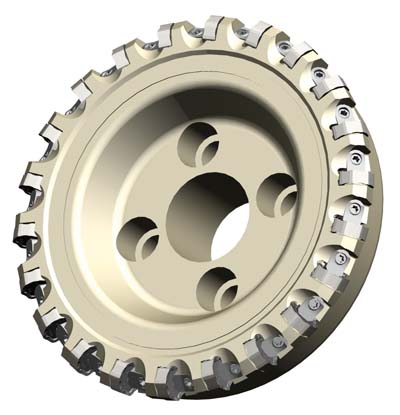
Walter USA LLC announces the expansion of its Xtra-tec F4045 milling cutter line with a new cutter designed with a medium pitch for use on lower horsepower machines and for difficult to fixture workpieces.
Stable machines, workpieces and clamping arrangements are required for maximum cutting rates. However, sometimes feeds and speeds need to be scaled back because workpieces with complicated shapes do not always permit rock-solid clamping. That's where a tool such as the Xtra-tec F4045 with medium pitch comes" The medium pitch allows the tool to deliver optimum performance in conditions of limited stability, and the milling cutter's other features enable it to boost productivity in a wide array of situations.
These other features include negative-shaped inserts with 14 cutting edges, seven per side. The inserts are pressed with a positive rake face which allows for freer cutting geometry that permits high cutting volumes in lower horsepower machines. Also, its innovative insert clamping system locks the inserts securely in their seats. The clamping wedge pivots to the side after just a few turns of the clamping screw, allowing rapid insert change.
Three geometry shapes, stable, universal and easy-cutting, enable adaptation to a range of different applications. Cutting rates and tool life are further enhanced by the use of Walter's Tiger-tec coatings.
The F4045 comes with either Tiger-tec Silver or with the PVD Tiger-tec grade WKK25 for especially difficult machining conditions. The Tiger-tec Silver advantage begins with a newly formulated aluminum oxide coating with an optimized microstructure that delivers superior resistance to crater and flank wear as well as to plastic deformation.
Contact Details
Related Glossary Terms
- aluminum oxide
aluminum oxide
Aluminum oxide, also known as corundum, is used in grinding wheels. The chemical formula is Al2O3. Aluminum oxide is the base for ceramics, which are used in cutting tools for high-speed machining with light chip removal. Aluminum oxide is widely used as coating material applied to carbide substrates by chemical vapor deposition. Coated carbide inserts with Al2O3 layers withstand high cutting speeds, as well as abrasive and crater wear.
- fixture
fixture
Device, often made in-house, that holds a specific workpiece. See jig; modular fixturing.
- flank wear
flank wear
Reduction in clearance on the tool’s flank caused by contact with the workpiece. Ultimately causes tool failure.
- gang cutting ( milling)
gang cutting ( milling)
Machining with several cutters mounted on a single arbor, generally for simultaneous cutting.
- microstructure
microstructure
Structure of a metal as revealed by microscopic examination of the etched surface of a polished specimen.
- milling
milling
Machining operation in which metal or other material is removed by applying power to a rotating cutter. In vertical milling, the cutting tool is mounted vertically on the spindle. In horizontal milling, the cutting tool is mounted horizontally, either directly on the spindle or on an arbor. Horizontal milling is further broken down into conventional milling, where the cutter rotates opposite the direction of feed, or “up” into the workpiece; and climb milling, where the cutter rotates in the direction of feed, or “down” into the workpiece. Milling operations include plane or surface milling, endmilling, facemilling, angle milling, form milling and profiling.
- milling cutter
milling cutter
Loosely, any milling tool. Horizontal cutters take the form of plain milling cutters, plain spiral-tooth cutters, helical cutters, side-milling cutters, staggered-tooth side-milling cutters, facemilling cutters, angular cutters, double-angle cutters, convex and concave form-milling cutters, straddle-sprocket cutters, spur-gear cutters, corner-rounding cutters and slitting saws. Vertical cutters use shank-mounted cutting tools, including endmills, T-slot cutters, Woodruff keyseat cutters and dovetail cutters; these may also be used on horizontal mills. See milling.
- physical vapor deposition ( PVD)
physical vapor deposition ( PVD)
Tool-coating process performed at low temperature (500° C), compared to chemical vapor deposition (1,000° C). Employs electric field to generate necessary heat for depositing coating on a tool’s surface. See CVD, chemical vapor deposition.
- pitch
pitch
1. On a saw blade, the number of teeth per inch. 2. In threading, the number of threads per inch.
- plastic deformation
plastic deformation
Permanent (inelastic) distortion of metals under applied stresses that strain the material beyond its elastic limit.
- rake
rake
Angle of inclination between the face of the cutting tool and the workpiece. If the face of the tool lies in a plane through the axis of the workpiece, the tool is said to have a neutral, or zero, rake. If the inclination of the tool face makes the cutting edge more acute than when the rake angle is zero, the rake is positive. If the inclination of the tool face makes the cutting edge less acute or more blunt than when the rake angle is zero, the rake is negative.