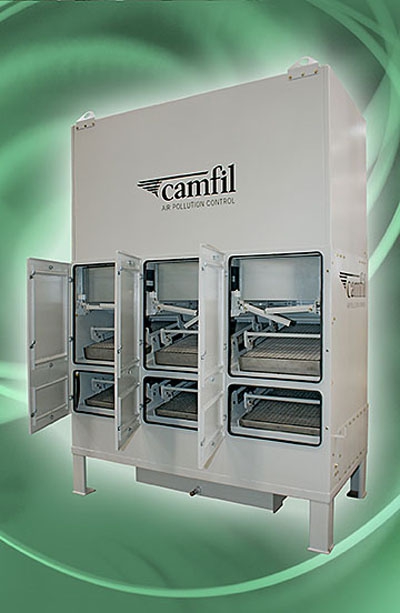
A new line of Handte EM Profi emulsion mist collectors from Camfil Air Pollution Control (APC) offers the highest available collection efficiencies, plus the ability to run "24/7" for reduced maintenance, service ease and lower operating costs. The units can handle the heaviest loads encountered in industry to clean up contaminants generated during milling, drilling, tapping, turning, grinding and other machining processes that utilize emulsion mist coolants.
The EM Profi collector uses long-life coarse and fine filter demisters followed by a final-stage HEPA filter with combined efficiencies of 99.9 percent on particles of 0.3µm and larger. This is much higher than capture efficiencies achieved with fiberglass V-bag filters, which lose efficiency as media becomes saturated. A patented automatic sprayer counteracts emulsion clumping, ensuring that the separators can operate "24/7" almost maintenance-free.
During routine annual maintenance, the unit is easily serviced from the ground by a single technician, eliminating extra manpower and lift equipment. Service life between change-outs is up to six years for demister filters and two years for HEPA filters. Large maintenance doors and quick-clamping elements facilitate fast, tool-less filter replacement. Due to these features, Handte EM Profi collectors achieve substantial savings through reduced downtime, longer change-out cycles and increased productivity and reliability.
Sturdy modular construction is another benefit. Basic modules can handle air volumes from 1,700 to 8,000 cfm, with a wide range of accessories and configurations for optimum flexibility. Modules can be combined to accommodate larger airflow requirements. Small space-saving models are also offered for low airflow applications of 500 to 1,400 cfm.
Contact Details
Related Glossary Terms
- emulsion
emulsion
Suspension of one liquid in another, such as oil in water.
- gang cutting ( milling)
gang cutting ( milling)
Machining with several cutters mounted on a single arbor, generally for simultaneous cutting.
- grinding
grinding
Machining operation in which material is removed from the workpiece by a powered abrasive wheel, stone, belt, paste, sheet, compound, slurry, etc. Takes various forms: surface grinding (creates flat and/or squared surfaces); cylindrical grinding (for external cylindrical and tapered shapes, fillets, undercuts, etc.); centerless grinding; chamfering; thread and form grinding; tool and cutter grinding; offhand grinding; lapping and polishing (grinding with extremely fine grits to create ultrasmooth surfaces); honing; and disc grinding.
- milling
milling
Machining operation in which metal or other material is removed by applying power to a rotating cutter. In vertical milling, the cutting tool is mounted vertically on the spindle. In horizontal milling, the cutting tool is mounted horizontally, either directly on the spindle or on an arbor. Horizontal milling is further broken down into conventional milling, where the cutter rotates opposite the direction of feed, or “up” into the workpiece; and climb milling, where the cutter rotates in the direction of feed, or “down” into the workpiece. Milling operations include plane or surface milling, endmilling, facemilling, angle milling, form milling and profiling.
- modular design ( modular construction)
modular design ( modular construction)
Manufacturing of a product in subassemblies that permits fast and simple replacement of defective assemblies and tailoring of the product for different purposes. See interchangeable parts.
- tapping
tapping
Machining operation in which a tap, with teeth on its periphery, cuts internal threads in a predrilled hole having a smaller diameter than the tap diameter. Threads are formed by a combined rotary and axial-relative motion between tap and workpiece. See tap.
- turning
turning
Workpiece is held in a chuck, mounted on a face plate or secured between centers and rotated while a cutting tool, normally a single-point tool, is fed into it along its periphery or across its end or face. Takes the form of straight turning (cutting along the periphery of the workpiece); taper turning (creating a taper); step turning (turning different-size diameters on the same work); chamfering (beveling an edge or shoulder); facing (cutting on an end); turning threads (usually external but can be internal); roughing (high-volume metal removal); and finishing (final light cuts). Performed on lathes, turning centers, chucking machines, automatic screw machines and similar machines.