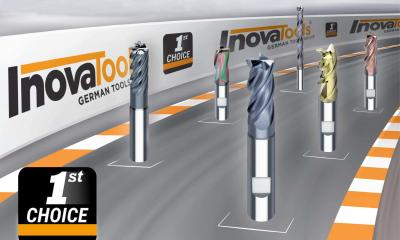
Tool manufacturer Inovatools supports the metalworking industry with a wide range of tools for all manner of cutting challenges. With its First Choice Inovatools, the tool specialist from Haunstetten near Kinding in Germany is now giving users the opportunity to find tailor-made tools for their specific cutting requirement quickly and easily. One example is machining stainless steel.
In addition to in-person technical advice, First Choice Inovatools represent a highly effective means of quickly identifying top tools in the Inovatools online shop or in the main catalog. This enables users to search by the application and cutting values thanks to the INOCUT cutting data program; alternatively, the tools are marked as “First Choice” in the complete catalog.
“To help you to find what you are looking for quickly when searching for a tool that is optimized for your application, Inovatools has preselected a number of top products and marked them as special recommendations,” says Tobias Eckerle, product manager at Inovatools. “One of the things we are trying to achieve is to guide users to the advanced geometries and technologies that are most suitable for them via the fastest possible route. Ultimately, that helps them to reduce production times and deliver top surface quality while benefiting from a longer service life, for example. Tool and machinery costs are reduced as a result.”
INOX, Nirosta, chromium steel, VA steel, rust-free steel, nickel-chromium steel and so on – there are many names for stainless steel. And just as the names for this material group are hugely diverse, so too are the specific characteristics depending on the chromium, nickel, titanium and molybdenum content. On the one hand, this defines the area of application; on the other hand, these supplements make HPC cutting complex and difficult.
Depending on the microstructure and alloy content of the material, the milling cutters and drills used struggle with built-up edges, abrasiveness, workhardening, edge zone hardening and high temperatures in the intervention zone, for example. Tools from Inovatools are adapted to the relevant requirements in terms of the substrate, cutting geometry, chip removal and coating and achieve the best results when it comes to roughing and finishing, for instance, with their specific cutting and cooling strategy.
According to Eckerle, “The top products from Inovatools bring the desired added value in terms of endurance and speed to HPC roughing and finishing processes. Such as the FightMax INOX milling cutter in a shorter or longer, free-length variant.”
In the FightMax INOX, Inovatools uses a balanced mixing ratio of special ultrafine-grain carbide. The tool has an unevenly split and unevenly twisted geometry with highly polished chip space. This gives the tool the necessary performance, ensures quiet, vibration-free concentricity, and guarantees quick and reliable chip removal. This is supported by the DUOCON smooth high-performance coating, which also gives the FightMax INOX protection and the necessary stability. Inovatools achieves extreme edge stability through the defined cutting edge rounding. A further special feature of the FightMax tools is the face that is specially optimized for ramping.
“These design benefits combined with the narrowest of production tolerances yield very long service lives and top surface quality, even at high feed rates and cutting speeds,” says Tobias Eckerle.
Another First Choice recommendation for machining stainless steel, for roughing with a reduced chip volume and lower cutting forces, for example, is the QuickMax SC roughing endmill. Special features include the optimized chip groove and the special entwined profile. The tool also scores points for achieving exceptional cutting rates while reliably removing the short, tightly rolled chips.
When it comes to trochoidal milling, the INOX SC endmill is in pole position. The tool demonstrates its strengths when taking on tasks such as complex contouring and, above all, deep cross-sections. The reduced cutting forces during slot milling allow smaller diameters to be used with large cutting lengths, which saves not only time, but above all costs.
As Eckerle comments, “Via First Choice, we recommend a multitooth milling cutter such as the StarMax Superfinish for finishing and, for drilling stainless steel, the SpeedMax universal high-performance twist drill, which centers itself precisely and can be operated at high feed rates.”
Contact Details
Related Glossary Terms
- centers
centers
Cone-shaped pins that support a workpiece by one or two ends during machining. The centers fit into holes drilled in the workpiece ends. Centers that turn with the workpiece are called “live” centers; those that do not are called “dead” centers.
- endmill
endmill
Milling cutter held by its shank that cuts on its periphery and, if so configured, on its free end. Takes a variety of shapes (single- and double-end, roughing, ballnose and cup-end) and sizes (stub, medium, long and extra-long). Also comes with differing numbers of flutes.
- feed
feed
Rate of change of position of the tool as a whole, relative to the workpiece while cutting.
- gang cutting ( milling)
gang cutting ( milling)
Machining with several cutters mounted on a single arbor, generally for simultaneous cutting.
- hardening
hardening
Process of increasing the surface hardness of a part. It is accomplished by heating a piece of steel to a temperature within or above its critical range and then cooling (or quenching) it rapidly. In any heat-treatment operation, the rate of heating is important. Heat flows from the exterior to the interior of steel at a definite rate. If the steel is heated too quickly, the outside becomes hotter than the inside and the desired uniform structure cannot be obtained. If a piece is irregular in shape, a slow heating rate is essential to prevent warping and cracking. The heavier the section, the longer the heating time must be to achieve uniform results. Even after the correct temperature has been reached, the piece should be held at the temperature for a sufficient period of time to permit its thickest section to attain a uniform temperature. See workhardening.
- metalworking
metalworking
Any manufacturing process in which metal is processed or machined such that the workpiece is given a new shape. Broadly defined, the term includes processes such as design and layout, heat-treating, material handling and inspection.
- microstructure
microstructure
Structure of a metal as revealed by microscopic examination of the etched surface of a polished specimen.
- milling
milling
Machining operation in which metal or other material is removed by applying power to a rotating cutter. In vertical milling, the cutting tool is mounted vertically on the spindle. In horizontal milling, the cutting tool is mounted horizontally, either directly on the spindle or on an arbor. Horizontal milling is further broken down into conventional milling, where the cutter rotates opposite the direction of feed, or “up” into the workpiece; and climb milling, where the cutter rotates in the direction of feed, or “down” into the workpiece. Milling operations include plane or surface milling, endmilling, facemilling, angle milling, form milling and profiling.
- milling cutter
milling cutter
Loosely, any milling tool. Horizontal cutters take the form of plain milling cutters, plain spiral-tooth cutters, helical cutters, side-milling cutters, staggered-tooth side-milling cutters, facemilling cutters, angular cutters, double-angle cutters, convex and concave form-milling cutters, straddle-sprocket cutters, spur-gear cutters, corner-rounding cutters and slitting saws. Vertical cutters use shank-mounted cutting tools, including endmills, T-slot cutters, Woodruff keyseat cutters and dovetail cutters; these may also be used on horizontal mills. See milling.
- twist drill
twist drill
Most common type of drill, having two or more cutting edges, and having helical grooves adjacent thereto for the passage of chips and for admitting coolant to the cutting edges. Twist drills are used either for originating holes or for enlarging existing holes. Standard twist drills come in fractional sizes from 1¼16" to 11¼2", wire-gage sizes from 1 to 80, letter sizes A to Z and metric sizes.
- workhardening
workhardening
Tendency of all metals to become harder when they are machined or subjected to other stresses and strains. This trait is particularly pronounced in soft, low-carbon steel or alloys containing nickel and manganese—nonmagnetic stainless steel, high-manganese steel and the superalloys Inconel and Monel.