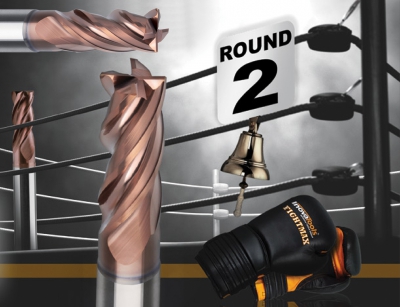
With the “FightMax” mill series, the tool manufacturer Inovatools is sending a winner into the ring for machining steel materials. The tool specialists have once again hit the bull’s eye with the new VHM-HPC roughing/finishing milling cutter “FightMax” INOX. The special geometry and chip clearance as well as the defined cutting edge preparation in combination with the microgeometry as well as high-performance coating prepare the new milling cutter optimally for meeting the special cutting requirements of this versatile material with the right tactics.
Nirosta, chromium steel, VA steel, rust-free steel, nickel-chromium steel – INOX has many names in the cutting world. And just as the names for this material group are hugely diverse, so too are the specific characteristics depending on the chromium, nickel, titanium and molybdenum share. On the one hand, this defines the area of application, e.g. in the foodstuffs or chemical industry, etc.; on the other hand, these characteristics make cutting complex and difficult.
“Successful cutting of all materials covered by the superordinate term INOX is a special discipline,” said Douglas Kline, managing director at Inovatools USA LLC. “The tool basically has to fight with the edge zone hardening and the material’s high level of toughness. Since the materials are poor thermal conductors, rapid chip clearance is particularly important. In addition, the tool must have been designed in such a way that the chips that tend to bond and stick can be discharged reliably. What is therefore required are tools that have been precisely tuned to meet the requirements of INOX machining.”
In the “FightMax” INOX, Inovatools uses a balance mixing ratio of special ultrafine grain carbide. The four-edged HPC power package has an unevenly split and an unevenly twisted geometry with highly polished chip space. This gives the tool the necessary performance, ensures quiet, vibration-free concentricity, and guarantees quick and reliable chip removal. This is supported by the smooth high-performance coating DUOCON, which also gives the “FightMax” INOX the necessary stability in the fight. The VHM-HPC roughing/finishing milling cutter is available in short and long versions with diameters from 6.00 mm to 20.00 mm.
Kline said: “The new milling cutter is particularly resilient thanks to our specific microgeometry for INOX machining. In addition, the defined cutting edge rounding gives the ‘FightMax’ INOX extreme edge stability when HPC milling. This makes it suitable for the special cutting requirements and also guarantees very long service lives, even with high feed rates and cutting speeds.”
In practice, the roughing/finishing milling cutter emerges as a winner, e.g. in machining the austenitic, acid-resistant 18/10 Cr-Ni steel 1.4301 (X5CrNi18-10). According to Inovatools, the “FightMax” delivers an up to 41 percent longer service life in the wear test compared to a comparable tool from the market (cutting data: vc = 91 m/min, vf = 426 mm/min, ae = 11 mm, ap = 12 mm) with very fine surface quality.
Kline said: “The ‘FightMax’ INOX has been specially optimized in line with the unique cutting conditions of rust-free materials. Thanks to its design advantages, it is suitable as a roughing and finishing milling cutter depending on the cutting parameters. Our technical consultants will be happy to give tips on selecting the right tool depending on the INOX material group and on setting the specified operating values. Naturally, it is also possible to identify the right tool for a specific cutting application with our cutting data computer INOCUT, for example. This app is available at www.schnittdaten.eu and www.inovatools.eu. It works via the specific recommendation of cutting values, depending on the working cross-section, material and tool.”
Contact Details
Related Glossary Terms
- chip clearance
chip clearance
In milling, the groove or space provided in the cutter body that allows chips to be formed by the inserts.
- clearance
clearance
Space provided behind a tool’s land or relief to prevent rubbing and subsequent premature deterioration of the tool. See land; relief.
- edge preparation
edge preparation
Conditioning of the cutting edge, such as a honing or chamfering, to make it stronger and less susceptible to chipping. A chamfer is a bevel on the tool’s cutting edge; the angle is measured from the cutting face downward and generally varies from 25° to 45°. Honing is the process of rounding or blunting the cutting edge with abrasives, either manually or mechanically.
- feed
feed
Rate of change of position of the tool as a whole, relative to the workpiece while cutting.
- gang cutting ( milling)
gang cutting ( milling)
Machining with several cutters mounted on a single arbor, generally for simultaneous cutting.
- hardening
hardening
Process of increasing the surface hardness of a part. It is accomplished by heating a piece of steel to a temperature within or above its critical range and then cooling (or quenching) it rapidly. In any heat-treatment operation, the rate of heating is important. Heat flows from the exterior to the interior of steel at a definite rate. If the steel is heated too quickly, the outside becomes hotter than the inside and the desired uniform structure cannot be obtained. If a piece is irregular in shape, a slow heating rate is essential to prevent warping and cracking. The heavier the section, the longer the heating time must be to achieve uniform results. Even after the correct temperature has been reached, the piece should be held at the temperature for a sufficient period of time to permit its thickest section to attain a uniform temperature. See workhardening.
- milling
milling
Machining operation in which metal or other material is removed by applying power to a rotating cutter. In vertical milling, the cutting tool is mounted vertically on the spindle. In horizontal milling, the cutting tool is mounted horizontally, either directly on the spindle or on an arbor. Horizontal milling is further broken down into conventional milling, where the cutter rotates opposite the direction of feed, or “up” into the workpiece; and climb milling, where the cutter rotates in the direction of feed, or “down” into the workpiece. Milling operations include plane or surface milling, endmilling, facemilling, angle milling, form milling and profiling.
- milling cutter
milling cutter
Loosely, any milling tool. Horizontal cutters take the form of plain milling cutters, plain spiral-tooth cutters, helical cutters, side-milling cutters, staggered-tooth side-milling cutters, facemilling cutters, angular cutters, double-angle cutters, convex and concave form-milling cutters, straddle-sprocket cutters, spur-gear cutters, corner-rounding cutters and slitting saws. Vertical cutters use shank-mounted cutting tools, including endmills, T-slot cutters, Woodruff keyseat cutters and dovetail cutters; these may also be used on horizontal mills. See milling.
- milling machine ( mill)
milling machine ( mill)
Runs endmills and arbor-mounted milling cutters. Features include a head with a spindle that drives the cutters; a column, knee and table that provide motion in the three Cartesian axes; and a base that supports the components and houses the cutting-fluid pump and reservoir. The work is mounted on the table and fed into the rotating cutter or endmill to accomplish the milling steps; vertical milling machines also feed endmills into the work by means of a spindle-mounted quill. Models range from small manual machines to big bed-type and duplex mills. All take one of three basic forms: vertical, horizontal or convertible horizontal/vertical. Vertical machines may be knee-type (the table is mounted on a knee that can be elevated) or bed-type (the table is securely supported and only moves horizontally). In general, horizontal machines are bigger and more powerful, while vertical machines are lighter but more versatile and easier to set up and operate.