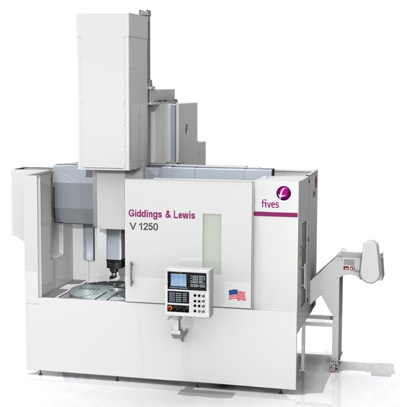
The new Giddings & Lewis V Series from Fives Machining Systems is a versatile line of vertical turning centers for shops looking for a dependable, multi-purpose lathe capable of handling a wide range of parts, including pumps, valves, gears, bearings, compressors, wheel hubs, jet engine housings and more.
All six models, with table sizes ranging from 800mm to 2500mm, have a hydrostatic ram that adds rigidity for heavy cutting and produce less friction for improved part finish. The hydrostatic wear-free guides require less maintenance. The infinitely adjustable cross rail is a programmable positioning axis able to handle a wide range of parts and minimize ram extension. Dual scale feedback delivers precision and ensures parallelism while the hydraulic cylinder elevation adds secure 1000 kN (225,000 lb) of mechanical clamping force per side.
"The V Series is engineered to be flexible, reliable and affordable in response to feedback from our job shop customers," said Brad Nelson, V Series Product Manager at Fives Giddings & Lewis. "All models have a compact footprint, and there is no requirement for special foundations, so the machine can be easily relocated, if necessary. We encourage customers to compare the capabilities and value of the V Series, and we're confident these new machines will impress."
The Giddings & Lewis VLock tooling system provides a stiff interface for modular tooling adaptors, long cutting tools and the optional heavy-duty, right-angle milling attachment. Modular turning tools more than double the taper stiffness at loads up to 1800 Nm," added Nelson. Standard modular tools offer significant savings over the proprietary vertical lathe tooling offered on most vertical lathes, he added. "Modular tools are also lighter, easier and safer to handle, requiring less time to maintain."
Through-the-tool coolant and 8 bar (116 psi) flood coolant is standard, as is a 12-position tool storage disk. Options include 70-bar (1015-psi) high-pressure coolant and an 18-tool storage disk. Other options include tool and part probes to increase utilization and ensure part quality, and enclosures from standard to fully enclosed.
The V Series is designed and built at the Fives Giddings & Lewis plant in Fond du Lac, Wis., and stays true to Giddings & Lewis design traditions, with solid cast iron base construction and versatility offered by optional live spindle attachments and a C-axis table. "By adding the V Series, starting with 800mm tables, to our existing VTC Series of vertical turning centers, with swings up to 9 meters, we are positioned to offer manufacturers the broadest and best range of turning solutions, said Kevin Lichtenberg, Fives Giddings & Lewis Vice President and General Manager.
Contact Details
Related Glossary Terms
- centers
centers
Cone-shaped pins that support a workpiece by one or two ends during machining. The centers fit into holes drilled in the workpiece ends. Centers that turn with the workpiece are called “live” centers; those that do not are called “dead” centers.
- coolant
coolant
Fluid that reduces temperature buildup at the tool/workpiece interface during machining. Normally takes the form of a liquid such as soluble or chemical mixtures (semisynthetic, synthetic) but can be pressurized air or other gas. Because of water’s ability to absorb great quantities of heat, it is widely used as a coolant and vehicle for various cutting compounds, with the water-to-compound ratio varying with the machining task. See cutting fluid; semisynthetic cutting fluid; soluble-oil cutting fluid; synthetic cutting fluid.
- gang cutting ( milling)
gang cutting ( milling)
Machining with several cutters mounted on a single arbor, generally for simultaneous cutting.
- lathe
lathe
Turning machine capable of sawing, milling, grinding, gear-cutting, drilling, reaming, boring, threading, facing, chamfering, grooving, knurling, spinning, parting, necking, taper-cutting, and cam- and eccentric-cutting, as well as step- and straight-turning. Comes in a variety of forms, ranging from manual to semiautomatic to fully automatic, with major types being engine lathes, turning and contouring lathes, turret lathes and numerical-control lathes. The engine lathe consists of a headstock and spindle, tailstock, bed, carriage (complete with apron) and cross slides. Features include gear- (speed) and feed-selector levers, toolpost, compound rest, lead screw and reversing lead screw, threading dial and rapid-traverse lever. Special lathe types include through-the-spindle, camshaft and crankshaft, brake drum and rotor, spinning and gun-barrel machines. Toolroom and bench lathes are used for precision work; the former for tool-and-die work and similar tasks, the latter for small workpieces (instruments, watches), normally without a power feed. Models are typically designated according to their “swing,” or the largest-diameter workpiece that can be rotated; bed length, or the distance between centers; and horsepower generated. See turning machine.
- milling
milling
Machining operation in which metal or other material is removed by applying power to a rotating cutter. In vertical milling, the cutting tool is mounted vertically on the spindle. In horizontal milling, the cutting tool is mounted horizontally, either directly on the spindle or on an arbor. Horizontal milling is further broken down into conventional milling, where the cutter rotates opposite the direction of feed, or “up” into the workpiece; and climb milling, where the cutter rotates in the direction of feed, or “down” into the workpiece. Milling operations include plane or surface milling, endmilling, facemilling, angle milling, form milling and profiling.
- modular tooling
modular tooling
1. Tooling system comprised of standardized tools and toolholders. 2. Devices that allow rapid mounting and replacement of tools. Commonly used with carousel toolchangers and other computerized machining operations. See toolchanger; toolholder.
- stiffness
stiffness
1. Ability of a material or part to resist elastic deflection. 2. The rate of stress with respect to strain; the greater the stress required to produce a given strain, the stiffer the material is said to be. See dynamic stiffness; static stiffness.
- turning
turning
Workpiece is held in a chuck, mounted on a face plate or secured between centers and rotated while a cutting tool, normally a single-point tool, is fed into it along its periphery or across its end or face. Takes the form of straight turning (cutting along the periphery of the workpiece); taper turning (creating a taper); step turning (turning different-size diameters on the same work); chamfering (beveling an edge or shoulder); facing (cutting on an end); turning threads (usually external but can be internal); roughing (high-volume metal removal); and finishing (final light cuts). Performed on lathes, turning centers, chucking machines, automatic screw machines and similar machines.