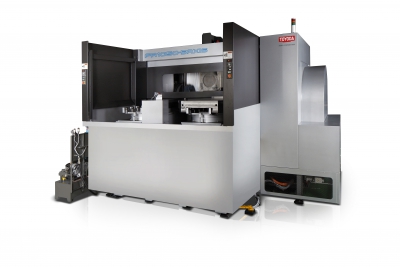
Toyoda’s FA1050 5-axis horizontal machining center is suitable for boring, endmilling, threading and U-axis machining. Toyoda says it starts at the core of the machine to provide long machine life while minimizing tool breakage and unneeded upkeep.
Toyoda’s FA1050 5-axis machine begins with a solid cast iron base combined with full-plate clamping mechanism withholding up to 26,000 lbs. of table clamp force. Shop owners can expect to achieve stable axial feed at high speeds during heavy workloads because of the machines rigid core.
Spindle support from four heavy duty bearings—robust double-row cylindrical roller bearings and dual angular contact thrust bearings—eliminates vibration. The boxway machine performs rapid acceleration and consistency with its 60-hp spindle drive motor at 6,000 rpm of geared head tough cutting.
Unstable machining on difficult metals is a recipe for disaster. The FA1050 5-axis’ solid structure secures versatile, accurate and highly competitive machining on difficult materials such as Hastelloy, Inconel and Nichrome.
Contact Details
Related Glossary Terms
- boring
boring
Enlarging a hole that already has been drilled or cored. Generally, it is an operation of truing the previously drilled hole with a single-point, lathe-type tool. Boring is essentially internal turning, in that usually a single-point cutting tool forms the internal shape. Some tools are available with two cutting edges to balance cutting forces.
- endmilling
endmilling
Operation in which the cutter is mounted on the machine’s spindle rather than on an arbor. Commonly associated with facing operations on a milling machine.
- feed
feed
Rate of change of position of the tool as a whole, relative to the workpiece while cutting.
- machining center
machining center
CNC machine tool capable of drilling, reaming, tapping, milling and boring. Normally comes with an automatic toolchanger. See automatic toolchanger.
- threading
threading
Process of both external (e.g., thread milling) and internal (e.g., tapping, thread milling) cutting, turning and rolling of threads into particular material. Standardized specifications are available to determine the desired results of the threading process. Numerous thread-series designations are written for specific applications. Threading often is performed on a lathe. Specifications such as thread height are critical in determining the strength of the threads. The material used is taken into consideration in determining the expected results of any particular application for that threaded piece. In external threading, a calculated depth is required as well as a particular angle to the cut. To perform internal threading, the exact diameter to bore the hole is critical before threading. The threads are distinguished from one another by the amount of tolerance and/or allowance that is specified. See turning.