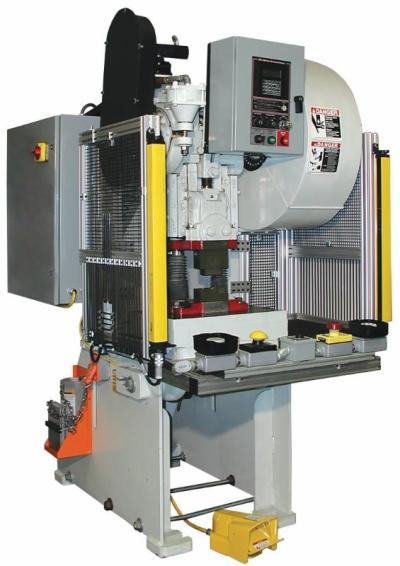
Rockford Systems offers its EX-AL barrier guarding systems, now available custom-designed and built to meet the safety standards of the Occupational Safety & Health Administration (OSHA) and American National Standards Institute (ANSI). By harnessing more than 45 years of experience in machine safeguarding, Rockford Systems is able to deliver customized guarding for traditional presses, milling machines, lathes and drills, as well as the newest automation systems. In this age of Industry 4.0 and the Industrial Internet of Things, Rockford Systems has been a pioneer in providing barrier guarding for welding cells, robotic cells, laser cutting areas and process automation systems.
Rockford Systems EX-AL guarding systems can be designed and fabricated as custom barriers to reduce or eliminate access to hazardous areas on machines. Customized safety shields for metalcutting and turning machines provide protection from flying chips, debris, coolant and cutting fluid.
EX-AL barrier guards are strong, economical solutions to plant safety needs. They feature a rugged aluminum extrusion framework that is virtually maintenance-free and allows for the integration of access doors or other openings for operator access, machine maintenance, feeding materials, and removal of both parts and scrap. Single-panel and multiple-panel designs capable of mounting to different areas on machines or the floor give safety managers an almost endless variety of customizable choices. PVC coated mesh and clear or colored polycarbonate make up the fixed area of the panels, with adjustable steel hairpins or fixed steel rods available for material feeding, part and scrap chutes, conveyors, and other ancillary equipment on machines.
Each EX-AL system is fabricated for a specific machine or application. Customers should provide exact measurements of their machinery, the guard design, and take into account its safety and productivity requirements. Rockford Systems machine safeguarding specialists are also available for on-site machine surveys and design consultation.
Contact Details
Related Glossary Terms
- coolant
coolant
Fluid that reduces temperature buildup at the tool/workpiece interface during machining. Normally takes the form of a liquid such as soluble or chemical mixtures (semisynthetic, synthetic) but can be pressurized air or other gas. Because of water’s ability to absorb great quantities of heat, it is widely used as a coolant and vehicle for various cutting compounds, with the water-to-compound ratio varying with the machining task. See cutting fluid; semisynthetic cutting fluid; soluble-oil cutting fluid; synthetic cutting fluid.
- cutting fluid
cutting fluid
Liquid used to improve workpiece machinability, enhance tool life, flush out chips and machining debris, and cool the workpiece and tool. Three basic types are: straight oils; soluble oils, which emulsify in water; and synthetic fluids, which are water-based chemical solutions having no oil. See coolant; semisynthetic cutting fluid; soluble-oil cutting fluid; synthetic cutting fluid.
- extrusion
extrusion
Conversion of an ingot or billet into lengths of uniform cross section by forcing metal to flow plastically through a die orifice.
- gang cutting ( milling)
gang cutting ( milling)
Machining with several cutters mounted on a single arbor, generally for simultaneous cutting.
- metalcutting ( material cutting)
metalcutting ( material cutting)
Any machining process used to part metal or other material or give a workpiece a new configuration. Conventionally applies to machining operations in which a cutting tool mechanically removes material in the form of chips; applies to any process in which metal or material is removed to create new shapes. See metalforming.
- milling
milling
Machining operation in which metal or other material is removed by applying power to a rotating cutter. In vertical milling, the cutting tool is mounted vertically on the spindle. In horizontal milling, the cutting tool is mounted horizontally, either directly on the spindle or on an arbor. Horizontal milling is further broken down into conventional milling, where the cutter rotates opposite the direction of feed, or “up” into the workpiece; and climb milling, where the cutter rotates in the direction of feed, or “down” into the workpiece. Milling operations include plane or surface milling, endmilling, facemilling, angle milling, form milling and profiling.
- turning
turning
Workpiece is held in a chuck, mounted on a face plate or secured between centers and rotated while a cutting tool, normally a single-point tool, is fed into it along its periphery or across its end or face. Takes the form of straight turning (cutting along the periphery of the workpiece); taper turning (creating a taper); step turning (turning different-size diameters on the same work); chamfering (beveling an edge or shoulder); facing (cutting on an end); turning threads (usually external but can be internal); roughing (high-volume metal removal); and finishing (final light cuts). Performed on lathes, turning centers, chucking machines, automatic screw machines and similar machines.