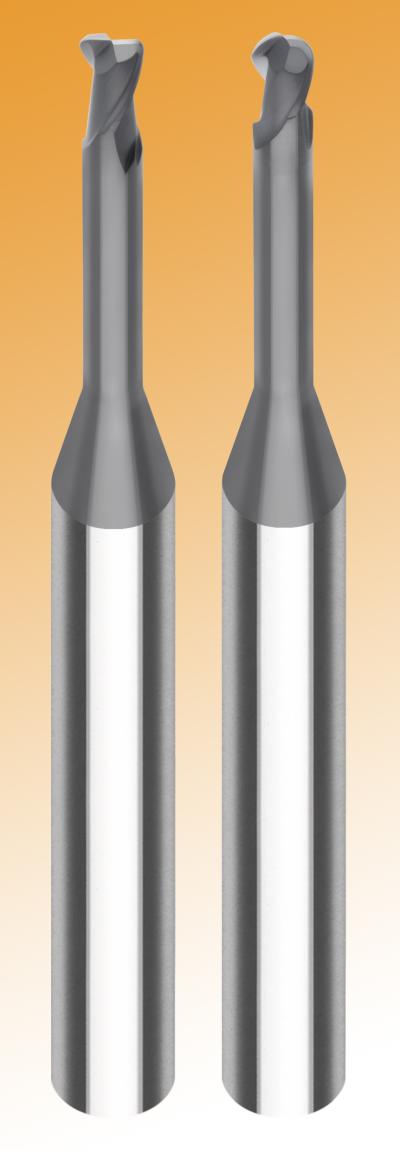
Diamond-coated carbide tools are perfect for the cost-effective machining of abrasive materials such as graphite and composites. With its extensive range of SC milling cutters, tool manufacturer Inovatools offers its HQ line for a diverse range of applications. Thanks to specially modified geometries and an ultrasmooth diamond coating, the high-precision HSC milling cutters can be used for machining composite materials and creating even highly complex 3D contours of the kind found on graphite molds and electrodes.
Thanks to its excellent thermal capacity, high chemical resistance and low expansion coefficient, graphite is frequently the material of choice in electrode production and mold construction. Since it does not warp or distort, graphite is perfect for ensuring excellent contour and dimensional stability. Since no burrs are left behind, the moldmaker does not have to perform time-consuming and expensive finishing work.
When cutting this highly abrasive material, conventional tools quickly reach their limits – after all, to machine graphite reliably and cost-effectively, high cutting speeds are essential for generating the extremely high level of friction required in the cutting zone. Tobias Eckerle, product manager at Inovatools, comments, “What's more, milling this brittle and highly abrasive material doesn’t create chips – instead, graphite particles fly off the material composite and strike the surface of the cutting edge at high speed. This impact wear and exposure to fine particles quickly take its toll on conventional tools, especially on the cutting surfaces and other exposed areas. In addition, this frictional heat has the effect of ‘baking’ the graphite particles, which leads to the formation of a built-up edge.”
Abrasion and, in particular, the temperatures generated in the intervention zone during cutting can cause significant problems for conventional milling cutters even during the machining of composites such as glass- or carbon-fiber-reinforced plastic. Take carbon-fiber-reinforced plastic, for example: The hard carbon causes extreme wear during cutting processes. In addition, the resin – which acts as a binder material – is often highly sensitive to even relatively small temperature increases. So if the frictional heat becomes excessive, the thermal stressing of the composites can cause individual layers to disintegrate or delamination in the milled area.
This is why Inovatools equips its HQ milling cutters with a special CVD diamond coating – after all, no other material is as hard and wear-resistant as diamond. Not only is it almost completely chemically inert at low and medium temperatures, but its minimal adhesion tendency and high thermal conductivity significantly boost the performance of cutting tools.
Eckerle explains, “Only by using high-quality, premium tools can cutters comply with narrow tolerance zones while milling materials quickly and cost-effectively. The diamond coating, which is specially tailored to our tools, is characterized by strong adhesion to the low-tension, warp-free carbide specially chosen for this application. Its unique material properties offer major potential for enhancing system performance during the machining of highly abrasive graphite and composite materials as well as nonferrous metals such as aluminum.”
