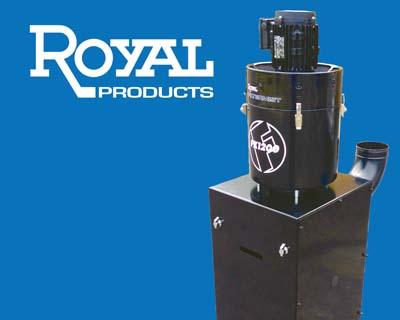
Royal Products' new Filtermist Ultra is a portable solution for oil mist and smoke that combines Filtermist with cyclonic technology to remove additional pollutants. The system is top-mounted on a mobile cart with securely locking casters. Its efficient design delivers a small footprint that eliminates the need for additional stands or brackets.
"Filtermist Ultra fits conveniently behind the chip conveyor on most machines," said Royal Products Vice President of Marketing Tom Sheridan. "It is ideal for retrofitting an existing production line or incorporating into a new one. And Filtermist Ultra works efficiently for nearly every application, including: turning, milling, grinding and cast-iron machining."
The system was designed to simplify maintenance and lower manufacturing costs. The internal cyclone particulate removal improves particle separation, so clean air can be exhausted back to the factory floor. That helps lower the expense of heating and cooling the facility. Filtermist Ultra can operate continuously, because it self-drains back to the machine tool coolant sump. This process also reduces coolant costs by recycling it, rather than venting it to the atmosphere.
The company says Filtermist Ultra exceeds current and proposed OSHA and NIOSH safety regulations, making it a good investment for the future. Removing oil mist reduces the risk of accidents caused by slippery residue. Inhaling oil mist is potentially dangerous to the lungs and larynx. The pollution may be harmful to skin as well. Oil mist deposits also create a fire hazard.
By preventing oily residues, Filtermist Ultra reduces the time and cost of cleaning exposed surfaces. It also eliminates build-up that can interfere with equipment.
Filtermist Ultra is driven by Royal Products FX-1200, enabling it to handle a wide range of machine tool types and sizes. It's ideal for machines with an internal volume greater than 60 cu. ft. The unit measures 18-inches by 20-inches and includes 20-feet of six-inch diameter ducting.
An all-inclusive system, it can be ordered with one SKU. That includes the model FX-1200 Filtermist unit, mobile cart, integral cyclone, oil return hose, ducting, six-inch diameter flange adapter, and two six-inch diameter ducting clamps. Other available products include a starter box kit with an optional low- or high-voltage motor starter, NEMA 12 box, input and output cables, and a turn-lock connector. An optional after-filter is available for collecting dry smoke and very fine mist particles.
Contact Details
Related Glossary Terms
- coolant
coolant
Fluid that reduces temperature buildup at the tool/workpiece interface during machining. Normally takes the form of a liquid such as soluble or chemical mixtures (semisynthetic, synthetic) but can be pressurized air or other gas. Because of water’s ability to absorb great quantities of heat, it is widely used as a coolant and vehicle for various cutting compounds, with the water-to-compound ratio varying with the machining task. See cutting fluid; semisynthetic cutting fluid; soluble-oil cutting fluid; synthetic cutting fluid.
- gang cutting ( milling)
gang cutting ( milling)
Machining with several cutters mounted on a single arbor, generally for simultaneous cutting.
- grinding
grinding
Machining operation in which material is removed from the workpiece by a powered abrasive wheel, stone, belt, paste, sheet, compound, slurry, etc. Takes various forms: surface grinding (creates flat and/or squared surfaces); cylindrical grinding (for external cylindrical and tapered shapes, fillets, undercuts, etc.); centerless grinding; chamfering; thread and form grinding; tool and cutter grinding; offhand grinding; lapping and polishing (grinding with extremely fine grits to create ultrasmooth surfaces); honing; and disc grinding.
- milling
milling
Machining operation in which metal or other material is removed by applying power to a rotating cutter. In vertical milling, the cutting tool is mounted vertically on the spindle. In horizontal milling, the cutting tool is mounted horizontally, either directly on the spindle or on an arbor. Horizontal milling is further broken down into conventional milling, where the cutter rotates opposite the direction of feed, or “up” into the workpiece; and climb milling, where the cutter rotates in the direction of feed, or “down” into the workpiece. Milling operations include plane or surface milling, endmilling, facemilling, angle milling, form milling and profiling.
- turning
turning
Workpiece is held in a chuck, mounted on a face plate or secured between centers and rotated while a cutting tool, normally a single-point tool, is fed into it along its periphery or across its end or face. Takes the form of straight turning (cutting along the periphery of the workpiece); taper turning (creating a taper); step turning (turning different-size diameters on the same work); chamfering (beveling an edge or shoulder); facing (cutting on an end); turning threads (usually external but can be internal); roughing (high-volume metal removal); and finishing (final light cuts). Performed on lathes, turning centers, chucking machines, automatic screw machines and similar machines.