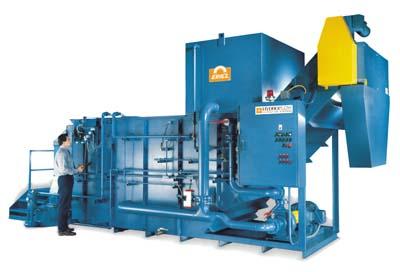
Eriez Hydroflow offers complete filter system products for a variety of metalworking applications, including standard machining, conventional grinding, creep feed grinding and CBN grinding/machining. These products are for metalworking operations that require practical and economical solutions for extending coolant life to help maintain maximum equipment performance.
Machining: Eriez Filters with Synthetic Permanent Media, Wedge Wire, Disposable Roll Media or Cellulose Pre-coated Microscreen can filter as low as oneµm and are available with low pressure flood coolant or high pressure directed coolant. These filters are specifically designed for drilling, milling, boring and turning operations that require significant volumes of flood coolant to move chips from the work area to the coolant sump. Modern machine tools now operate at higher speeds and increased feed rates, intensifying the need for high pressure clean coolant at the tool. Eriez has experience with scalping conveyors used as a pre-filter for large volume and difficult chips. The company has designed mounted filters fed by in-ground flume and floor mounted systems fed by overhead pipes using its custom Chip Transfer Sumps.
Conventional Grinding: Centerless, ID/OD, surface, form and other types of conventional grinding are ideal applications for Eriez filters. For flow rates of 40 GPM to 1200 GPM and filtration to 10µm, the Permanent Media Vacuum Filtration System offers the most advantages over other types of filters available today. The Star Filter handles applications requiring finer filtration to oneµm and/or higher flow rates to 6000 GPM.
Creep Feed Grinding: The Company has been building vacuum filters for creep feed grinding applications since 1986. Eriez Hydroflow supplied the industry's first central system for creep feed grinding in 1990, servicing 20 large Blohm Grinding Cells with a total flow requirement in excess of 2000 GPM.
CBN Grinding/Machining: Perhaps the fastest growing and most difficult filtration application in modern metal working is the CBN Grinding/Superabrasive Machining process. This high-speed process of metal removal requires the use of heavy oils at very high pressure (up to 1000 PSI), resulting in aeration and cavitation problems. Plus, the hard nature of the CBN produces swarf with very little particle size distribution, resulting in blinding and short cycling.
Contact Details
Related Glossary Terms
- boring
boring
Enlarging a hole that already has been drilled or cored. Generally, it is an operation of truing the previously drilled hole with a single-point, lathe-type tool. Boring is essentially internal turning, in that usually a single-point cutting tool forms the internal shape. Some tools are available with two cutting edges to balance cutting forces.
- coolant
coolant
Fluid that reduces temperature buildup at the tool/workpiece interface during machining. Normally takes the form of a liquid such as soluble or chemical mixtures (semisynthetic, synthetic) but can be pressurized air or other gas. Because of water’s ability to absorb great quantities of heat, it is widely used as a coolant and vehicle for various cutting compounds, with the water-to-compound ratio varying with the machining task. See cutting fluid; semisynthetic cutting fluid; soluble-oil cutting fluid; synthetic cutting fluid.
- cubic boron nitride ( CBN)
cubic boron nitride ( CBN)
Crystal manufactured from boron nitride under high pressure and temperature. Used to cut hard-to-machine ferrous and nickel-base materials up to 70 HRC. Second hardest material after diamond. See superabrasive tools.
- feed
feed
Rate of change of position of the tool as a whole, relative to the workpiece while cutting.
- gang cutting ( milling)
gang cutting ( milling)
Machining with several cutters mounted on a single arbor, generally for simultaneous cutting.
- grinding
grinding
Machining operation in which material is removed from the workpiece by a powered abrasive wheel, stone, belt, paste, sheet, compound, slurry, etc. Takes various forms: surface grinding (creates flat and/or squared surfaces); cylindrical grinding (for external cylindrical and tapered shapes, fillets, undercuts, etc.); centerless grinding; chamfering; thread and form grinding; tool and cutter grinding; offhand grinding; lapping and polishing (grinding with extremely fine grits to create ultrasmooth surfaces); honing; and disc grinding.
- metalworking
metalworking
Any manufacturing process in which metal is processed or machined such that the workpiece is given a new shape. Broadly defined, the term includes processes such as design and layout, heat-treating, material handling and inspection.
- milling
milling
Machining operation in which metal or other material is removed by applying power to a rotating cutter. In vertical milling, the cutting tool is mounted vertically on the spindle. In horizontal milling, the cutting tool is mounted horizontally, either directly on the spindle or on an arbor. Horizontal milling is further broken down into conventional milling, where the cutter rotates opposite the direction of feed, or “up” into the workpiece; and climb milling, where the cutter rotates in the direction of feed, or “down” into the workpiece. Milling operations include plane or surface milling, endmilling, facemilling, angle milling, form milling and profiling.
- swarf
swarf
Metal fines and grinding wheel particles generated during grinding.
- turning
turning
Workpiece is held in a chuck, mounted on a face plate or secured between centers and rotated while a cutting tool, normally a single-point tool, is fed into it along its periphery or across its end or face. Takes the form of straight turning (cutting along the periphery of the workpiece); taper turning (creating a taper); step turning (turning different-size diameters on the same work); chamfering (beveling an edge or shoulder); facing (cutting on an end); turning threads (usually external but can be internal); roughing (high-volume metal removal); and finishing (final light cuts). Performed on lathes, turning centers, chucking machines, automatic screw machines and similar machines.