Being extremely smooth, this diamond coating not only ensures excellent chip evacuation and the rapid removal of graphite particles, but also swiftly dissipates the cutting heat from the contact zone. This ensures not only highly reliable milling in dry machining processes, but also minimum lubrication. Eckerle adds, “Operators see crucial benefits thanks not least to the special, optimized geometry- and diameter-dependent layer thicknesses without any compromise on the sharpness of the cutting edges.”
Other benefits for operators include the high manufacturing quality of the tools, as evidenced in a range of quality-relevant cutting parameters. The end mills with radius tolerances of +/- 3 µm are ground with extreme precision, and the concentricity of the milling cutters is ≤ 5 µm.
According to Inovatools, in a comparison test involving the dry end milling of graphite EK85, the 12 mm HQ milling cutter exhibited much less wear than an uncoated tool and another diamond-coated milling cutter on the market. The service life was much higher than that of both comparison tools.
According to Eckerle, “Ongoing monitoring in tool manufacture – including of the coating – ensures the very highest quality throughout. Our extensive stock and flexible production capacities mean that we ensure instant availability without requiring our customers to place minimum order quantities.”
The tools from the HQ line are one example. Eckerle says, “We have flagged these tools as ‘First Choice Inovatools’ in the catalog and our online shop to help our customers quickly find what they need when looking for an application-oriented tool.”
Contact Details
Related Glossary Terms
- abrasive
abrasive
Substance used for grinding, honing, lapping, superfinishing and polishing. Examples include garnet, emery, corundum, silicon carbide, cubic boron nitride and diamond in various grit sizes.
- built-up edge ( BUE)
built-up edge ( BUE)
1. Permanently damaging a metal by heating to cause either incipient melting or intergranular oxidation. 2. In grinding, getting the workpiece hot enough to cause discoloration or to change the microstructure by tempering or hardening.
- chemical vapor deposition ( CVD)
chemical vapor deposition ( CVD)
High-temperature (1,000° C or higher), atmosphere-controlled process in which a chemical reaction is induced for the purpose of depositing a coating 2µm to 12µm thick on a tool’s surface. See coated tools; PVD, physical vapor deposition.
- composites
composites
Materials composed of different elements, with one element normally embedded in another, held together by a compatible binder.
- conventional milling ( up milling)
conventional milling ( up milling)
Cutter rotation is opposite that of the feed at the point of contact. Chips are cut at minimal thickness at the initial engagement of the cutter’s teeth with the workpiece and increase to a maximum thickness at the end of engagement. See climb milling.
- gang cutting ( milling)
gang cutting ( milling)
Machining with several cutters mounted on a single arbor, generally for simultaneous cutting.
- milling
milling
Machining operation in which metal or other material is removed by applying power to a rotating cutter. In vertical milling, the cutting tool is mounted vertically on the spindle. In horizontal milling, the cutting tool is mounted horizontally, either directly on the spindle or on an arbor. Horizontal milling is further broken down into conventional milling, where the cutter rotates opposite the direction of feed, or “up” into the workpiece; and climb milling, where the cutter rotates in the direction of feed, or “down” into the workpiece. Milling operations include plane or surface milling, endmilling, facemilling, angle milling, form milling and profiling.
- milling cutter
milling cutter
Loosely, any milling tool. Horizontal cutters take the form of plain milling cutters, plain spiral-tooth cutters, helical cutters, side-milling cutters, staggered-tooth side-milling cutters, facemilling cutters, angular cutters, double-angle cutters, convex and concave form-milling cutters, straddle-sprocket cutters, spur-gear cutters, corner-rounding cutters and slitting saws. Vertical cutters use shank-mounted cutting tools, including endmills, T-slot cutters, Woodruff keyseat cutters and dovetail cutters; these may also be used on horizontal mills. See milling.
- tolerance
tolerance
Minimum and maximum amount a workpiece dimension is allowed to vary from a set standard and still be acceptable.