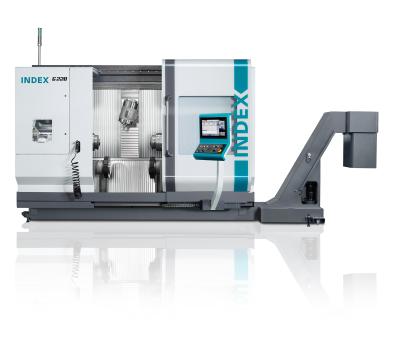
INDEX has announced the release of next generation of its G220 turn-mill center. Incorporating the design principles introduced via the larger G320, G420 and G520 machines, the new G220 provides high flexibility to produce complex, small-to-medium-sized parts in a single setup.
The G Series’ design concept begins with a rigid, vibration-damping machine bed in a mineral cast block design. The machines combine optimal stability and damping properties with high dynamics and generously dimensioned linear guides in the X and Z axes.
The G220 features a Z-axis slide with a motorized milling spindle and hydrodynamically mounted Y/B axis arranged above the axis of rotation. The powerful milling spindle is available with an HSK-T63 interface with specs of 12,000 rpm, 60.3 hp (49 kW) and 53.1 ft lbs (72 Nm) at 25% DC, or an HSK-T40 interface with specs of 18,000 rpm, 25.5 hp (19 kW) and 22.1 ft lbs (30 Nm) at 25% DC. This facilitates a wide range of milling and drilling operations, and the machine is also capable of full 5-axis machining.
A tool magazine accommodating up to 139 tools feeds the milling spindle and offers incredibly easy setups. In addition to the traditional setup station at the front of the machine, the G220 offers access to the magazine’s two tool chains at the rear of the machine. This allows an operator to change tools on one chain while the other is in use, eliminating costly non-cutting time.
The G220 provides two tool turrets located at the bottom of the machine’s workspace. Each turret can move not just along the X and Z axes, but along the Y axis as well. Additionally, each of the turrets’ stations can be equipped with live tools for maximum flexibility.
Two identical, fluid-cooled spindles offer powerful, dynamic performances with 38.9 hp (29 kW) and 104.7 ft lbs (142 Nm) at 100% DC. Each spindle provides a spindle clearance of 3.0" (76 mm) and the machine accommodated a maximum turning length of 35.4" (900 mm).
The combination of the G220’s large workspace and positioning of the spindles and turrets allow for simultaneous machining with both the motorized milling spindle and both tool turrets at either spindle, with no risk of collision. This allows for greater throughput and significant cycle time reductions.
To further enhance productivity, INDEX offers a variety of automation solutions for the G220. Especially notable is the new MBL 76 bar loader. Tailored specifically to optimize performance with the new machine, this bar loader offers excellent damping properties and is electrically powered with no hydraulic components.
Additionally, the G220 is optionally available with an integrated gantry loader with a double gripper or the iXcenter robot cell to load and unload flange or shaft-style parts.
The G220 uses a modified Siemens S 840D SL control, which offers user-friendly operation via INDEX’s iXpanel interface.
Contact Details
Related Glossary Terms
- clearance
clearance
Space provided behind a tool’s land or relief to prevent rubbing and subsequent premature deterioration of the tool. See land; relief.
- gang cutting ( milling)
gang cutting ( milling)
Machining with several cutters mounted on a single arbor, generally for simultaneous cutting.
- milling
milling
Machining operation in which metal or other material is removed by applying power to a rotating cutter. In vertical milling, the cutting tool is mounted vertically on the spindle. In horizontal milling, the cutting tool is mounted horizontally, either directly on the spindle or on an arbor. Horizontal milling is further broken down into conventional milling, where the cutter rotates opposite the direction of feed, or “up” into the workpiece; and climb milling, where the cutter rotates in the direction of feed, or “down” into the workpiece. Milling operations include plane or surface milling, endmilling, facemilling, angle milling, form milling and profiling.
- turning
turning
Workpiece is held in a chuck, mounted on a face plate or secured between centers and rotated while a cutting tool, normally a single-point tool, is fed into it along its periphery or across its end or face. Takes the form of straight turning (cutting along the periphery of the workpiece); taper turning (creating a taper); step turning (turning different-size diameters on the same work); chamfering (beveling an edge or shoulder); facing (cutting on an end); turning threads (usually external but can be internal); roughing (high-volume metal removal); and finishing (final light cuts). Performed on lathes, turning centers, chucking machines, automatic screw machines and similar machines.