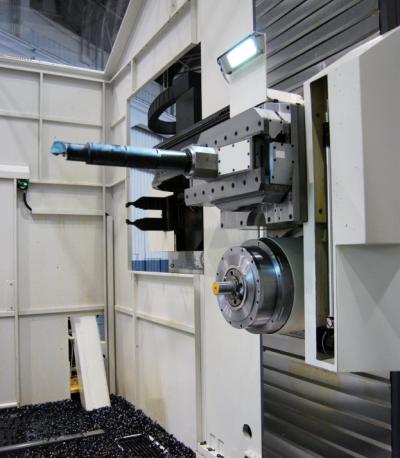
Fives brings the combination live spindle and integrated contouring head (ICH) to its Cincinnati MEGA and Giddings & Lewis HMC Series horizontal machining centers, for expanded processing flexibility and dramatically reduced workpiece transfers and setups, with improved accuracy. The ICH's 220-mm (8.7-in) U-axis slide stroke provides the ability to produce small- or large-diameter features without head changing or manual intervention, allowing complex features to be machined in one setup with reduced cycle time and labor. The contouring head can produce features such as bottle bores, valve seats, seal faces, phonographic sealing surfaces, O-ring grooves, straight/tapered threads, chamfers, and external profiles. It is ideal for single setup, rough and finish machining of any large parts that combine bored, milled and turned features.
The ICH is located immediately above the machine's main spindle, but slightly offset in the Y and W/Z axes to avoid tool interference. The 45-kW/60-hp (S6-40%) contouring spindle for HMCs handles parts up to 540 mm (21.3 in) ID and 340 mm (13.4 in) OD. It is available with standard Kennametal KM80 or Sandvik Coromant Capto C8 tool interfaces, and accommodates tools as long as 600 mm (23.6 in), weighing up to 18 kg (39.6 lb). Tools are loaded via the machine's automatic toolchanger for faster processing without operator involvement. The W/Z-axis live boring spindles can use 50-taper tools. With an auto coupler, the Giddings & Lewis HMC Series handles programmable boring bars up to 750 mm (29.5 in) long and 50 kg (110 lb). Live spindle travel is 800 mm (31.5 in) for all machining center models.
"The combination of the U-axis head and main W/Z-axis milling/boring spindle provides boring and turning capabilities in a single multitasking machine," said Fives Cincinnati Product Manager Ken Wichman. "The range, power, accuracy and tool-handling capability of the ICH provide a much wider range of processing capabilities than possible with contouring attachments or other options. The integrated head is much more rigid than attachments bolted on or held by the spindle taper, resulting in superior part quality, surface finish and dimensional accuracy.”
A touch probe can be used in the boring spindle or on the HMC Series an optional auxiliary probe is available for in-process or post-process measurement of part features. Standard services, such as coolant supply, are plumbed through the contouring head to eliminate manual intervention and ensure maximum tool life.
Contact Details
Related Glossary Terms
- automatic toolchanger
automatic toolchanger
Mechanism typically included in a machining center that, on the appropriate command, removes one cutting tool from the spindle nose and replaces it with another. The changer restores the used tool to the magazine and selects and withdraws the next desired tool from the storage magazine. The changer is controlled by a set of prerecorded/predetermined instructions associated with the part(s) to be produced.
- boring
boring
Enlarging a hole that already has been drilled or cored. Generally, it is an operation of truing the previously drilled hole with a single-point, lathe-type tool. Boring is essentially internal turning, in that usually a single-point cutting tool forms the internal shape. Some tools are available with two cutting edges to balance cutting forces.
- centers
centers
Cone-shaped pins that support a workpiece by one or two ends during machining. The centers fit into holes drilled in the workpiece ends. Centers that turn with the workpiece are called “live” centers; those that do not are called “dead” centers.
- coolant
coolant
Fluid that reduces temperature buildup at the tool/workpiece interface during machining. Normally takes the form of a liquid such as soluble or chemical mixtures (semisynthetic, synthetic) but can be pressurized air or other gas. Because of water’s ability to absorb great quantities of heat, it is widely used as a coolant and vehicle for various cutting compounds, with the water-to-compound ratio varying with the machining task. See cutting fluid; semisynthetic cutting fluid; soluble-oil cutting fluid; synthetic cutting fluid.
- inner diameter ( ID)
inner diameter ( ID)
Dimension that defines the inside diameter of a cavity or hole. See OD, outer diameter.
- machining center
machining center
CNC machine tool capable of drilling, reaming, tapping, milling and boring. Normally comes with an automatic toolchanger. See automatic toolchanger.
- outer diameter ( OD)
outer diameter ( OD)
Dimension that defines the exterior diameter of a cylindrical or round part. See ID, inner diameter.
- toolchanger
toolchanger
Carriage or drum attached to a machining center that holds tools until needed; when a tool is needed, the toolchanger inserts the tool into the machine spindle. See automatic toolchanger.
- turning
turning
Workpiece is held in a chuck, mounted on a face plate or secured between centers and rotated while a cutting tool, normally a single-point tool, is fed into it along its periphery or across its end or face. Takes the form of straight turning (cutting along the periphery of the workpiece); taper turning (creating a taper); step turning (turning different-size diameters on the same work); chamfering (beveling an edge or shoulder); facing (cutting on an end); turning threads (usually external but can be internal); roughing (high-volume metal removal); and finishing (final light cuts). Performed on lathes, turning centers, chucking machines, automatic screw machines and similar machines.