turret, FAMAR machines are able to do the gear cutting and grinding. Furthermore, through the technology of fixed or driven tools fixed on the turrets, FAMAR lathes can even allow the machining of heat-treated materials.
ERGO operating system is quite simple: while the spindle carrier of the “Z” vertical axis, running over closed lubricated guideways, brings the centred spindle to its working position, the movement of the “X” axis is generated by the sliding of the complete carrier over preloaded guides, which are positioned over the bedframe. Recirculating ballscrews guarantee the best precision level of the moving, the highest speed and acceleration, very good loading ability associated with long durability and a simple maintenance. The axes are motorized by asynchronous brushless motors.
The machine bedframe (FAMAR patent) is made of electro-welded steel; its loop shape reportedly guarantees high stability and excellent sturdiness. Being filled with special polymerized concrete that is responsible for an extraordinary level of vibration absorption, as well as thermic stability.
Comparing this particular closed-ring conception with the traditional hanging spindle technology, this solution performs much better results both in repositioning precision and in displacements speed.
The special turret that is fitted on FAMAR machines is flanged on the bedframe. This solution eliminates machining errors due to heat changes. Moreover this system offers greater stability, even during heavy machining, and a more homogeneous spread of the cutting forces.
All FAMAR machines are ergonomic and manufactured according to TPM and EC standards, so that all the mechanical and electronic components can be easily accessed to simplify inspections and maintenance.
The work area and the loading/unloading area are isolated and protected from the machining chips and separated by two sliding metal guards. This setup assures cleanliness and ideal workplace conditions.
The NC system is the digital ground configuration of Siemens 840 D the FANUC 21T.
Contact Details
Related Glossary Terms
- boring
boring
Enlarging a hole that already has been drilled or cored. Generally, it is an operation of truing the previously drilled hole with a single-point, lathe-type tool. Boring is essentially internal turning, in that usually a single-point cutting tool forms the internal shape. Some tools are available with two cutting edges to balance cutting forces.
- gang cutting ( milling)
gang cutting ( milling)
Machining with several cutters mounted on a single arbor, generally for simultaneous cutting.
- grinding
grinding
Machining operation in which material is removed from the workpiece by a powered abrasive wheel, stone, belt, paste, sheet, compound, slurry, etc. Takes various forms: surface grinding (creates flat and/or squared surfaces); cylindrical grinding (for external cylindrical and tapered shapes, fillets, undercuts, etc.); centerless grinding; chamfering; thread and form grinding; tool and cutter grinding; offhand grinding; lapping and polishing (grinding with extremely fine grits to create ultrasmooth surfaces); honing; and disc grinding.
- milling
milling
Machining operation in which metal or other material is removed by applying power to a rotating cutter. In vertical milling, the cutting tool is mounted vertically on the spindle. In horizontal milling, the cutting tool is mounted horizontally, either directly on the spindle or on an arbor. Horizontal milling is further broken down into conventional milling, where the cutter rotates opposite the direction of feed, or “up” into the workpiece; and climb milling, where the cutter rotates in the direction of feed, or “down” into the workpiece. Milling operations include plane or surface milling, endmilling, facemilling, angle milling, form milling and profiling.
- numerical control ( NC)
numerical control ( NC)
Any controlled equipment that allows an operator to program its movement by entering a series of coded numbers and symbols. See CNC, computer numerical control; DNC, direct numerical control.
- tapping
tapping
Machining operation in which a tap, with teeth on its periphery, cuts internal threads in a predrilled hole having a smaller diameter than the tap diameter. Threads are formed by a combined rotary and axial-relative motion between tap and workpiece. See tap.
- turning
turning
Workpiece is held in a chuck, mounted on a face plate or secured between centers and rotated while a cutting tool, normally a single-point tool, is fed into it along its periphery or across its end or face. Takes the form of straight turning (cutting along the periphery of the workpiece); taper turning (creating a taper); step turning (turning different-size diameters on the same work); chamfering (beveling an edge or shoulder); facing (cutting on an end); turning threads (usually external but can be internal); roughing (high-volume metal removal); and finishing (final light cuts). Performed on lathes, turning centers, chucking machines, automatic screw machines and similar machines.