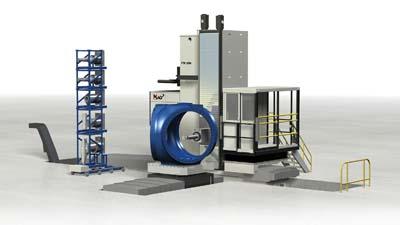
MAG's new FTR 3500 floor-type horizontal boring mill (HBM) is a versatile, mid-sized job-shop machine, capable of a full 2 m reach inside parts with a ram-supported spindle. The workhorse machine tool is ideal for "heavy metal" milling, as well as precision multi-axis contouring, boring, drilling and tapping on large parts for the construction, oil field and wind energy industries.
The machine's collinear ram, made from ductile iron, adds a 1-meter W-axis reach to the spindle's existing 1-meter extension. It provides maximum rigidity for full-power cuts by minimizing spindle extension. The ram's 400 x 500mm cross section is ideally sized for extended reach with rigid support to enable the machine to perform additional operations, helping to reduce time-consuming large-part setups for faster cycle times and less work-in-process. The machine's Ram Displacement Compensation system uses a hydraulically actuated tension rod system to counteract the static loads of attachments, and control ram displacement caused by variations in ram extension and attachment weight.
Like all MAG boring mills, the FTR 3500 includes W and Z-axis thermal compensation software to dynamically offset spindle growth. The FTR 3500 is available in column heights of 2 to 5 meters (6.6 to 16.4 ft) in half-meter increments. Traveling-column design allows virtually unlimited X-axis travel for processing of large and long workpieces or multiple batch parts, while 20 m/min (787 ipm) rapid traverse rates reduce cycle times. The choice of spindle power trains includes two four-speed versions available with spindle diameters of 130 and 155mm (5 and 6 in). Available horsepower is 56 kW (75 hp).
The FTR 3500's rigid box welded column construction, wide way spreads on the column and runway, and steel runway fabrication provide exceptional rigidity and durability for the most demanding machining requirements, resisting deflection and minimizing vibrations. Linear positioning accuracy is 0.015mm (0.0006 in) and repeatability is 0.008mm (0.0003 in). Precision roller packs on X, Y and W axes, provide stability, low friction, durability and maintainability for high-performance machining. The Y-axis has a 100mm (3.94 in) preloaded, anti-friction ballscrew, while the Z and W axes use a 63mm (2.5 in) diameter ballscrew. The X-axis is driven by an electrically-preloaded rack and pinion system. Modular design allows economical customization of the FTR 3500, along with industry's fastest machine build and delivery. The machine can be fitted with choice of travels, headstocks, spindle diameters and spindle power, controls, coolant systems, workholding and tool magazines.
Front-end options include a range of indexing and rotary tables, auxiliary slides and floor plates. An optional attachment rack enables storage and quick change of contouring heads, programmable boring bars, right angle heads and more to speed production. Optional cartridge-style ram allows for a fixed attachment or attachment changing operations.
"Green" features of the FTR 3500 include a minimal air-oil lubrication system in the headstock, eliminating the need for chillers and ancillary equipment for lower overall ownership cost. Ergonomic enhancements include operator platforms with X-, Y- and W-travel options, and operator convenience packages that include lighting, power, air and workbench options. Custom workzone enclosures are also available. The service areas of the machine are designed using Visual Uptime Management principles to simplify maintenance and maximize machine availability. Clear, color-coded labeling and note plates assist in accessing and maintaining key utilities for the machine and control.
Contact Details
Related Glossary Terms
- boring
boring
Enlarging a hole that already has been drilled or cored. Generally, it is an operation of truing the previously drilled hole with a single-point, lathe-type tool. Boring is essentially internal turning, in that usually a single-point cutting tool forms the internal shape. Some tools are available with two cutting edges to balance cutting forces.
- coolant
coolant
Fluid that reduces temperature buildup at the tool/workpiece interface during machining. Normally takes the form of a liquid such as soluble or chemical mixtures (semisynthetic, synthetic) but can be pressurized air or other gas. Because of water’s ability to absorb great quantities of heat, it is widely used as a coolant and vehicle for various cutting compounds, with the water-to-compound ratio varying with the machining task. See cutting fluid; semisynthetic cutting fluid; soluble-oil cutting fluid; synthetic cutting fluid.
- gang cutting ( milling)
gang cutting ( milling)
Machining with several cutters mounted on a single arbor, generally for simultaneous cutting.
- milling
milling
Machining operation in which metal or other material is removed by applying power to a rotating cutter. In vertical milling, the cutting tool is mounted vertically on the spindle. In horizontal milling, the cutting tool is mounted horizontally, either directly on the spindle or on an arbor. Horizontal milling is further broken down into conventional milling, where the cutter rotates opposite the direction of feed, or “up” into the workpiece; and climb milling, where the cutter rotates in the direction of feed, or “down” into the workpiece. Milling operations include plane or surface milling, endmilling, facemilling, angle milling, form milling and profiling.
- milling machine ( mill)
milling machine ( mill)
Runs endmills and arbor-mounted milling cutters. Features include a head with a spindle that drives the cutters; a column, knee and table that provide motion in the three Cartesian axes; and a base that supports the components and houses the cutting-fluid pump and reservoir. The work is mounted on the table and fed into the rotating cutter or endmill to accomplish the milling steps; vertical milling machines also feed endmills into the work by means of a spindle-mounted quill. Models range from small manual machines to big bed-type and duplex mills. All take one of three basic forms: vertical, horizontal or convertible horizontal/vertical. Vertical machines may be knee-type (the table is mounted on a knee that can be elevated) or bed-type (the table is securely supported and only moves horizontally). In general, horizontal machines are bigger and more powerful, while vertical machines are lighter but more versatile and easier to set up and operate.
- modular design ( modular construction)
modular design ( modular construction)
Manufacturing of a product in subassemblies that permits fast and simple replacement of defective assemblies and tailoring of the product for different purposes. See interchangeable parts.
- rapid traverse
rapid traverse
Movement on a CNC mill or lathe that is from point to point at full speed but, usually, without linear interpolation.
- tapping
tapping
Machining operation in which a tap, with teeth on its periphery, cuts internal threads in a predrilled hole having a smaller diameter than the tap diameter. Threads are formed by a combined rotary and axial-relative motion between tap and workpiece. See tap.